I am about do what many in the building science world consider a big no-no: insulating the exterior walls of a previous uninsulated, 100 year old home.
The cladding is original cedar clapboard. Sheathing is 1” thick t&g. The interior plaster and lath has been removed due to significant cracking throughout the house. The plaster will be replaced with drywall. Now that the interior of the walls have been striped, the studs and backside of the sheathing are exposed, allowing me to inspect for any signs of water intrusion. There are almost no signs of water coming from the exterior in. No staining, no current moisture. Where there were any gaps/cracks (found exclusively around windows), I have sealed the areas with spray foam.
I am only minorly concerned with potential issues related to water entry from the exterior not being able to dry out once insulation has been added to the cavities. However, due to the inevitability of imperfection, and the simple fact the home does now have an exterior weather barrier/house wrap, I’ve elected to fill the stud cavities with moisture resistant mineral wool batts.
What I’m mostly battling with now is the decision to use a vapor barrier on the interior, just behind the new drywall. Despite the likelihood of vapor permeating through the drywall, into the cavity, and condensing on the backside of the sheathing, I am still hesitant to add a control layer which discourages drying to the interior. My gut says to keep it simple, don’t try to overly seal a building which is not designed to be sealed tight. My brain tells me to use a semi-permeable membrane such as Certain-Teed’s Menbrain product. The reconciliation between my gut and brain tells me to use a vapor-retarding primer on the drywall. Now I’m curious what each of you would tell me.
It should be noted that a small number of the exterior walls were previously insulated with fiberglass batts. In these areas, drywall had been installed over the batts. Apparently one of previous owners did a bit of remodeling. Judging by the branding on the fiberglass batts, the insulation was installed roughly 40 years ago. There was absolutely no moisture damage behind those batts, the studs and sheathing bone dry. I could have simply left the fiberglass batts installed, but I was curious to inspect for damage and see what the internet has been yammering about in terms killing old houses by installing insulation within stud cavities. Anecdotal, for certain, but no issues in this case. Those fiberglass batts will be replaced with R-15 unfaced mineral wool batts, which I intend to use throughout the house.
So, lets hear it. Any suggestions or tips? I’m mostly curious to hear opinions regarding vapor control. As good ol’ Mr. Lstiburek points out, even an unpainted sheet of drywall (no holes, of course) will diffuse only 1/3 quart of water per heating season. Add some latex paint to that, you’re vapor permeability is negligible. Perhaps even vapor-retarding primer is overkill and I’ll have better luck keeping it simple.
Let me know what you think.
Note: I am in climate zone 5. We heat the house with forced hot air.
I'd say no vapor barrier - not unless you are putting a steam room in somewhere. Sealing the wall from the interior seems counterproductive with the exterior wall you describe
I wouldn't. I might rethink that foam, too, unless it's vapor permeable. That wall has obviously benefitted from being able to dry to the inside or out for the last 100 years - it it ain't broke, don't fix it.
Fill it with unfaced mineral wool and use regular gyp bd & latex paint on the interior.
Note that most current building codes (check your local code requirements) generally require a Class I or II vapor retarder on the interior of the wall assembly for Climate Zone 5, unless you have vented cladding or continuous insulation. If you do have vented cladding or continuous insulation, then you can use a Class III vapor retarder (i.e. latex paint). Wood siding is sort of vented but Lstiburek also points out that it "need[s] help" to be considered ventilated. https://www.jlconline.com/how-...
"My gut says to keep it simple, don’t try to overly seal a building which is not designed to be sealed tight." It also sounds like you've already added a weather barrier ("the home does now have an exterior weather barrier/house wrap"). If you did, you've already sealed the house up. This is reducing the ability for it to dry with air movement. You're also adding insulation which is reducing the ability for it to dry with thermal movement. Best to design the assembly accordingly and control for vapor.
You didn't mention if the fiberglass you found from previous remodels was faced or unfaced (sounds like it might have been faced if there was branding that you could read). Kraft facer on the batts would be a Class II vapor retarder (so would the CertainTeed MemBrain product).
