Dwell Magazine, in the October 2009 issue, features a professionally designed 2 bedroom home in Houston for a professional couple utilizing ISO shipping containers as key structural elements. It was a successful enough approach that two more private residences utilizing shipping containers are now being built nearby.
This year Jure Kotnik published "Container Architecture : This book contains 6441 containers," featuring completed professionally designed projects from around the globe, including a student housing complex in Stockholm using 1026 containers, a cruise line center in Hamburg using 48 containers, a museum in Seoul using 166 containers, and a broad range of private residences using 1 - 12 containers as key elements.
The MOMA "House" show last September featured an ingenious hi-tech portable dwelling in a single container.
The New York Times ran a feature article a few weeks ago on a West Texas getaway constructed from 5 containers by the former art director of Rolling Stone.
Previous discussions on this topic here seem to have been dominated by haters of the concept and nay-sayers, but there are obviously also a number of architects and designers engaging with the possibilities of working with what is currently a very large supply of very strong and relatively inexpensive space enclosures, at a time when the cost of more conventional building materials and techniques have gone sky high.
I'm interested in hearing from anyone who is currently working in this arena, especially for private dwellings.
It is fashion, simple as that. "Cool". I don't think anyone argues with that (it is subjective, of course). Where the problems were was when people were suggesting that it would save a lot of money, which it doesn't (not to my knowledge).
So "cool" being cool, all's good. It'd take a lot more than ideas to convince me and others that this was an economical approach.
I worked on one..
The main problems we ran into were...
Some Cons...
1. Condensation management , i.e. managing water in the wall cavity
2. Conductivity. Romex works but you have to pay special attention to the panelboard and all adjacent wiring. Grounding PV is also an extra layer of concern
3. The floors are sometimes a 3/4" to 1" Pressure treated and creosote treated plywood. Perhaps a lil too toxic for some people.
4. Codes...if you plan it in a major city...you may have an extra bureaucratic layer to deal with. Of course you can use the special section of the IBC
We used them in the design of a project for an office building in Atlanta, Georgia which was never realized. The Atlanta officials were okay with it, and we actually received a permit. The issue was that as soon as pricing came in, there was not enough savings to justify the use. Maybe it was how we used them/cut them up, but we could have done a small "regular" building more inexpensively.
Now I am in Lubbock, Texas and there is a residential/studio/gallery project where they may be used as a storage units within the design. The person I am working with spoke to the city early on, and the officials were open to the idea here as well.
All in all, I would say they have a use, but when you start cutting them up, add in the cost for skinning them to relax heat gain, etc. you can quickly lose any initial savings.
I still find them to be interesting objects which can be used, but I do not find there use in the industry innovative any longer. It also seems that justification for use in some of the projects I have seen is very suspect.
As a means of recycling, building with them may be a good thing, but there could be a better use.
I've worked on several container building concept designs and proposals for such, so it was my job to pretend I believed in it and sell it, but I'm not convinced they are a good idea either. They do become more economical past 4 stories, but 4 stories and under they are the same as wood construction or more $$$ (for multi-family construction at least.) If the design is simple enough, you can save a lot of time though. The concept is novel, but limiting because of the 8' widths. I do think there are some legitimate applications, like emergency temporary medic stations in the jungle, which is a job we were going for, but didn't get.
I'm all about the recycling, but theres some pretty basic problems to deal with:
- extremely unsustainable timber use in flooring in standard shipping containers (often virgin rainforest wood, or heavily chemically treated)
- the width of a container makes them difficult to use, so you have to find ways of opening them up, which lessens the advantage of a pre-sealed box.
- all that welding and steelwork isn't easy or cheap.
- have you ever hung out in a shipping container? hot and stuffy.
not that there isn't ways around these, but I don't think shipping container architecture will ever be a huge thing.
Like I said before, the haters and naysayers are plentiful. That's what Dr. Edward de Bono calls "black hat thinking," in which you just criticize what you think is wrong. If that's your bent, save your breath, I've already heard it all in previous discussions here. I'm hoping, instead, to find a few people here who are interested in having a "white hat" discussion about what is right with the concept. And maybe some creative discussions about the best ways to take advantage of the resource.
