steven, i like the school, the black looks great by itself...quick question, why did the masons not use jamb block at the m.o.'s? is it typical to install windows prior to finishing the brick veneer? i would think that it would make for tough finishing where brick and window meets, and that the mortar can be corrosive on the aluminum??
if by jamb block you mean bullnose, the block is bullnose at the interior corners but not the outside corners.
the windows themselves don't touch the cmu, held off by blocking, so mortar's corrosiveness at the windows shouldn't be an issue. (at the top, where mortar is likely to fall into the void, the flashing would catch it before it got onto the window itself. ....and they're supposed to clean out that fallen mortar off the flashing so that it's unencumbered: we'll see if it happens.)
it is common around here for the windows to go in before the masonry and it doesn't have any specific sequencing liabilities from what i can tell. allows for us to inspect all the flashing conditions and anchorage condition before the brick goes into place. the brick leaves a 1/4" - 3/8" reveal around the window perimeter which gets backer rod and caulk so that things can move independently as they need to.
haven't used that jamb block before but some reasons i might not are:
-i usu want to show the full dimension of the window frame both inside and out and it looks like that block would conceal it?
-the blocking mounted to the outside face of the block also serves to provide a 'stop' for the rigid insulation that will be attached to the wall, and a smooth place to -lay the window head flashing so that it avoids puncture.
-wouldn't you still use blocking, but just install it in that offset?
-what would the head block look like? if it's the same shape as the jamb block, what does that do to a bond beam design? if not, how do you deal with blocking?
-school construction has to be as economical as possible. that means using as few special shapes as possible. the fewer total shape-types the better.
these are just my initial thoughts, being unfamiliar with the jamb block type. i'll look into it further though, for sure. thanks for the heads up.
the portion of the block that is different provides the stop for the rigid insulation, that is the "tab" that sticks into the cavity. so your brick returns to masonry and not the blocking.
we started demolition on another one of my projects this week... the scope of work includes demo of two affordable housing buildings from the 1950s and the construction of 4 new affordable housing buildings...
hmm... not sure what happened with that last picture... here it is...
LB, you're absolutely right!!! those old buildings are awful... the new ones are going to be built to last... they'll have metal roofing, integrally colored block, pre-finished hardiplank, hollow core floor structure for the second floor, etc... the design is a sorta florida cracker style vernacular... i couldn't sell the housing department on a modern design... but they'll be nice for what they are...
and i'll add my usual full disclosure statement... i am not the design architect... i'm a capital improvements project manager for the city... the architect on this project (and the recreation center) is wannemacher russell architects
Ha! At my old firm we did a historic renovation on a church in Florida, its style was described by its congregants as "Cracker Gothic" which I always thought was hysterical - I guess "Cracker" is a recognized term for a vernacular style down there!
careful of pre-finished hardie plank....cause you can't blind nail it, and all the joints need to be caulked...and most important the silica....from the sawing...is NASTY...NASTY.. You will also notice an
unreal amount of chattering...when ever a cut is made....I would call
this material our next big mistake.
^^^and for all the reasons snooker mentioned above - cutting, caulking, toxicity, nail holes, etc - it's godawful expensive to get installed (at least by someone who knows what they're doing).
thanks snooker and steven... we have a fantastic contractor so i don't think that it will be an issue... but i'll keep a lookout for issues... although it is a bit more expensive up front it should save the city money in the long run since it won't have to be repainted every 5-10 years...
Was out driving around and stopped in to see how my social worker client was coming along with the neighborhood infill garage I designed for him. As you can see it is really his play house.
and
most recent pics of my Beverly Hills house...huge wood trellis...master bedroom (with steel moment frame)...pool room which cantileveres over the pool (concrete floor slab will have a sheet of water that will fall into the pool)...notice how the contractor completely fucked up the concrete
This is a follow-up to my May 16, 2007 post. I just created a punch list last week and we are getting some odds and ends cleared up. This was a great project to work on and a great learning experience. The client's budget was pretty small and becamse signficantly smaller once we had to make the building structural sound. It's amazing what one will uncover when you begin to remove 50 year old walls.
