A pedestrian bridge at FIU university (near Miami) across US 1 just collapsed killing at least six people trapped in cars underneath stopped at a red light. The bridge was just opened Saturday.
Just opened or just installed? There's orange construction fences on the edges of the pedestrian deck, don't think it would be opened if that were the case.
You are correct. Auto traffic was allowed underneath the bridge (that traffic was the source of the injuries and fatalities) but it was not open to pedestrians as yet.
A quick search show a great deal of litigation between Munilla Management and various parties.
Mar 15, 18 5:21 pm ·
·
SneakyPete
Clients need to do their homework just as much as design firms do.
Mar 15, 18 5:28 pm ·
·
JLC-1
world class winners....
Mar 15, 18 5:29 pm ·
·
gwharton
Low bidder. You get what you pay for.
Mar 15, 18 5:29 pm ·
·
SneakyPete
Honest question: when does prior litigation and negligence (in general, not as it may pertain to this tragedy) result in a bid that can be rejected?
Mar 15, 18 5:30 pm ·
·
Almosthip7
Then when an engineering firm gets a a bad reputation they just buy up a firm and rebrand.
Genivar and WSP come to mind..... and SNC-Lavalin
Mar 15, 18 6:26 pm ·
·
joseffischer
For GA schools, the no bid list is really easy to get on. You don't really need a reason beyond "we don't like that firm." On the flip side, the schools (and architects) get into a lot of trouble if their bidding process doesn't pull at least 3 legitimate bids. We usually get 5-7, so no worries there.
What a horrible tragedy. I initially thought this was the result of negligent construction methods, but I noticed something while reading the NPR article:
Those holes in the section look like post-tensioning ducts to me. This Engineering News Record article confirms that the deck was to be post-tensioned:
My gut tells me that someone, whether the engineer or builder, didn't calculate the bending stress at midspan correctly prior to application of tension, the section cracked and a hinge formed, and because the ends were simply resting on their pedestals and not fixed, the whole thing turned into a mechanism and failed.
Of course, this is just my best guess. I'm eager the see the result of the investigation and learn the real reason for the failure.
maybe the problem was allowing this "test" or "experiment" to occur over an open public roadway. I hope the engineering firm is put out of business for allowing this huge oversight in safety.
Florida International University Pedestrian Bridge Collapse
SUSPECTS DATABASE I have identified, named and collected photographs of many of the key players and suspects for possible arrest and criminal prosecution on charges such as involuntary manslaughter.
1. Mark B. Rosenberg, FIU President 2. Kenneth Jessell, FIU Vice President and Chief Financial Officer 3. Atorod Azizinamini - Chair of FIU’s Civil & Environmental Engineering Department and director of FIU’s Accelerated Bridge Construction University Transportation Center
Project contractor organisation chart.
Project contractor company presidents 4. Linda Figg, FIGG President 5. Jorge Munilla, MCM President
National Society of Professional Engineers 9. W. Denny Pate, FIGG, Lead Technical Designer and Engineer of Record 10. Robert Murphy, MCM, Project Director * Dwight Dempsey, FIGG, Project Design Manager 11. Kenneth Heil, FIGG, Design Quality Manager 12. Manuel Feliciano, FIGG, Bridge Engineer 13. Kristian Navarro, MCM, Project Engineer
US Army Corps of Engineers * Eddie Martinez, MCM, Project Safety Manager * Kristian Navarro, MCM, Project Engineer 14. Carlos Hernandez, MCM, Quality Control Manager
Elected Representatives of the People 15. Mario Diaz-Balart, U.S. Representative and Chairman of the House Appropriations Subcommittee on Transportation, Housing and Urban Development. 16. Orlando Lopez, Mayor of the City of Sweetwater
17. Anthony Foxx, Obama's Transport Secretary * Atorod Azizinamini - Chair of FIU’s Civil & Environmental Engineering Department and director of FIU’s Accelerated Bridge Construction University Transportation Center
State and Federal Authorities 18. Rick Scott, Governor of Florida 19. Donald Trump, President of the United States
My (non-engineer) hunch has to do with post tensioning the bottom platform after the truss structure was secured...Is that common practice? Seems counterintuitive...
Mar 26, 18 1:36 pm ·
·
x-jla
I’m sure that the connection isn’t ridgid, but still seems like somethings off about that...I mean the point loads on that cord seem like a lot for such a thin slab...that hasn’t been fully strengthened?
As I understand the construction the unfinished tower and the 'cable stays' were for show. In fact, there were no cables to be installed, just some pipe to give the appearance of a cable-stayed bridge. They apparently were trying to mimic some of Calatrava's designs without the super-expensive engineering and construction costs.
Mar 24, 18 3:09 pm ·
·
Wilma Buttfit
Interesting. Something about it in the renderings does look fake.
Mar 24, 18 3:19 pm ·
·
Wilma Buttfit
having the structure only for show is a bad way to design a bridge
This thread was used as an example of bad internet activity at an insurance company continuing ed seminar that I attended last week. The insurance company's attorney said that a professional who engages in online speculation about this type of event, using their real name and/or any identifying info about themselves or their firm, is leaving a trail that can be used against them in future cases. For instance if you put forth a theory for why this bridge collapsed, and it turns out that your theory is not 100% correct, that can be used as evidence of your lack of technical knowledge/ability and/or poor professional judgement.