So I'll kick things off by mentioning several key points:
1. ISO Shipping containers are inherently very strong. They are designed to be lifted, fully loaded (58,000 pounds net load, plus the 8,000 pound weight of the container for a 40' unit), by sling points, and can be stacked 8 high on the deck of ship. And they're weatherproof. Anchored to concrete groundpads, a stock unit can easily withstand a storm that would demolish a mobile home or severely damage a frame construction building.
2. In some locations they have piled up in huge quantities, because of trade imbalances. In these places merely disposing of the excess has become an environmental issue.
3. In the "Reduce - Reuse -Recycle" paradigm of current environmental thinking, Reuse is superior to Recycle, because Reuse does not waste the original fabrication "costs," and does not incur additional costs to reclaim the material and refabricate a new product. So finding valid second uses for shipping containers is an environmentally sound practice.
4. Because of their transportability and inherent modularity, they can be quickly deployed for "immediate need" shelter, and structures can be incrementally expanded as required.
5. Because of the large surplus of containers, the cost of enclosing space with a permanent structure is very low compared to onsite construction of any modality. A 40' unit (320 sq ft) in most of the U.S, currently runs $8 - 16 sq ft total, sited, depending on location.
So that's a start. Given those parameters, what are valid uses of the resource?
That's what Dr. Edward de Bono calls "black hat thinking," in which you just criticize what you think is wrong.
Usually, I do criticize what I think is wrong. But I call it "no hat thinking" aka simple logic.
But to your question: all the reasons you listed above are potential benefits for, as you say, immediate need shelter. But in your earlier post you asked about private residential projects. This is a pretty wide spectrum, and at the private residential end of it, shipping containers will always be, for all the reasons others have noted, a fetish/funky alternative building type. The economics just rarely make sense.
One question I have is: is there still a shipping container manufacturing industry? Because clearly we have enough.
There are huge problems with shipping containers. to refer to LB, a new 40ft hi-cube shipping container [yes, still being built] costs approx $USD100,000 to build - in my metric thats 28.5m2 or $3500/m2.
Any model using shipping containers has to rely on old shipping containers which come from a variety of sources in a variety of states as agfa8x mentions above. Some containers have to be of a certain class to transport goods. So there maybe a heap of spare containers out there but they are effectively useless for their original purpose.
Some fall off the back of ships, and are picked up and sold to numerous factories in China and Vietnam for reuse. Most have toxic timbers for floors that needs complete and controlled removal
Structurally, they can be rigid, but once you start playing around with the frame or the walls, this vanishes. There is little or no IP involved. A monkey with a blowtorch can modify a container.
The dimensions are difficult to make work. There are alot of issues with insulation and ventilation.
My question is this, and its simple: why get involved with a business model where your methodology cannot be protected? Even the big shipping container modifiers like Verbus Systems have very limited patents that only apply to logistics rather than construction detailing.
your first post is indicative of a flawed premise; just because Dwell and other publications or institutions feature these containers hardly makes it new or newsworthy. typically media or institutions are lagging indicators of what's "in." certainly a case point; the first time i can recall shipping container[s] being used by architects, was at least 7 or 8 years ago[?] - Pugh & Scarpa and then Michael Rotondi, Jennifer Segal, and i'm sure more examples exist...
again shipping containers and modular design have become so fetishized that local architects think that PODS containers can be utilized for homeless housing. can you believe that? essentially upgraded cardboard boxes used to house homeless?
Agreed, reference Jones Partners High Sierra Cabin series from 1995.
For a slightly tongue-in-cheek take on homeless housing, has anyone recently looked at Jones Partners 'Housing for the Homeless' from 1985. The cash for clunkers program could have helped to implement this proposal.
For those interested in digging into this a little bit, the criticisms so far mostly miss the point. I'm not saying the use of shipping containers as an architectural element is the solution to all the world's ills or even makes sense in every case. But what I am interested in exploring with others is those situations where it could make sense.
Take Hawai'i, for instance, where almost everything, building materials included, arrives in containers. And far more comes in than goes out. So there is a permanent surplus, which translates into a permanent disposal problem as well as a permanent possible resource. And in that same area, cost of living is high, cost of construction is sky high, while average income is low, and that translates into a permanent shortage of affordable, low cost housing. Conventional home ownership is simply out of reach for a very large percentage of the population.