Here are some pics:
Standing on the mezzanine. (Please note the painted door on the far left wall. Sad face) We originally inteded for the high wall on the right to be OSB board; we changed the wall to be covered in sheet metal.
Mezzanine handrail detail
This is the library space. We kept the floor joists in place from the former floor that we removed above.
Conference room (Please note column pop outs on the far right wall)
Conference room column detail. We had some interesting old columns we discovered when we removed the existing walls. The client didn't have enough money to shore the floor above and place larger beams so we were stuck with these bad boys. We decided to enshrine them in glass
Uh-oh...I did the code research for this project. What's this I hear about a ladder rule? It doesn't ring a bell. Please educate me. Anyway, it passed codes for the building permit and we received the occupancy permit after the final codes walk-through three weeks ago. Was this something that they overlooked as well? We are under IBC 2006.
Vado, I'm working on your CD right now. This very second.
Liberty, it's Shaw carpet. Nice color, great texture. We pushed pretty hard to leave it as the exposed concrete but both ends of the catwalk are showroom spaces. The client request we use solely carpet in showroom spaces so it would have been odd if both ends of the catwalk were carpet and the catwalk itself was exposed concrete. It wasn't my first choice but I am still pleased with the results.
ha! I'd like to see some kid try to climb the cable rails that parallel the stair. They look kinda slippery. Likely he would fall down the stairs rather than over the top rail. That would show 'im.
It's good to know that there are jurisdictional requirements that might override IBC in this instance.
Looks fantastic, Steven, and the guardrail stays nicely uncluttered while meeting the no-ladder rule (do you have to add a handrail on the stair portion?).
Nice to see the butterfly expressed in the ceiling planes inside, too.
actually the whole stair tower deal worked out much better than expected - the drawings of that area (well, the structural engineers drawings of that area) were....more suggestive than specific?
what i like most about this project is the planning aspect to it that noone will probably ever notice. when i started on this job, it was already sort of underway, limping along, but the site planning followed the normal school planning model: object out in the field.
i felt that it was really impt to group the buildings more tightly together and leave a larger part of the greenfield site undisturbed, simultaneously making something of the space between the buildings. that courtyard space will be a sort of outdoor classroom/office lunch area shared by the school and the school board's central office building.
nope. LB, surprisingly, I've never cooked in any of my kitchens. most of them aren't local to me anyways...this one is in the southeast, and i'm in the SF bay area.
we do, however, get lots of feedback from the chefs who do cook there.
Thanks for posting, techno. That first pic looks like the facade is making a frowny face while observing the wreckage before it! (My problem is once I see a face in a facade, I can't stop seeing it. now I feel sad for the poor building!)
next to the adjacent buildings it doesnt look so garish. I did the sketch designs a bum-wad of a consultant did the rest, its fucked up but hey the hospital gets a therapy unit
Jobsite Pic of The Day
steven, i like the school, the black looks great by itself...quick question, why did the masons not use jamb block at the m.o.'s? is it typical to install windows prior to finishing the brick veneer? i would think that it would make for tough finishing where brick and window meets, and that the mortar can be corrosive on the aluminum??
if by jamb block you mean bullnose, the block is bullnose at the interior corners but not the outside corners.
the windows themselves don't touch the cmu, held off by blocking, so mortar's corrosiveness at the windows shouldn't be an issue. (at the top, where mortar is likely to fall into the void, the flashing would catch it before it got onto the window itself. ....and they're supposed to clean out that fallen mortar off the flashing so that it's unencumbered: we'll see if it happens.)
it is common around here for the windows to go in before the masonry and it doesn't have any specific sequencing liabilities from what i can tell. allows for us to inspect all the flashing conditions and anchorage condition before the brick goes into place. the brick leaves a 1/4" - 3/8" reveal around the window perimeter which gets backer rod and caulk so that things can move independently as they need to.
the block i am referring to replaces the need for the blocking around the m.o.