This is EXACTLY what the internet should be doing. Looking at the issues raised on the "Eng-Tips" website (search 'Florida bridge') would make any architect or engineer pause and reflect on their next project. The structural engineers commenting there are making intelligent comments and raising questions about both the materials, the design, and the construction of the bridge without pointing fingers at specific individuals.
The key is to be anonymous, I guess. Neither the insurance companies or their lawyers want any of the information to ever get out or be the subject of professional conversations.
Mar 26, 18 12:46 pm ·
·
Flatfish
Yes, be anonymous if you want to discuss that on the internet - that was the takeaway.
It isn't that they don't want information to get out - it's that they don't want it to get out, right or wrong, with the names of their insured professionals attached to it. It's that it can be used to establish what you should have known, or could have been expected to know, or as evidence of what you don't know, in some future case.
Oh cool, insurers read archinect. If they want to reduce risks in the industry, they should start with all the unlicensed and never-practiced-before professors that dominate the schools. Structures do need more than theory to stand up. Especially now that you can get licensed right out of school.
Thanks to the use of an online truss calculator, I have now been able to make a more accurate calculation of the likely forces which the bridge was subjected to when it failed.
Video evidence shows that the bottom northern end joint of the bridge failed first and so suspicion has fallen upon the elements of the bridge at the north end and so it was helpful to calculate the likely axial forces along member #11 (marked "M11" in the diagrams above).
The compression force from the dead weight of the bridge I calculated as - 1367 kip or 1,367 thousand pounds of force.
The compression force from the post-tensioning (P.T.) bars within member #11 - I calculated had to be at least 304 kip but in practice would have been more, perhaps significantly more so we should have treated the P.T. bar force as a live load (LL), not a dead load (DL) for design purposes.
So the unfactored load on member #11 was at least 1367 + 304 = 1671 kip.
As recommended,
factoring the load as 1.2 x DL + 1.6 x LL suggests they should have designed for a Maximum allowable design factored load of 1367 x 1.2 + 304 x 1.6 = 2127 kip
that member #11 used 10 x #7 bars which would suggest it was suitable for a factored load of only 2006 kip. which corresponds to a ratio of factored to unfactored load of 2006/1671 = 1.2 (only).
To get to a factored load of at least 2127 kip, as my table suggests, member #11 would have needed 14 x #8 or 12 x #9 or 10 x #10 rebars.
Even if member #11 was not designed or constructed within code we cannot conclude that the failure of the bridge's bottom northern end joint was caused by a failure of member #11 per se.
The remains of the bottom northern end joint of the bridge
The failure which the evidence of the video and photographs suggests is more likely to be with the design of the joint itself, an insufficiency of reinforcement in anchoring member #11 to the deck, leading to, I might suggest, shear fractures along the 2 planes either side of member #11 where they intersect with the deck which I have illustrated by annotating sheet B-8 from the design engineer's drawings as follows.
I may not know with 100% certainty what the cause of this bridge collapse is but I can offer my expert opinion on the basis of the available evidence so far.
What caused it to fail? The bridge designers innovated (incompetently) a new I-beam design of bridge but where the I-beam's upright-supports (called an "open truss") join the deck of the bridge, the designers should have specified the necessary reinforcement to stop the severely stressed joints breaking apart - "should have" but negligently didn't and so the weakest link - the northern bottom end joint - failed first and it caused a catastrophic collapse of the whole bridge.
How hard can it be? Here's my concept for a high shear strength steel joint for this sort of application.
Here's a closer look at my computer aided design images for the joint
So my concept is to use an steel I-beam to make something like a clevis joint.
The link is designed accept a cable connector.
I don't agree that architects or engineers should ever use rebar-and-stirrup "cage" concrete columns for a bridge truss, like FIGG have, I think, mistakenly designed for the collapsed FIU pedestrian bridge.
Instead, I'd recommend metal-only for a bridge truss's structural elements.
The obvious way to go to complete a revised design of truss member #11 (M11) starting from my joint design would be to use H / I steel beam for the full length of M11 and for all truss members which are in compression.
For a design which specifies a concrete surface for the truss members then a superficial, non-structural concrete facade could be added around the truss members easily enough.
Thank you for that, I needed a good laugh this morning.
The most obvious problem with your "design" is that if you change all the bridge members to steel then you don't need the cable anymore, because it was originally for prestressing the concrete.
Another problem is that if you encase the joint in "non-structural" concrete, either the joint will become rigid and won't behave the way you expect, or the joint will rotate and the concrete will immediately crack and delaminate.
It's obvious you have no idea what you're doing. I'm sure that won't stop you, though. Try posting that nonsense on an engineering forum and see how far it gets you.
Some of the bridge components are always in tension when the bridge is in situ, in normal operation - the deck members, D1 to D5 and the truss upright support members M5 and M8 for example.
You can see which are which are in tension and which in compression in my Force Bar Chart image, previously posted.