Used good condition 20' standard containers can be purchased today in Hilo or Honolulu for under $3K, while new ones sell for about $5K. Single use (one trip only) 40' High-cubes (9'6" tall, 8' 11" inside) are about $8K, while good condition used are under $5K. At least one entrepreneur is building and selling a fully permittable 320 sq ft basic living unit on Oahu out of these 40' single use containers with bathroom and efficiency kitchen, wiring and lighting, door and three windows, drywall, insulation, and shed roof for about $25K, or $17K without drywall and roof. For some people that can make private home ownership affordable, even if it is minimalistic. And there is always the possibility of incrementally adding to the size of the home in the future.
But people's thinking about adding to a basic shelter single unit naturally gravitates toward placing a second one next to the first and attaching them. And many designs to date have followed that logic, stacking multiple containers side by side or on top of each other like Legos. What I really like about Christopher Robertson's Houston design is that he took the concept to another level by placing two 40' containers about 20' apart, bridging the space between them with a floor and roof, and enclosing the open ends. The containers serve as "really wide walls" as he puts it, with a large great room surrounded by bedrooms, bath, etc. in the "wall space." It's a very flexible concept. And it even holds the possibility of being built incrementally, with a basic "starter" unit eventually morphing over the years into a full sized family dwelling.
yup, go for it if you want, but make sure you look up all the precedents we all mentioned. Jones and others were using modules, stacking, putting walls between, etc., 15+ years ago (and look how far they got!).
Just like prefab, there are great applications, but for general cost savings they don't cut it.
1. Condensation management , i.e. managing water in the wall cavity - OpenD: what do you think of the possibility of using foam-in-place insulation between the corrugated steel wall and drywall? Polyurethane foam is non-absorbant, non-flammable, an excellent insulator, and essentially non-degradable except by UV exposure.
2. Conductivity. Romex works but you have to pay special attention to the panelboard and all adjacent wiring. Grounding PV is also an extra layer of concern - OpenD: check
3. The floors are sometimes a 3/4" to 1" Pressure treated and creosote treated plywood. Perhaps a lil too toxic for some people. - Open D: on the wet side of the Big Island of Hawai'i (Hilo side) this might be an advantage, due to the high incidence of termite infestation. Wood used within 12" of the ground is required to be pressure treated anyway. One approach I've seen used is to lay up a ceramic tile floor over the ply. Seems to be an effective barrier against toxic fumes in the living space. Comments? Ideas?
4. Codes...if you plan it in a major city...you may have an extra bureaucratic layer to deal with. Of course you can use the special section of the IBC - OpenD: most of the land on the Big island falls under county regulation, not city. Building codes are fairly standard to US norms, but the Building Department is chronically understaffed and enforcement is, shall we say, lax. Matter of fact there are currently an estimated 1,000 non-permit homes in the Puna region alone. The county has begun to come to terms with the idea that working with unconventional construction to insure safety and health concerns are addressed, and to get these buildings on the tax roles, is a worthwhile effort. A couple of weeks ago county commissioners unanimously approved the use in Puna Dsistrict of temporary shelters like tents to be lived in for up to 2 years, off the grid, while construction covered by a permit is being undertaken. And the precedent is already established, with a number of container structures already built and occupied under approved permits.
So while the approach may be discouraged in other areas, where it is permitted, why not make use of it if the requirements are a fit? The main barrier left today is the need for for professionally drawn plans stamped by state licensed architect and engineer, but the widespread use of package home kits and package plans in the area indicates to me that the cost to an individual owner with limited resources could be made attainable with well designed, attractive standard plans.
As a side note, I find it interesting that the bulk of the alternative, environmentally sensitive design today is happening at the two extremes of the economic scale... with wealthy owners who can easily afford the high costs of cutting edge LED lighting, solar and wind power, separate greywater reclamation and blackwater systems, etc.... and with low income owner/builders who are working with salvaged materials, homemade solar water heating, rammed earth and hay bale construction and the like, simply because it's what is within their reach. Interesting.
Their detached residence concepts are interesting, if limited, but their attention seems to be on larger complexes. I haven't seen their small structure concepts evolving beyond the original "swiss army knife" unfolding container, and overhanging stacked blocks approach that have been pictured on their site for quite a while.