"My brain tells me to use a semi-permeable membrane such as Certain-Teed’s Menbrain [sic] product." Listen to your brain. It sounds like it more closely matches code requirements than your gut.
I'd definitely use a variable permeance membrane on the interior--it costs a few bucks but is made for just this kind of situation. Certainteed Membrain is ok but it's very flimsy and more vapor-open than I prefer. I spec and use Siga Majrex or Pro Clima Intello. I want to try Rothoblaas' version as well.
use a wood fibre insulation and wood fibre plastering board - they are fully vapor permeable so will always dry and regulate. use a chalk plaster and chalk based paints inside and you'll have extra protection against mold.
but use pro clima intello if you're gonna keep the buildup youre mentioning above...
This is the correct answer. Better even is to not even insulate the exterior and just use a low-cost/ low-energy radiant geothermal system. My 120 year old masonry house is meant to breathe. I use felt weatherstripping, mineral wool insulation around frames and under floors, and true plaster on lathe. The radiators are so hilariously oversized you could keep it at 70+ degrees with the windows open in the winter.
Geothermal heating is not low cost to install and rather site specific for it's feasibility.
Also - with a mineral fiber cavity insulation and the right vapor retarder wouldn't you'll still have vapor permeable wall assembly that can handle wetting without causing mold problems?
Your 120 year old house is meant to "breathe" (i.e., allow water vapor to pass through) but it's not meant to be kept at 70°F and 50% humidity all winter or to have air conditioning keep it cool and dry in the summer. Modern living is detrimental to most old homes. One approach is to not insulate, and use excessive amounts of fossil fuels to force-dry the walls in winter. Another is to use modern building science products made for the situation.
@ Chad - sure, but every layer is just more space for water vapor to hang out, even with vapor-permeable products. I think the link WG posted below is a pretty decent summary on it.
Modern living is detrimental to most old homes. One approach is to not insulate, and use excessive amounts of fossil fuels to force-dry the walls in winter. Another is to use modern building science products made for the situation.
We had Christine Williamson (aka Building Science Fight Club) and Doug Horgan on The BS + Beer Show to talk about vapor retarders--you might find it helpful:
what did you decide to do? And how did it turn out? I guess only time will tell. I’m also in the same situation and have decided on Rockwool but leaning toward omitting the interior plastic vapor barrier since the rest of the home does not have a vapor barrier. Thx
100+ year old buildings were built so they evaporate the moisture and not trap it. This is why they can be particularly drafty. If you hyperwrap a building, you need to make sure the details are so well done that moisture never ever even in 100 or even 1,000 years gets inside the walls. This means that you need to waterproof with 0% permeable interior in any room with sinks, toilets, and bath/showers and proper ventilation. So, then you are building something almost like you would a spacecraft. You need to have the building breath and ventilate for various HSW reasons but certainly to allow moisture to leave because if it's trapped in, you will have a lot of problems. Note: latex paint, while it will resist moisture for a while, it's not a vapor barrier ever time and while it might be effective initially, it ultimately gets holes and becomes permeable.
Buildings that are wrapped as tight as they are on the exterior causes a problem because they don't apply the same degree of vapor/moisture barrier, also on the interior side so moisture essentially condensates inside the wall cavities. You then got mold and mold contributes to wood rot and almost every wood rot had some mold issues preceding it rotting.
Ultimately, this is why many of these structures are rotting out after they been housewrapped and then it rots after a few decades. They get hyperfocused on the keeping moisture out from the outside they totally forget the moisture that is getting in from use of sinks, toilets, doors and windows opening & closing, bath tubs/showers, and lets not forget, the occupants themselves. Now you have moisture vapor from all these sources on the inside of the house. So the moisture permeates the interior wall finishes and then gets stuck inside the walls because of the impermeable layer on the exterior side of the wall.
Houston, we have a problem. We didn't take into account the humans taking a piss, exhaling moisture in their breath, having showers/bath, using the sinks, etc.