If you need to see that image bigger, use this link - Force Bar Chart
So when I wrote "use H / I steel beam for the full length of M11 and for all truss members which are in compression" I meant, for ONLY those truss members which are in compression but not for those members which are always in tension, for which cable is lighter.
The concrete facade would in sections, attached separately to each member, with a sealed joint between the concrete sections.
I already have posted this on an engineering forum.
You can't bluff your ignorance away by being obnoxiously sceptical. You simply come over as a troll.
Apr 6, 18 3:34 pm ·
·
Non Sequitur
So, was it the sealant between the concrete panels that caused the collapsed? Perhaps you should have specified some structural glazing silicone, then less would have died.
You are wilfully misunderstanding in order to troll my posts because you have nothing intelligent or educated to say about the matter.
There was no concrete facade in the collapsed bridge and even if there were it would have made no difference.
The problem was with the structural joints of the truss members.
The sealant between your bath and the bathroom wall is not there to stop your bath collapsing but to stop water penetrating between the gap between your bath and the wall.
"The information I posted came from following the links on your website."
But the lying troll posted a link to the scurrilous rationalwiki website, the favourite site for trolls who have nothing to contribute to a discussion and get off on personal attacks.
Trolls are the lowest of the low in internet forums and any forum should ban them,
Do you know that you can have a free profile page here on Archinect on which you can list all of the articles and videos about you that you've posted on your website? It would help expand your reputation beyond Great Britain.
Another thing, Peter - I didn't post anything from rationalwiki. But thanks for pointing me to that:
Peter Dow is a Scottish left-wing "activist", alleged scientist, an anti-monarchy campaigner and the self-proclaimed “Republican Socialist National Standard Bearer” of Scotland.[1] His bizarre one-man campaign against the British monarchy, the British state, British academia, and British sanity have led to him exposing his gibbering lunacy to various unsuspecting netgoers for some years now.
The design would most likely specify the finished piece with a view to it being made out of one of the standard sizes of I-beams which are held in stock by steel stockholders..
The construction would presumably order the finished steel pieces from a steel fabricator who would in turn order the specified size from the steel stockholder and cut it to size and cut out the middle bit at the end, to allow space for the link etc.
Analysis of the newly released FIU bridge plans has revealed that my earlier suspicion that member 11 was dangerously under-reinforced has been confirmed, to such a degree that the collapse of member 11 under the compression load after the bridge was placed on the piers but before destressing was to be expected.
The first point to note from the plans is that the plan's P.T. bar tensioning begins once the concrete reaches a strength of 6,000 psi or more, as this quote shows -
2. AFTER CONCRETE COMPRESSIVE STRENGTH HAS REACHED 6000 PSI, STRESS POST-TENSIONING OF THE MAIN SPAN IN THE FOLLOWING SEQUENCE ..."
Next, the plans recommend a P.T. bar setting for the 2 P.T. bars in member 11 which together total a P.T. bar tension of 560 KIP.
The results of my truss calculations show the dead weight of the bridge exerts a tensile force of 304 KIP while the bridge is being transported and a compressive force of 1367 KIP when the bridge is placed on the piers.
Now let us consider what all those forces together in the sequence they were applied mean for the compressive force on the reinforced concrete of member 11.
I have considered 5 different stages, A, B, C, D and E. The bridge collapsed either in stage D or as a result of damage sustained in stage D, so the bridge never got to stage E in good order, sadly, but inevitably given the plan followed.
Stage A The concrete has hardened to at least 6,000 PSI and so post tensioning is about to begin but at this stage the mainspan is still resting on the ground, so there are no troublesome forces on member 11, no PT bar tension, no bridge dead weight and so the reinforced concrete is not being compressed very much at all except under its own weight and that of the canopy immediately above it, but we will ignore that for now.
Stage B The P.T. bars of member 11 have been tensioned to the recommended amount - a total of 560 KIP and that tension force on the P.T. bars is being provided by an equal and opposite compressive force of 560 KIP on the reinforced concrete. But the mainspan is still on the ground so not much in the way of dead weight of the bridge to worry about yet.
Stage C. The mainspan has been lifted onto the transporters and now the dead weight of the bridge is exerting an external tension force of 304 KIP on member 11. This has the effect of reducing the compressive force on the reinforced concrete of member 11 by 304 KIP down to 256 KIP.
Stage D, "D" for "danger" and for "Doom". This is when things take a turn for the worse. The bridge gets placed on the piers and now the dead weight of the bridge is applying a compressive force of 1367 KIP on to member 11. So now the reinforced concrete has to take the full 560 KIP from the P.T. bars plus the 1367 KIP dead weight to suffer a whopping 1927 KIP of compressive force, which is more than the member is able to cope with, especially so if the concrete has not reached is full strength of at least 8500 PSI, as is shown in this table from my concrete column calculator and this bar chart.
The plans only call for 8 number 7 (diameter 7/8" inch, area 0.6 square inches each), axially orientated reinforcing bars, just barely 1% of a reinforcement ratio for that size of concrete member.