Wes Jones? Not familiar. Any references you can point me to?
"i have a friend that is working on a 20 home subdivision in sarasota, fl that is using shipping containers..."
Interesting? Any online references you can point me to? I'm particulary interested in gathering more information on actual experience vs concepts.
There are several reasons as to why shipping containers are not an exceptionally great idea. Notice that I said "exceptionally great" and not just bad.
Shipping containers are considerably pricey-- when you compare them to the at-cost price of manufactured homes and trailers:
* A FEMA trailer-- sans overhead costs-- runs between 13,500 and 15,500 dollars.
* A single-wide mobile home at-cost runs about 8,000 to 15,000 dollars.
* A "manufactured home" is ball park 12,000 to 21,000 dollars.
Remember, these are at-cost prices out-the-factor-door. If you add research and development along with delivery, it adds some expense onto the cost.
If you were to build houses at a similar size minus the costs of architectural services, permitting, land et cetera... you could build more-than-affordable "real" houses for $50 a square foot with a high level of finish. Obviously this would require government intervention but if the goal is providing shelter... private business has no business in this discussion. Get the government to subsidize concrete and that figure plummets even further.
Now to the weight part, a "dry weight" shipping container weighs about the same as a finished mobile home at a similar size. I think a 70' single wide weighs about 26,000 lbs-- 370 pounds be linear foot or 25 lbs per square foot. So a 40-foot single wide would weigh about 14,800 pounds.
Hawaii's roads are not as weight-rated as roads on the mainland. Any planner would scorn a project for just this reason... with similar weights, they will both equally damage a road. However... with shipping containers, you'll not only have the weight of the container but the weight of the concrete, finishing materials and so on. So, there is a hidden cost here. If moving them completely finished as units, one must factor in whether the roads are rated to handle that enormous weight.
Essentially weight will be a limiting factor. Standard construction can usually mitigate this with smaller and more divided loads.
I have no particular issues with conductivity. The only issue I might possible bring up is radio interference. Since the entire structure is made of ferous metals, I'd be mildly worried that the close contact of electrical wiring and steel would produce radio noise and possible interactions with cellular, wifi and tv signals. I don't see this as problematic but there's a possibility of feedback interference (hissing and whining) that might be amplified by operating plasma tvs or devices that emit microwave radiation.
I did a quick search but found little-to-nothing saying one way or another since there's very little precendent of people living in solid steel structures.
The pressure treated lumber is dead on. If I a remember correctly, most food in hawaii is shipped by plane. So I'm not entirely what the availablity of finding foodsafe (which would automatically inhabitable) shipping containers. The other problem with shipping containers is the paint. Most industrial and high-performance paints are incredibly toxic from the paint itself to the pigments in the paint-- technically, most pigments are not chemically inert either.
So, to prevent your property being deemed condemned or brownfielded... all containers would have to be completely stripped and repainted. You'll have to pay quite a hefty amount to have the paint chips and dust removed and disposed of by full plasma valorization-- i.e., super expensive.
On to the moisture, I do not currently know enough on this subject. However, weatherproof containers are air tight which presents a different health problem and a structural problem especially in dealing with a "reactive" material like the metal used in shipping containers. The metal in shipping containers is not purposely designed for high amounts of chemical exposure-- i.e., why they are often "single-use."
While a common concern of indoor air pollution, the use of many different types of household chemicals release caustic gases (chlorides [chlorine gas and choloroform], ammonia, dioxins, various oxides et cetera) that may over time severly damage an all steel nearly airtight enclosure.
In addition to that, this presents unique fire hazards as well which may not be fully understood. That brings me to your other point, untreated polyurethane foam is highly flammable once it begins to burn. On top of that, burning polyurethane foam releases hydrogen cyanide. I'm not sure about you but I'd rather not be inside of a steel box filling up with cyanide gas.
---
Lastly, like any major tourist destination, the housing price scheme of Hawaii is really messed up... almost bordering on locational discrimination.
The tourism industry relies on armies of low-wage workers but no one on vacation really wants to see that reality. Businesses will often force a "suburbanization" of these workers to places where incidental contact is more than likely not possible. The tricky part with Hawaii that makes it particular is the limited amount of land. Almost all land in Hawaii is valuable and the working poor can't compete with the monied higher-paid individuals who want the "authentic" Hawaiian experience or the vast amounts of rental vacation homes.