haven't used that jamb block before but some reasons i might not are:
-i usu want to show the full dimension of the window frame both inside and out and it looks like that block would conceal it?
-the blocking mounted to the outside face of the block also serves to provide a 'stop' for the rigid insulation that will be attached to the wall, and a smooth place to -lay the window head flashing so that it avoids puncture.
-wouldn't you still use blocking, but just install it in that offset?
-what would the head block look like? if it's the same shape as the jamb block, what does that do to a bond beam design? if not, how do you deal with blocking?
-school construction has to be as economical as possible. that means using as few special shapes as possible. the fewer total shape-types the better.
these are just my initial thoughts, being unfamiliar with the jamb block type. i'll look into it further though, for sure. thanks for the heads up.
the portion of the block that is different provides the stop for the rigid insulation, that is the "tab" that sticks into the cavity. so your brick returns to masonry and not the blocking.
kill the block!
the block never hurt anyone - well except those it fell on.
Sniff sniff saturday night and I'm home alone (cue hands on face and scream!)
we started demolition on another one of my projects this week... the scope of work includes demo of two affordable housing buildings from the 1950s and the construction of 4 new affordable housing buildings...






<smartass comment>
Wouldn't the housing be more 'affordable' if it didn't have to be rebuilt every 50 years?
<end smartass comment>
Can't wait to see more, architphil.
and here's some new pictures of the recreation center...




the steel structure for the lobby...
a mockup of the zinc shingles that will cover the 2nd story volumes...
a balcony/walkway overlooking the 2 story lobby space...
metal framing on the 2nd floor and an opening overlooking the green space and two large oak trees...
hmm... not sure what happened with that last picture... here it is...

LB, you're absolutely right!!! those old buildings are awful... the new ones are going to be built to last... they'll have metal roofing, integrally colored block, pre-finished hardiplank, hollow core floor structure for the second floor, etc... the design is a sorta florida cracker style vernacular... i couldn't sell the housing department on a modern design... but they'll be nice for what they are...
and i'll add my usual full disclosure statement... i am not the design architect... i'm a capital improvements project manager for the city... the architect on this project (and the recreation center) is wannemacher russell architects
Ha! At my old firm we did a historic renovation on a church in Florida, its style was described by its congregants as "Cracker Gothic" which I always thought was hysterical - I guess "Cracker" is a recognized term for a vernacular style down there!
careful of pre-finished hardie plank....cause you can't blind nail it, and all the joints need to be caulked...and most important the silica....from the sawing...is NASTY...NASTY.. You will also notice an
unreal amount of chattering...when ever a cut is made....I would call
this material our next big mistake.
^^^and for all the reasons snooker mentioned above - cutting, caulking, toxicity, nail holes, etc - it's godawful expensive to get installed (at least by someone who knows what they're doing).
thanks snooker and steven... we have a fantastic contractor so i don't think that it will be an issue... but i'll keep a lookout for issues... although it is a bit more expensive up front it should save the city money in the long run since it won't have to be repainted every 5-10 years...
Was out driving around and stopped in to see how my social worker client was coming along with the neighborhood infill garage I designed for him. As you can see it is really his play house.


and
me welding a float for the Rose Bowl Parade...sort of a job site, I suppose
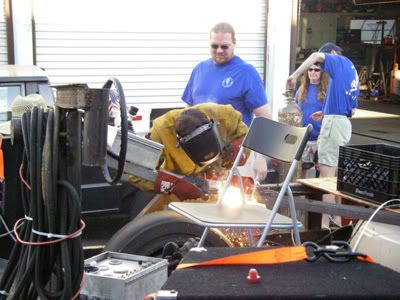
most recent pics of my Beverly Hills house...huge wood trellis...master bedroom (with steel moment frame)...pool room which cantileveres over the pool (concrete floor slab will have a sheet of water that will fall into the pool)...notice how the contractor completely fucked up the concrete
cool snooker - its quite an oddity, yet remarkable.
oops...sorry about the size ;/
This is a follow-up to my May 16, 2007 post. I just created a punch list last week and we are getting some odds and ends cleared up. This was a great project to work on and a great learning experience. The client's budget was pretty small and becamse signficantly smaller once we had to make the building structural sound. It's amazing what one will uncover when you begin to remove 50 year old walls.