As I have noted there, W Denney Pate's drawings don't draw a section through member 11 with only 2 P.T. bars, only section B-B "(TYP. FOR ALL MEMBERS WITH P.T. BARS)" which draws 8 reinforcement bars. Bars marked here "7S11" are 8 size 7 (7/8" diameter) bars confirmed by the table on page 98, SHEET B-98, SUPERSTRUCTURE REINFORCEMENT BAR LIST AND NTSB images.
It's inadequate reinforcement for the compression before destressing the P.T. bars.
So it turns out that this picture was "the smoking gun" after all, but not for the reason I thought at the time, but because it shows one of the far too small and far too few reinforcement bars, marked "<-B->".
Stage E. After destressing is complete. We don't know for sure if this stage was actually reached, but even if it was, by that time the damage was done and the member 11 was failing and bridge had begun the process of collapsing and it was just a matter of time.
One small post for a scientist, one giant leap for forensic engineering.
member 2's "SECTION C-C" - - has 12 x size 8 (diameter 1", area 0.785 sq-in) reinforcing bars and member 2's P.T. bar force setting is 560 kip (same as member 11). My truss calculation results were - in transit tension of 458 kip in situ compression of 1920 kip Now let us consider what all those forces together in the sequence they were applied mean for the compression force on the reinforced concrete of member 2. At the critical "Stage D", when the bridge is placed on the piers but before the P.T. bars can be destressed, the reinforced concrete of member 2 has to take the full compression force of 560 KIP from the P.T. bars under tension plus the 1920 KIP dead weight of the bridge to suffer a total of 2480 KIP of compression force, but member 2 was able to cope with that load of 2480 kip, so I calculated the maximum allowable design factored load to find out how strong the concrete must have been, in this table from my concrete column calculator and this bar chart. Therefore the survival of member 2 may be expected, during Stage D anyway, if the strength of the concrete was 7,000 psi or more, albeit a reasonably safe load factor (at least 1.2) is not to be enjoyed until the concrete hardens to at least 8,285 psi. Simply applying commonly used engineering design equations for concrete columns suggests clearly why member 2 survived but member 11 failed. Pate's under-design of member 11 was significantly further out of code than was his design of member 2.
Apr 29, 18 7:27 pm ·
·
Non Sequitur
Love it.
Apr 29, 18 7:46 pm ·
·
Non Sequitur
Braveheart was a great scottish documentary.
Apr 29, 18 8:41 pm ·
·
x-jla
Poppycock
Apr 29, 18 10:39 pm ·
·
Block this user
Are you sure you want to block this user and hide all related comments throughout the site?
Archinect
This is your first comment on Archinect. Your comment will be visible once approved.
Pedestrian Bridge Collapse
A pedestrian bridge at FIU university (near Miami) across US 1 just collapsed killing at least six people trapped in cars underneath stopped at a red light. The bridge was just opened Saturday.
that's not it though, http://www.mcm-us.com/news/mcm...
You may be right. This is what a model of the bridge was presented as:
Just opened or just installed? There's orange construction fences on the edges of the pedestrian deck, don't think it would be opened if that were the case.
https://www.npr.org/2018/03/15...
Regardless, this is horrible.
You are correct. Auto traffic was allowed underneath the bridge (that traffic was the source of the injuries and fatalities) but it was not open to pedestrians as yet.
Construction Firms Behind Collapsed FIU Bridge Faced Accusations of Unsafe Practices
Two of the biggest firms that built the Florida International University pedestrian bridge that collapsed today have recently been accused of unsafe practices. In one of those cases, another bridge project toppled onto workers.
http://www.miaminewtimes.com/n...
Get this, Figg built the 35W bridge in Minneapolis, to replace the one that collapsed.
Figg and MCM are in for a world of trouble over this.
F
A quick search show a great deal of litigation between Munilla Management and various parties.
Clients need to do their homework just as much as design firms do.
world class winners....
Low bidder. You get what you pay for.
Honest question: when does prior litigation and negligence (in general, not as it may pertain to this tragedy) result in a bid that can be rejected?
Then when an engineering firm gets a a bad reputation they just buy up a firm and rebrand. Genivar and WSP come to mind..... and SNC-Lavalin
For GA schools, the no bid list is really easy to get on. You don't really need a reason beyond "we don't like that firm." On the flip side, the schools (and architects) get into a lot of trouble if their bidding process doesn't pull at least 3 legitimate bids. We usually get 5-7, so no worries there.
I thought this was a cable-stayed bridge design. I did not see the tower or cables in the picture, perhaps they were doing that at later!
Code of Hammurabi would apply here, if I were king.
What a horrible tragedy. I initially thought this was the result of negligent construction methods, but I noticed something while reading the NPR article:
Those holes in the section look like post-tensioning ducts to me. This Engineering News Record article confirms that the deck was to be post-tensioned:
https://www.enr.com/articles/4...
One of the vehicles crushed by the bridge was a vehicle for a post-tensioning manufacturer:
https://www.local10.com/news/florida/miami-dade/fiu-pedestrian-bridge-collapses-days-after-portion-of-bridge-was-installed-
My gut tells me that someone, whether the engineer or builder, didn't calculate the bending stress at midspan correctly prior to application of tension, the section cracked and a hinge formed, and because the ends were simply resting on their pedestals and not fixed, the whole thing turned into a mechanism and failed.