So, where do you put the poor when everyone wants to be everywhere? The problem with a place like Hawaii (and it is really no different than Florida or Jamaica or any other place) is that people need to face the reality that poverty is an inherent part of their business plan and need to be inclusive instead of exclusive.
Very interesting points, Orochi, especially the bit about locating the poor people away from where the rich people want to vacation.
I'm still feeling like the bigger question isn't "What should we do with all these containers?" but rather "Why do we have so many of these containers?" If they can't be reused after one use then that's a completely unsustainable industry, right? It's taking a disposable attitude towards an enormous use of material.
It seems both Orochi and I are proposing that vis a vis wage discrepancies and surplus materials people are coming up with a plausible solution, but it's only because they are asking the wrong questions.
Granted, alternative projects (like Project Pink, or the Manhattan Airport proposal) are very often a great way to start a discussion of a real problem.
Orochi, thanks for playing. You haven't quite got the hang of "white hat" thinking, but I appreciate the input.
"White hat" thinking, to take another stab at explaining it, is where you set negative criticism aside and consider only the positive aspects of something. It's not the only way one should look at something, but as a phase in planning, it is a way to get beyond our cultural bias in the Western World for black hat "whats wrong with it" thinking to dominate all else. One of the factors that is credited for the phenomenal industrial growth of post-war Japan is that they have a very different cultural bias. It's considered rude to attack another's ideas.
I've simplified the case, but in short, Japanese designers and engineers come at the design process very differently than Westerners. They tend to elevate ideas as long as they have support, whereas in the west we are more prone to shooting down ideas until only one is left standing. I find the first approach more conducive to creativity. When I hold "think tank" meetings I ban the word "no," and make it safe for anyone to propose anything, free of criticism. It seems to work well to spark "outside the box" thinking, which can lead to real breakthoughs.
Orochi, now I'll slip on my own black hat for a bit to consider your objections...
First, you're comparing apples to pineapples. Costs of construction are much higher in Hawai'i, so $50 sq ft is not a realistic comparison figure. And those FEMA trailers, which would blow away in a wind that wouldn't faze an ISO container, same deal. Either you'd have to ship the materials in and assemble them locally, or build them elsewhere and ship the finished units in, either of which is costly.
A big plus for reusing containers is that they are already there, in large numbers. Asking why they are there is not really germane to the question of what to do with what is already there. And they're not "single use" because they can't be used again for shipping, they're single use (when they are) because the economics of shipping empty containers back where they came from doesn't support it. Same reason you don't send a can back to Campbells for a refill after you've eaten the beans. These are just bigger cans. And my question is, what are possible valid uses for these big cans, since they can be purchased intact for salvage value prices?
Besides the old bent up rusty containers y'all seem to be thinking of, there are also virtually new unpainted containers, some made of corten steel, some of aluminum. And 20' containers can be trucked in to most places where larger ones won't go.
On the foam-in-place rigid ployurethane foam insulation question, I slipped a cog when I called it nonflammable, but neither is it highly combustible. Even without added fire retardant, it is what used to be called "self-extinguishing," and it takes sustained very high temperature to set afire. I've seen photos of a dome home in California that had an exterior of polyurethane foam with a vinyl skin, which was the only structure in its area to survive a huge wildfire. The only damage was a small area where the foam melted away under the sustained blowtorch of 100+ mph winds and 40 foot flames. It is considered safe for insulation in many uses when covered with plaster or stucco, or for crack and crevice sealing, like around pipes and vents or windows and doors. Still, toxic outgasssing under the high temperatures of a sustained fire in an enclosed space is a valid issue. Where i had originally envisioned it being of possible use is on the exterior, sandwiched between the metal corrugations and an exterior skin to provide weather insulation, where that wouldn't be a concern. .
As to the poverty issue and how it affects the housing picture in desireable vacation destinations, I couldn't agree more. But while we're waiting for the big picture to be improved in some way, on the micro level there are still real people in need of real housing today. Container based housing may not be THE solution, but it's possible it could be A solution for some. And that's a question I'm interested in wrestling with.