Here are some pics:
Standing on the mezzanine. (Please note the painted door on the far left wall. Sad face) We originally inteded for the high wall on the right to be OSB board; we changed the wall to be covered in sheet metal.
Mezzanine handrail detail
This is the library space. We kept the floor joists in place from the former floor that we removed above.
Conference room (Please note column pop outs on the far right wall)
Conference room column detail. We had some interesting old columns we discovered when we removed the existing walls. The client didn't have enough money to shore the floor above and place larger beams so we were stuck with these bad boys. We decided to enshrine them in glass
Catwalk in the double volume team spaces
very nice n_
gracias, cris.
Nice job, n_! I love the mezzanine guardrail, what is the flooring there? And while the painted over door sucks, it still all looks quirky and cool.
looks great, no ladder effect rule in tennessee?
Uh-oh...I did the code research for this project. What's this I hear about a ladder rule? It doesn't ring a bell. Please educate me. Anyway, it passed codes for the building permit and we received the occupancy permit after the final codes walk-through three weeks ago. Was this something that they overlooked as well? We are under IBC 2006.
Vado, I'm working on your CD right now. This very second.
Liberty, it's Shaw carpet. Nice color, great texture. We pushed pretty hard to leave it as the exposed concrete but both ends of the catwalk are showroom spaces. The client request we use solely carpet in showroom spaces so it would have been odd if both ends of the catwalk were carpet and the catwalk itself was exposed concrete. It wasn't my first choice but I am still pleased with the results.
its not in the ibc but shows up in certain states code books. like kentucky where i have gotten lucky.
Our local amendments are ladder-free. Phew.
ha! I'd like to see some kid try to climb the cable rails that parallel the stair. They look kinda slippery. Likely he would fall down the stairs rather than over the top rail. That would show 'im.
It's good to know that there are jurisdictional requirements that might override IBC in this instance.
last week:


today:
and the classic kentucky no-ladder-effect guardrail detail:

that is a fine looking building SW!
thanks, vado. i'm beginning to think it might be, too.
Looks fantastic, Steven, and the guardrail stays nicely uncluttered while meeting the no-ladder rule (do you have to add a handrail on the stair portion?).
Nice to see the butterfly expressed in the ceiling planes inside, too.
yep handrails just not up yet.
actually the whole stair tower deal worked out much better than expected - the drawings of that area (well, the structural engineers drawings of that area) were....more suggestive than specific?
what i like most about this project is the planning aspect to it that noone will probably ever notice. when i started on this job, it was already sort of underway, limping along, but the site planning followed the normal school planning model: object out in the field.
i felt that it was really impt to group the buildings more tightly together and leave a larger part of the greenfield site undisturbed, simultaneously making something of the space between the buildings. that courtyard space will be a sort of outdoor classroom/office lunch area shared by the school and the school board's central office building.
first time poster on this thread:



they may not be architecture, but they're still a jobsite. (well, not anymore they're not...they've opened recently...)
and
and
that's some really nice looking kitchen equipment
thanks..we do alright for ourselves! this job had one of the best S/S Fabricators in the country working on it too, so our stuff was in good hands.
Gorgeous indeed, mightylittle. Do you get to sneak in at night and bake your award-winning delicacies there?!?
nope. LB, surprisingly, I've never cooked in any of my kitchens. most of them aren't local to me anyways...this one is in the southeast, and i'm in the SF bay area.
we do, however, get lots of feedback from the chefs who do cook there.
the new therapy unit under construction



approach
the entry <- discussion had about the colour...composition too close to the adjacent building (yes we have more like that)
Thanks for posting, techno. That first pic looks like the facade is making a frowny face while observing the wreckage before it! (My problem is once I see a face in a facade, I can't stop seeing it. now I feel sad for the poor building!)
next to the adjacent buildings it doesnt look so garish. I did the sketch designs a bum-wad of a consultant did the rest, its fucked up but hey the hospital gets a therapy unit
go therapy......dos for dummies....= does for dummies....
we all NEED some therapy now and then. or at least a spa day!
spa day sounds good
Block this user
Are you sure you want to block this user and hide all related comments throughout the site?
Archinect
This is your first comment on Archinect. Your comment will be visible once approved.