Of course, this is just my best guess. I'm eager the see the result of the investigation and learn the real reason for the failure.
They seem to be testing a variety of new things here from construction and installation techniques to concrete mix.
maybe the problem was allowing this "test" or "experiment" to occur over an open public roadway. I hope the engineering firm is put out of business for allowing this huge oversight in safety.
If the first picture isn't the bridge, can we get it removed?
Florida International University Pedestrian Bridge Collapse
SUSPECTS DATABASE
I have identified, named and collected photographs of many of the key players and suspects for possible arrest and criminal prosecution on charges such as involuntary manslaughter.
1. Mark B. Rosenberg, FIU President
2. Kenneth Jessell, FIU Vice President and Chief Financial Officer
3. Atorod Azizinamini - Chair of FIU’s Civil & Environmental Engineering Department and director of FIU’s Accelerated Bridge Construction University Transportation Center
Project contractor organisation chart.
Project contractor company presidents
4. Linda Figg, FIGG President
5. Jorge Munilla, MCM President
Project contractor managers
6. Dwight Dempsey, FIGG, Project Design Manager
7. Rodrigo Isaza, MCM, Project Construction Manager
8. Eddie Martinez, MCM, Project Safety Manager
National Society of Professional Engineers
9. W. Denny Pate, FIGG, Lead Technical Designer and Engineer of Record
10. Robert Murphy, MCM, Project Director
* Dwight Dempsey, FIGG, Project Design Manager
11. Kenneth Heil, FIGG, Design Quality Manager
12. Manuel Feliciano, FIGG, Bridge Engineer
13. Kristian Navarro, MCM, Project Engineer
US Army Corps of Engineers
* Eddie Martinez, MCM, Project Safety Manager
* Kristian Navarro, MCM, Project Engineer
14. Carlos Hernandez, MCM, Quality Control Manager
Elected Representatives of the People
15. Mario Diaz-Balart, U.S. Representative and Chairman of the House Appropriations Subcommittee on Transportation, Housing and Urban Development.
16. Orlando Lopez, Mayor of the City of Sweetwater
17. Anthony Foxx, Obama's Transport Secretary
* Atorod Azizinamini - Chair of FIU’s Civil & Environmental Engineering Department and director of FIU’s Accelerated Bridge Construction University Transportation Center
State and Federal Authorities
18. Rick Scott, Governor of Florida
19. Donald Trump, President of the United States
* Named more than once
Produced by Peter Dow
Science and Politics
http://SCOT.TK
We've been discussing the engineering science of the Florida bridge collapse at this link.
http://www.sciforums.com/threa...
geez, what a mess.
Is the center “truss” form bearing on the post tension slab?
I can’t articulate it, but it’s seems intuitively obvious to me why it failed...
The tower isn't there. (Not an engineer, but interned with one once).
Sometimes the cable stay tower is decorative.
My (non-engineer) hunch has to do with post tensioning the bottom platform after the truss structure was secured...Is that common practice? Seems counterintuitive...
I’m sure that the connection isn’t ridgid, but still seems like somethings off about that...I mean the point loads on that cord seem like a lot for such a thin slab...that hasn’t been fully strengthened?
Shouldn't Kevin Bacon show up somewhere in that Cavalcade of Culpability? All that's missing is Nixon's barber and my dog.
It's obvious - the Russians did it.
Armchair engineers. <sigh> Better than real engineers only because they never build anything.
shhssss. I hear the black helicopters.
.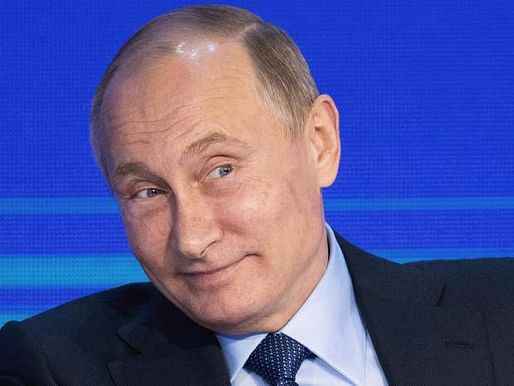
Ha, looks like one.
As I understand the construction the unfinished tower and the 'cable stays' were for show. In fact, there were no cables to be installed, just some pipe to give the appearance of a cable-stayed bridge. They apparently were trying to mimic some of Calatrava's designs without the super-expensive engineering and construction costs.
Interesting. Something about it in the renderings does look fake.
having the structure only for show is a bad way to design a bridge
This is sad. Hopefully there are no major injuries regarding this incident.
several people are already dead.
This thread was used as an example of bad internet activity at an insurance company continuing ed seminar that I attended last week. The insurance company's attorney said that a professional who engages in online speculation about this type of event, using their real name and/or any identifying info about themselves or their firm, is leaving a trail that can be used against them in future cases. For instance if you put forth a theory for why this bridge collapsed, and it turns out that your theory is not 100% correct, that can be used as evidence of your lack of technical knowledge/ability and/or poor professional judgement.