For anyone interested in learning more about ployurethane foam insulation, there's a useful book by David B South called "Urethane Foam: Magic Material - and the Best Kept insulation Secret!" It's been out of print for a while, so he put it online as a free download at htttp://www.monolithic.com/stories/foam-chapter-00 Now the book is back in print, but the free content is still online at the moment.
Despite the hokey title, it's actually a practical reference. Drawing on a long career in the polyurethane foam business (at the peak his foam company was applying over a million pounds of foam insulation per year) and his later work with thin-shell ferrocement domes, which use polyurethane foam both as a mold form for sprayed concrete and as an exterior insulation material, he tells it like it is, and like it isn't.
In Chapter 5, on Foam and Fire, he strongly cautions against using unprotected polyurethane foam as interior insulation, but follows with:
Urethane foam is an excellent fire barrier when used on the exterior of a building. There are numerous examples of urethane foam roofs saving a building from fire. Burning brands * and debris can lay on a urethane roof for a considerable time before burning through. The urethane insulated roof will simply char. If there is no external heat source, the fire will go out. It requires a lot of heat to keep urethane foam burning. Where heat can radiate into the atmosphere, urethane makes a superior fire barrier.
We have a gentleman in Fort Worth working to develop shipping containers as transitional housing for our homeless population. He has received a fair amount of media attention and has been battling it out with city council for over a year.
I have met with him several times now and we are pushing to engage the design community, lead by our local Architecture for Humanity chapter, in the design process of future units.
He currently has a one-unit residence constructed on an industrial site, the final hurdle being the acquisition of city land. According to him, he purchases the 8' x 48' units out of Houston for around $2700 and can finish them out at a per unit cost of between $12-15K. As I understand it, the key cost component is the final leg of transportation; that is, getting the unit off the train and onto your site.
I believe this low-end, residential application to be the only economically viable architectural solution to the growing surplus of container units.
One of the interesting things about his approach is that for what I call Tier 1 housing (the homeless), he has the wisdom to redefine "home" as "a safe place to sleep," and to address that need directly.
It's hard for a lot of people who do have homes to get past the fact that Tier 1 housing doesn't satisfy THEIR OWN needs, but it's a worthwhile improvement nevertheless for those who have been sleeping in cardboard boxes, or under tarps or bridges. And I think it is a key distinction to make in trying to find solutions to the homeless issue. As Abraham Maslow pointed out in his "Hierarchy of Needs," until the most basic needs for food, water, and a safe place to sleep are met, higher needs are not motivators.
"I believe this low-end, residential application to be the only economically viable architectural solution to the growing surplus of container units."
I see the man in Ft. Worth is already planning to use containers in his approach to "Tier 2" housing as well, as a step up from Tier 1 into fully equipped small low end dwellings. This will be more difficult to achieve, but again, I think it is a worthwhile ambition, and one containers could play a part in.
Agreed. Given the Tier 1 approach, a redefinition of "value claims" is key to public appeal (and political appeasement). Maslow's hierarchy of needs is an interesting interjection, however I believe a multi-leveled approach is necessary in light of the negatively-skewed perception of shipping containers as dwelling units. In other words, one must appeal to not only physical needs, but also factors which influence the interdependency of physiological and emotional needs as well.
I believe these "value claims" must supercede any performance or aesthetic claims from an architectural perspective. At Tier 1, housing is not just a tectonic artifact for dwelling, but a symbol of dignity and stability, than architectural "honesty" and "transparency" et. al. can come. Having a place to sleep possesses an inherent dignity. This seems to be the central claim to his effort.
Another potential point of contention with shipping containers and their use of housing is the sacrere of our [Western] own culture.
What kind of society do we live in where consumerism runs so rampant that we are now resorting to the idea of living within the boxes of the products that we use to decorate our houses?
Something is amiss here-- especially the idea of housing our discarded population in the boxes that house boxes. That notion lacks any sort of sanctity we have in our own belief of universal human rights. It sends the message to the people we are trying to help that we are trying to put our human "trash" into the "trash" that more or less is a major factor in them becoming human "trash" in the first place.
Is this really where our society should go? Should we all resort to living in the boxes of boxes? Should we treat everything as disposable and recyclable?
I do not necessarily feel that there is any dignity in this marginalization of marginals.