I have a very similar scenario except it’s an 80 year old detached garage in Southern California. In my case it’s a stucco exterior with felt or tar paper and no sheathing. The walls are standard 2 x 4 with diagonal racking support and on the interior of the walls they put 7/16 OSB which is great for a garage.
However as the heat has started to rise in Southern California I’ve looked into my walls and I’m not sure how best to truly insulate on a budget.
Would love to get some feedback on this and to understand how the author proceeded with his build out. As I am currently divided on whether to try and install rigid foam in 2 inches or more, or go with Rock wool and attempt an interior smart vapor retarder under the interior OSB.
Per the fantastic videos that others have provided here I think keeping the garage breathable with some amount of insulation in the walls that is hydrophobic seems the best option of a bad situation. Not to mention I haven’t even thought about the roofing yet but that’s for another post.
Any feedback on these ideas would be greatly appreciated particularly by the author. Thanks and I really appreciate this great article.
Aug 14, 22 8:44 pm ·
·
Block this user
Are you sure you want to block this user and hide all related comments throughout the site?
Archinect
This is your first comment on Archinect. Your comment will be visible once approved.
Vapor barrier on 100 year old home?
Hi, Folks.
I’d like to get your opinion on something.
I am about do what many in the building science world consider a big no-no: insulating the exterior walls of a previous uninsulated, 100 year old home.
The cladding is original cedar clapboard. Sheathing is 1” thick t&g. The interior plaster and lath has been removed due to significant cracking throughout the house. The plaster will be replaced with drywall. Now that the interior of the walls have been striped, the studs and backside of the sheathing are exposed, allowing me to inspect for any signs of water intrusion. There are almost no signs of water coming from the exterior in. No staining, no current moisture. Where there were any gaps/cracks (found exclusively around windows), I have sealed the areas with spray foam.
I am only minorly concerned with potential issues related to water entry from the exterior not being able to dry out once insulation has been added to the cavities. However, due to the inevitability of imperfection, and the simple fact the home does now have an exterior weather barrier/house wrap, I’ve elected to fill the stud cavities with moisture resistant mineral wool batts.
What I’m mostly battling with now is the decision to use a vapor barrier on the interior, just behind the new drywall. Despite the likelihood of vapor permeating through the drywall, into the cavity, and condensing on the backside of the sheathing, I am still hesitant to add a control layer which discourages drying to the interior. My gut says to keep it simple, don’t try to overly seal a building which is not designed to be sealed tight. My brain tells me to use a semi-permeable membrane such as Certain-Teed’s Menbrain product. The reconciliation between my gut and brain tells me to use a vapor-retarding primer on the drywall. Now I’m curious what each of you would tell me.
It should be noted that a small number of the exterior walls were previously insulated with fiberglass batts. In these areas, drywall had been installed over the batts. Apparently one of previous owners did a bit of remodeling. Judging by the branding on the fiberglass batts, the insulation was installed roughly 40 years ago. There was absolutely no moisture damage behind those batts, the studs and sheathing bone dry. I could have simply left the fiberglass batts installed, but I was curious to inspect for damage and see what the internet has been yammering about in terms killing old houses by installing insulation within stud cavities. Anecdotal, for certain, but no issues in this case. Those fiberglass batts will be replaced with R-15 unfaced mineral wool batts, which I intend to use throughout the house.
So, lets hear it. Any suggestions or tips? I’m mostly curious to hear opinions regarding vapor control. As good ol’ Mr. Lstiburek points out, even an unpainted sheet of drywall (no holes, of course) will diffuse only 1/3 quart of water per heating season. Add some latex paint to that, you’re vapor permeability is negligible. Perhaps even vapor-retarding primer is overkill and I’ll have better luck keeping it simple.
Let me know what you think.
Note: I am in climate zone 5. We heat the house with forced hot air.
I'd say no vapor barrier - not unless you are putting a steam room in somewhere. Sealing the wall from the interior seems counterproductive with the exterior wall you describe
just painted gyp for vapor retarder
I'd still install a vapor retarder behind the GWB and forgo the special primer.