Insurance Company continuing ed: Drop your drawers and bend over.
"bad internet activity"?
This is EXACTLY what the internet should be doing. Looking at the issues raised on the "Eng-Tips" website (search 'Florida bridge') would make any architect or engineer pause and reflect on their next project. The structural engineers commenting there are making intelligent comments and raising questions about both the materials, the design, and the construction of the bridge without pointing fingers at specific individuals.
The key is to be anonymous, I guess. Neither the insurance companies or their lawyers want any of the information to ever get out or be the subject of professional conversations.
Yes, be anonymous if you want to discuss that on the internet - that was the takeaway. It isn't that they don't want information to get out - it's that they don't want it to get out, right or wrong, with the names of their insured professionals attached to it. It's that it can be used to establish what you should have known, or could have been expected to know, or as evidence of what you don't know, in some future case.
i thought it went without saying, "99% of lawyers" and insurance companies, "give the rest a bad name"....
Both have a business model that is based on profiting on the misfortune or others.
"The first thing we do, let's kill all the lawyers." -- Dick The Butcher
Oh cool, insurers read archinect. If they want to reduce risks in the industry, they should start with all the unlicensed and never-practiced-before professors that dominate the schools. Structures do need more than theory to stand up. Especially now that you can get licensed right out of school.
They read it for the specific purpose of finding an excuse to deny coverage to someone they insure In case of a claim.
Thanks to the use of an online truss calculator, I have now been able to make a more accurate calculation of the likely forces which the bridge was subjected to when it failed.
Video evidence shows that the bottom northern end joint of the bridge failed first and so suspicion has fallen upon the elements of the bridge at the north end and so it was helpful to calculate the likely axial forces along member #11 (marked "M11" in the diagrams above).
![[IMG]](https://s25.postimg.org/sqkm4b89r/criteria_concrete_column_design.jpg)
The compression force from the dead weight of the bridge I calculated as - 1367 kip or 1,367 thousand pounds of force.
The compression force from the post-tensioning (P.T.) bars within member #11 - I calculated had to be at least 304 kip but in practice would have been more, perhaps significantly more so we should have treated the P.T. bar force as a live load (LL), not a dead load (DL) for design purposes.
So the unfactored load on member #11 was at least 1367 + 304 = 1671 kip.
As recommended,
factoring the load as 1.2 x DL + 1.6 x LL suggests they should have designed for a
Maximum allowable design factored load of 1367 x 1.2 + 304 x 1.6 = 2127 kip
I estimated from this NTSB video
that member #11 used 10 x #7 bars which would suggest it was suitable for a factored load of only 2006 kip. which corresponds to a ratio of factored to unfactored load of 2006/1671 = 1.2 (only).
![[IMG]](https://s25.postimg.org/jjb7pigov/service_load_vs_rebar_choices.jpg)
![[IMG]](https://s25.postimg.org/m860fxjpr/bottom_joint_of_member_11.jpg)
To get to a factored load of at least 2127 kip, as my table suggests, member #11 would have needed 14 x #8 or 12 x #9 or 10 x #10 rebars.
Even if member #11 was not designed or constructed within code we cannot conclude that the failure of the bridge's bottom northern end joint was caused by a failure of member #11 per se.
The remains of the bottom northern end joint of the bridge
The failure which the evidence of the video and photographs suggests is more likely to be with the design of the joint itself, an insufficiency of reinforcement in anchoring member #11 to the deck, leading to, I might suggest, shear fractures along the 2 planes either side of member #11 where they intersect with the deck which I have illustrated by annotating sheet B-8 from the design engineer's drawings as follows.
![[IMG]](https://s25.postimg.org/krqd330jj/sheet_B8_cropped.jpg)
I may not know with 100% certainty what the cause of this bridge collapse is but I can offer my expert opinion on the basis of the available evidence so far.
Image - I've added some red ink to this extract from the FIGG - MCM design-build team's own document pdf proposing to FIU that they get the contract to build the bridge.
What caused it to fail?
The bridge designers innovated (incompetently) a new I-beam design of bridge but where the I-beam's upright-supports (called an "open truss") join the deck of the bridge, the designers should have specified the necessary reinforcement to stop the severely stressed joints breaking apart - "should have" but negligently didn't and so the weakest link - the northern bottom end joint - failed first and it caused a catastrophic collapse of the whole bridge.
Peter Dow, Science and Politics http://scot.tk
Science - http://peterdow.scienceonthewe...
Politics - http://peter-dow.blogspot.co.u...
Peter Dow as per the Rational Wiki.
Watch his video Valentine to Condolezza Rice or read about his cure for cancer.
This guy is Ricky on steroids and Adderall.
I've flagged the above two comments from the trolls.
This forum will be better run if trolls are banned.
@ Peter Dow
The information I posted came from following the links on your website.
You couldn't possibly be any more absurd. But don't let me stop you from trying.
How hard can it be? Here's my concept for a high shear strength steel joint for this sort of application.
Here's a closer look at my computer aided design images for the joint
So my concept is to use an steel I-beam to make something like a clevis joint.
The link is designed accept a cable connector.