Red hat off, Blue hat on.
Detachment from the subject and the object is necessary. The judgment and idea most of us are making is that home is box with four sides, one door and two windows that sits on a piece of land.
Home has many meanings. A home is not just a house. When planners, researchers and architects approach subjects like this, they often always apply what their life from their point of view is.
Home ownership and its benefits are often a fantasy of the middle class. They believe strongly in the idea that ownership infers some sort of glorious benefit whether it be personal freedom, personal expression or monetary gain.
However, this persuasion is often of ethos or pathos. It rarely is rooted in logos. Ownership is not for everyone nor are the benefits as spectacular as one would like to think. Renting may not necessarily be the better thing either.
The point is most homeless people and people in deep poverty often end up there for many reasons. Paranoia, disability and disenfranchisement are some of the bigger reasons. While disability requires it own special approach, the other two are blockades to projects such as this.
Essentially, many "easy routes to homeownership" projects, affordable housing projects and other schemes seem to apply the preference of the helping crowd to the needing crowd. The process is essentially is making someone else walk in your shoes without walking in their shoes first.
I think for these things to be acceptable and not doomed to failure, we have to detach ourselves from the projects. Just because someone is homeless doesn't always mean they need or want a house or shelter. And their idea of a house or a shelter is probably much different from what we percieve to be a house or a shelter.
Blue hat off, yellow hat on.
A recent study points to the fact that there is enough self storage facilities in the United States to fit everyone in the country inside of them.
Instead of repurposing shipping containers, why don't we just out law new construction of new self storage facilties unless they are made out of shipping containers? It only seems natural that a container made for storing cargo would be better suited to storage cargo.
I think it probably might be even easier to rehab self-storage facilities into apartments than it would be to rehab shipping containers into homes.
Yellow hat off, black hat on.
Most of the studies regarding the flammability of polyurethane foam have been done by the Polyurethane Foam Association.
Anyone arguing the fact that polyurethane foam isn't as flammable as advertised should really consider that a majority [or maybe large portion] of structural fires that result in death are caused by dropping cigarettes on polyurethane foam.
Flexible polyurethane foam is suppose to be less flammable than rigid foam. It is even suppose to be flame proof against smoldering fire hazards. So, explain to me why a product that is suppose to not burn has killed soo many people and destroyed soo many buildings?
I checked the research and most of the research regarding PF involves treated or self-extinguishing foam and a bulk of this research was conducted in the 1970s and the 1980s. So, my hypothesis is that the slim availability of third-party facts about the the flammability of polyurethane foam is that no one has ever extensively studied it because it was a known fact that the stuff is flammable.
Furthermore, the PFA states on their website "Flexible polyurethane foam (FPF) is an organic material and, like all organic materials, is flammable." And to add insult to injury, "High risk occupancies should consider having fire detection, fire alarm and fire suppression systems."
Why would an association that says their product is not that dangerous recommend having fire suppression systems if you use their product?
HMM.
Black hat off, white hat on.
Maslow's heirarchy of needs is an important topic. However, the most effective form of housing the homeless and poor is known as the "housing first" approach.
The approach utilizes existing housing stock and assigns individuals to a collection of properties across the given area. Unlike homeless shelter approaches and other "camp like structure," housing first is showing to have a much higher success rate and a lower total cost.
What the aim is too fully integrate these people into society, away from other homeless people and to give them responsibility. It works better because this option really assigns no identity or cultural construct to them outside of being "regular people." The only thing that is different about them is the regularly scheduled visits from social workers making sure the person is complying with the program details.
It is more expensive upfront but over the course of a year is somewhere between a 1/4th and an 1/8th of the cost of keeping these people in shetlers, jail or "communities."
White hat off, green hat on
Considering the "hierachy of energy consumption," perfectly good steel would be a waste to turn into housing. If we were to talk about this from an ecological point of view, the biggest consumers of electricity are-- from least to greatest-- concrete, glass, chlorine, rubber/tar, iron and finally steel.
So, essentially, why should recyclable steel be used when energy and emissions are right now such huge issues?