I wouldn't. I might rethink that foam, too, unless it's vapor permeable. That wall has obviously benefitted from being able to dry to the inside or out for the last 100 years - it it ain't broke, don't fix it.
Fill it with unfaced mineral wool and use regular gyp bd & latex paint on the interior.
you could do Kraft face Batts if you're up north. Don't do sheet plastic like visqueen unless you're north of the frozen Canadian tundra.
can't be canadian, the op wrote vapour wrong.
Note that most current building codes (check your local code requirements) generally require a Class I or II vapor retarder on the interior of the wall assembly for Climate Zone 5, unless you have vented cladding or continuous insulation. If you do have vented cladding or continuous insulation, then you can use a Class III vapor retarder (i.e. latex paint). Wood siding is sort of vented but Lstiburek also points out that it "need[s] help" to be considered ventilated. https://www.jlconline.com/how-...
"My gut says to keep it simple, don’t try to overly seal a building which is not designed to be sealed tight." It also sounds like you've already added a weather barrier ("the home does now have an exterior weather barrier/house wrap"). If you did, you've already sealed the house up. This is reducing the ability for it to dry with air movement. You're also adding insulation which is reducing the ability for it to dry with thermal movement. Best to design the assembly accordingly and control for vapor.
You didn't mention if the fiberglass you found from previous remodels was faced or unfaced (sounds like it might have been faced if there was branding that you could read). Kraft facer on the batts would be a Class II vapor retarder (so would the CertainTeed MemBrain product).
"My brain tells me to use a semi-permeable membrane such as Certain-Teed’s Menbrain [sic] product." Listen to your brain. It sounds like it more closely matches code requirements than your gut.
I'd definitely use a variable permeance membrane on the interior--it costs a few bucks but is made for just this kind of situation. Certainteed Membrain is ok but it's very flimsy and more vapor-open than I prefer. I spec and use Siga Majrex or Pro Clima Intello. I want to try Rothoblaas' version as well.
This is my pinned tweet. I have no advice for you.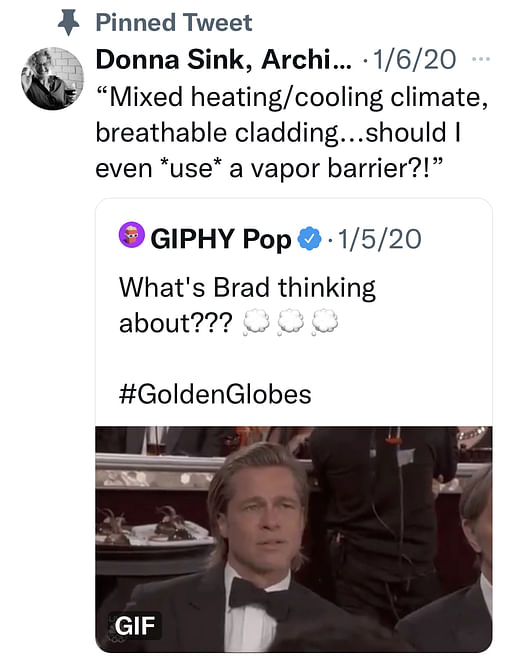
use a wood fibre insulation and wood fibre plastering board - they are fully vapor permeable so will always dry and regulate. use a chalk plaster and chalk based paints inside and you'll have extra protection against mold.
but use pro clima intello if you're gonna keep the buildup youre mentioning above...
This is the correct answer. Better even is to not even insulate the exterior and just use a low-cost/ low-energy radiant geothermal system. My 120 year old masonry house is meant to breathe. I use felt weatherstripping, mineral wool insulation around frames and under floors, and true plaster on lathe. The radiators are so hilariously oversized you could keep it at 70+ degrees with the windows open in the winter.
Geothermal heating is not low cost to install and rather site specific for it's feasibility.
Also - with a mineral fiber cavity insulation and the right vapor retarder wouldn't you'll still have vapor permeable wall assembly that can handle wetting without causing mold problems?