I don't agree that architects or engineers should ever use rebar-and-stirrup "cage" concrete columns for a bridge truss, like FIGG have, I think, mistakenly designed for the collapsed FIU pedestrian bridge.
Instead, I'd recommend metal-only for a bridge truss's structural elements.
The obvious way to go to complete a revised design of truss member #11 (M11) starting from my joint design would be to use H / I steel beam for the full length of M11 and for all truss members which are in compression.
For a design which specifies a concrete surface for the truss members then a superficial, non-structural concrete facade could be added around the truss members easily enough.
Thank you for that, I needed a good laugh this morning.
The most obvious problem with your "design" is that if you change all the bridge members to steel then you don't need the cable anymore, because it was originally for prestressing the concrete.
Another problem is that if you encase the joint in "non-structural" concrete, either the joint will become rigid and won't behave the way you expect, or the joint will rotate and the concrete will immediately crack and delaminate.
It's obvious you have no idea what you're doing. I'm sure that won't stop you, though. Try posting that nonsense on an engineering forum and see how far it gets you.
@Schoon
Some of the bridge components are always in tension when the bridge is in situ, in normal operation - the deck members, D1 to D5 and the truss upright support members M5 and M8 for example.
You can see which are which are in tension and which in compression in my Force Bar Chart image, previously posted.
If you need to see that image bigger, use this link - Force Bar Chart
So when I wrote "use H / I steel beam for the full length of M11 and for all truss members which are in compression" I meant, for ONLY those truss members which are in compression but not for those members which are always in tension, for which cable is lighter.
The concrete facade would in sections, attached separately to each member, with a sealed joint between the concrete sections.
I already have posted this on an engineering forum.
Engineering - https://cr4.globalspec.com/thr...
You can't bluff your ignorance away by being obnoxiously sceptical. You simply come over as a troll.
So, was it the sealant between the concrete panels that caused the collapsed? Perhaps you should have specified some structural glazing silicone, then less would have died.
Caulk, the ultimate engineering solution. From the lonely heart from hell.
More goodness: Aberdeen postgrad escapes prison
Not FROM prison, from going TO prison.
@Non Sequitur
You are wilfully misunderstanding in order to troll my posts because you have nothing intelligent or educated to say about the matter.
There was no concrete facade in the collapsed bridge and even if there were it would have made no difference.
The problem was with the structural joints of the truss members.
The sealant between your bath and the bathroom wall is not there to stop your bath collapsing but to stop water penetrating between the gap between your bath and the wall.
Now stop trolling me.
I know I should not feed the trolls.
Ideally he would be banned. He is just vexatious.
By the way, this troll Miles Jaffe is a liar.
"The information I posted came from following the links on your website."
But the lying troll posted a link to the scurrilous rationalwiki website, the favourite site for trolls who have nothing to contribute to a discussion and get off on personal attacks.
Trolls are the lowest of the low in internet forums and any forum should ban them,
Your website is the best source of scandalous material about you.
Self-styled political activist fined after sexually suggestive emails to Aberdeen councillor
link source: http://peter-dow.blogspot.com/
Do you know that you can have a free profile page here on Archinect on which you can list all of the articles and videos about you that you've posted on your website? It would help expand your reputation beyond Great Britain.
Another thing, Peter - I didn't post anything from rationalwiki. But thanks for pointing me to that:
Peter Dow is a Scottish left-wing "activist", alleged scientist, an anti-monarchy campaigner and the self-proclaimed “Republican Socialist National Standard Bearer” of Scotland.[1] His bizarre one-man campaign against the British monarchy, the British state, British academia, and British sanity have led to him exposing his gibbering lunacy to various unsuspecting netgoers for some years now.
https://rationalwiki.org/wiki/...
Are there any other scurrilous webpages about you that we should be aware of?
Wow.
"Curios: how would one make such a hot rolled steel i-beam?"
What are you talking about Chris? Architects don't "make" steel beams!
Wikipedia is your friend if you really want to know all about making I-beams. https://en.wikipedia.org/wiki/...
The design would most likely specify the finished piece with a view to it being made out of one of the standard sizes of I-beams which are held in stock by steel stockholders..
The construction would presumably order the finished steel pieces from a steel fabricator who would in turn order the specified size from the steel stockholder and cut it to size and cut out the middle bit at the end, to allow space for the link etc.
If you want to know all about metal fabrication then again Wikipedia is your friend. https://en.wikipedia.org/wiki/...
Analysis of the newly released FIU bridge plans has revealed that my earlier suspicion that member 11 was dangerously under-reinforced has been confirmed, to such a degree that the collapse of member 11 under the compression load after the bridge was placed on the piers but before destressing was to be expected.
The first point to note from the plans is that the plan's P.T. bar tensioning begins once the concrete reaches a strength of 6,000 psi or more, as this quote shows -
"CONSTRUCTION SEQUENCE - STAGE 2 - SUPERSTRUCTURE PRE-CASTING
2. AFTER CONCRETE COMPRESSIVE STRENGTH HAS REACHED 6000 PSI, STRESS POST-TENSIONING OF THE MAIN SPAN IN THE FOLLOWING SEQUENCE ..."
Next, the plans recommend a P.T. bar setting for the 2 P.T. bars in member 11 which together total a P.T. bar tension of 560 KIP.
The results of my truss calculations show the dead weight of the bridge exerts a tensile force of 304 KIP while the bridge is being transported and a compressive force of 1367 KIP when the bridge is placed on the piers.
Now let us consider what all those forces together in the sequence they were applied mean for the compressive force on the reinforced concrete of member 11.
I have considered 5 different stages, A, B, C, D and E. The bridge collapsed either in stage D or as a result of damage sustained in stage D, so the bridge never got to stage E in good order, sadly, but inevitably given the plan followed.
Stage A The concrete has hardened to at least 6,000 PSI and so post tensioning is about to begin but at this stage the mainspan is still resting on the ground, so there are no troublesome forces on member 11, no PT bar tension, no bridge dead weight and so the reinforced concrete is not being compressed very much at all except under its own weight and that of the canopy immediately above it, but we will ignore that for now.
Stage B The P.T. bars of member 11 have been tensioned to the recommended amount - a total of 560 KIP and that tension force on the P.T. bars is being provided by an equal and opposite compressive force of 560 KIP on the reinforced concrete. But the mainspan is still on the ground so not much in the way of dead weight of the bridge to worry about yet.
Stage C. The mainspan has been lifted onto the transporters and now the dead weight of the bridge is exerting an external tension force of 304 KIP on member 11. This has the effect of reducing the compressive force on the reinforced concrete of member 11 by 304 KIP down to 256 KIP.
Stage D, "D" for "danger" and for "Doom". This is when things take a turn for the worse. The bridge gets placed on the piers and now the dead weight of the bridge is applying a compressive force of 1367 KIP on to member 11. So now the reinforced concrete has to take the full 560 KIP from the P.T. bars plus the 1367 KIP dead weight to suffer a whopping 1927 KIP of compressive force, which is more than the member is able to cope with, especially so if the concrete has not reached is full strength of at least 8500 PSI, as is shown in this table from my concrete column calculator and this bar chart.
The plans only call for 8 number 7 (diameter 7/8" inch, area 0.6 square inches each), axially orientated reinforcing bars, just barely 1% of a reinforcement ratio for that size of concrete member.
As I have noted there, W Denney Pate's drawings don't draw a section through member 11 with only 2 P.T. bars, only section B-B "(TYP. FOR ALL MEMBERS WITH P.T. BARS)" which draws 8 reinforcement bars. Bars marked here "7S11" are 8 size 7 (7/8" diameter) bars confirmed by the table on page 98, SHEET B-98, SUPERSTRUCTURE REINFORCEMENT BAR LIST AND NTSB images.
It's inadequate reinforcement for the compression before destressing the P.T. bars.
So it turns out that this picture was "the smoking gun" after all, but not for the reason I thought at the time, but because it shows one of the far too small and far too few reinforcement bars, marked "<-B->".
Stage E. After destressing is complete. We don't know for sure if this stage was actually reached, but even if it was, by that time the damage was done and the member 11 was failing and bridge had begun the process of collapsing and it was just a matter of time.
One small post for a scientist, one giant leap for forensic engineering.
Peter Dow, Science and Politics
You're still beating on this dead horse? That moving bush on the grassy knoll was just the wind.
^ The "Politics" part is particularly good reading: Peter Dow's Political Defense Blog
http://peter-dow.blogspot.co.u...
Back on topic, Yosemite Sam has a theory that Marvin the Martian caused the bridge collapse.
I don’t know why people keep buying stuff from ACME.
Now considering member 2, which survived intact,
member 2's "SECTION C-C" -
- has 12 x size 8 (diameter 1", area 0.785 sq-in) reinforcing bars and member 2's P.T. bar force setting is
560 kip (same as member 11).
My truss calculation results were -
in transit tension of 458 kip
in situ compression of 1920 kip
Now let us consider what all those forces together in the sequence they were applied mean for the compression force on the reinforced concrete of member 2.
At the critical "Stage D", when the bridge is placed on the piers but before the P.T. bars can be destressed, the reinforced concrete of member 2 has to take the full compression force of 560 KIP from the P.T. bars under tension plus the 1920 KIP dead weight of the bridge to suffer a total of 2480 KIP of compression force, but member 2 was able to cope with that load of 2480 kip, so I calculated the maximum allowable design factored load to find out how strong the concrete must have been, in this table from my concrete column calculator and this bar chart.
Therefore the survival of member 2 may be expected, during Stage D anyway, if the strength of the concrete was 7,000 psi or more, albeit a reasonably safe load factor (at least 1.2) is not to be enjoyed until the concrete hardens to at least 8,285 psi.
Simply applying commonly used engineering design equations for concrete columns suggests clearly why member 2 survived but member 11 failed. Pate's under-design of member 11 was significantly further out of code than was his design of member 2.
Love it.
Braveheart was a great scottish documentary.
Poppycock
Block this user
Are you sure you want to block this user and hide all related comments throughout the site?
Archinect
This is your first comment on Archinect. Your comment will be visible once approved.