Your 120 year old house is meant to "breathe" (i.e., allow water vapor to pass through) but it's not meant to be kept at 70°F and 50% humidity all winter or to have air conditioning keep it cool and dry in the summer. Modern living is detrimental to most old homes. One approach is to not insulate, and use excessive amounts of fossil fuels to force-dry the walls in winter. Another is to use modern building science products made for the situation.
@ Chad - sure, but every layer is just more space for water vapor to hang out, even with vapor-permeable products. I think the link WG posted below is a pretty decent summary on it.
Louder for the people in the back Wood Guy:
Modern living is detrimental to most old homes. One approach is to not insulate, and use excessive amounts of fossil fuels to force-dry the walls in winter. Another is to use modern building science products made for the situation.
all good comments, thx all
[is this our designated professional discussion for the month? we get HSW's for this, right?]
Archinect should become a registered provider and send out certificates to participants.
We had Christine Williamson (aka Building Science Fight Club) and Doug Horgan on The BS + Beer Show to talk about vapor retarders--you might find it helpful:
good discussion
what did you decide to do? And how did it turn out? I guess only time will tell. I’m also in the same situation and have decided on Rockwool but leaning toward omitting the interior plastic vapor barrier since the rest of the home does not have a vapor barrier. Thx
I'm just here to chuckle at the Menbrain slip of the OP.
100+ year old buildings were built so they evaporate the moisture and not trap it. This is why they can be particularly drafty. If you hyperwrap a building, you need to make sure the details are so well done that moisture never ever even in 100 or even 1,000 years gets inside the walls. This means that you need to waterproof with 0% permeable interior in any room with sinks, toilets, and bath/showers and proper ventilation. So, then you are building something almost like you would a spacecraft. You need to have the building breath and ventilate for various HSW reasons but certainly to allow moisture to leave because if it's trapped in, you will have a lot of problems. Note: latex paint, while it will resist moisture for a while, it's not a vapor barrier ever time and while it might be effective initially, it ultimately gets holes and becomes permeable.
Buildings that are wrapped as tight as they are on the exterior causes a problem because they don't apply the same degree of vapor/moisture barrier, also on the interior side so moisture essentially condensates inside the wall cavities. You then got mold and mold contributes to wood rot and almost every wood rot had some mold issues preceding it rotting.
Ultimately, this is why many of these structures are rotting out after they been housewrapped and then it rots after a few decades. They get hyperfocused on the keeping moisture out from the outside they totally forget the moisture that is getting in from use of sinks, toilets, doors and windows opening & closing, bath tubs/showers, and lets not forget, the occupants themselves. Now you have moisture vapor from all these sources on the inside of the house. So the moisture permeates the interior wall finishes and then gets stuck inside the walls because of the impermeable layer on the exterior side of the wall.
Houston, we have a problem. We didn't take into account the humans taking a piss, exhaling moisture in their breath, having showers/bath, using the sinks, etc.
I have a very similar scenario except it’s an 80 year old detached garage in Southern California. In my case it’s a stucco exterior with felt or tar paper and no sheathing. The walls are standard 2 x 4 with diagonal racking support and on the interior of the walls they put 7/16 OSB which is great for a garage.
However as the heat has started to rise in Southern California I’ve looked into my walls and I’m not sure how best to truly insulate on a budget.
Would love to get some feedback on this and to understand how the author proceeded with his build out. As I am currently divided on whether to try and install rigid foam in 2 inches or more, or go with Rock wool and attempt an interior smart vapor retarder under the interior OSB.
Per the fantastic videos that others have provided here I think keeping the garage breathable with some amount of insulation in the walls that is hydrophobic seems the best option of a bad situation. Not to mention I haven’t even thought about the roofing yet but that’s for another post.
Any feedback on these ideas would be greatly appreciated particularly by the author. Thanks and I really appreciate this great article.
Block this user
Are you sure you want to block this user and hide all related comments throughout the site?
Archinect
This is your first comment on Archinect. Your comment will be visible once approved.