If anything, a state like Hawaii should open a steel recycling facility that operates as a non-profit to reduce costs. It could then trade containers of shredded steel casings for concrete and then use that concrete to build real, affordable, centralized and urban-ish housing for its poor and homeless population. You know, considering concrete would be a more appropriate material in a place like typhoons, high amounts of rain and a landscape that oozes sulfur from every pore.
Along with redefining what a home is, we might also redefine what ownership is. Ironically Hawai'ian native culture did not have the concept of ownership Westerners later imposed on them. All the land was seen as being for the common good, and tribal allocations were made based on need, and re-evaluated as conditions changed. The requirement for good stewardship of the resources available was a given.
In regard to the Ft. Worth Tier 1 project, ownership might be defined something like "it's yours to use as long as you want it and need it, so long as you take care of it and don't break the rules." That would not work for everyone, and some wouldn't even be interested, as you said, but for some it would be a step up that could make a huge difference. And for Tier 2 projects I can see a co-housing approach being a possibility, on publically owned land, with individual units having basic facilities plus access to shared facilities.
"Housing first" is a great approach if you have existing surplus housing stock to work with. But in some places, as diverse as Hilo and NYC, you just don't have that resource.
Recycling the steel from the containers in situ has possibilities, but if it were that simple i think it would already be done, which it largely isn't. For Hawai'i I think the the key obstacles to overcome would be the lack of required infrastructure and very high energy costs. Ironically the use of steel frames in mid range house construction there is trending up, despite rising material costs, as stick-built wood construction costs climb out of sight. Steel has proven to be a very good material to work with in the area, especially given the seismic activity and hurricane risk, not to mention widespread termite problems, so long as you take easy and appropriate steps to remediate the environmental factors you mentioned like rain and volcanic sulfur in the air, where it occurs.
Regarding rigid polyurethane foam, it's not the same stuff as soft polyurethane pillows and upholstery, so you really can't compare them in any meaningful way. I've experimented with one of David South's key assertions myself, holding a well cured chunk of rigid polyurethane insulating foam in one hand, while applying a blowtorch flame to it with the other. As long as you hold the torch flame steady on the foam it will oblate, and as long as there is no wind you can eventually work up a little lick of flame. But take the torch away and the flame dies immediately. Meanwhile the back of the foam stays cool. It is this extremely low thermal transfer that makes it, in South's words, a better fire barrier than concrete.
I love your idea about mandating the use of containers for self-storage facilities. The big name facilities I've seen are typically built very much like a complex of shipping containers, but of much flimsier material. You really have to wonder why. And the reuse of containers for larger structures like apartment complexes and hotels and offices is already happening at a rate you can't ignore... almost everywhere except the US. You really have to look to other countries for the best examples of what is possible when considering "what does a shipping container want to be?"
We met with the owner last night and are moving forward with a collaborative design work session with architecture for humanity, client, city officials, financiers and a possible jury. Will keep you posted!
You might also take at look at what this guy in Oahu is doing. He's got an approach to a portable single container, 320 sq ft studio with a bathroom and kitchenette that meets legal standards for the area, has made it through the building permit process and has been sited.
On another page he's got a 4 container 1420 sq ft house that he says the State officials love, and are in discussion about building a couple for their use.
What he needs, obviously, is a good architect to take these to the next level of design, but his basic concepts are also obviously workable, because he's gotten 5 structures built already.
most shipping containers - or at least a large portion - are only used once. this is because of trade imbalances. most countries are either goods importers or exporters. not many import and export equally. large consumers like the usa consequently have a lot of surplus containers.
It very much depends on the market. In the Hawai'i case I'm looking into, many containers are surplus after a single trip because of the large imbalance between what is shipped in, versus what is shipped out. Surprisingly, you can even buy new locally made containers in Hawai'i, as you can elsewhere in the United States, because some shippers insist on using only pristine new containers. A few homebuilders wanting the best quality, even at higher cost, have been known to buy new ones for that reason.
More typically, in most American port cities, like Houston, there are a wide range available for purchase, from scrap metal grade to like new, with many having had enough use to require small repairs before reuse for shipping, like patching the floor or welding a hinge. The more use they've had the more beat up they are, and the lower the price. The cheaper ones are popular for use as small steel buildings for storage, workshops, hunting cabins and the like. The better, newer ones are in some demand now for architectural use.
If you want to research the lifecycle on containers before they are resold, each ISO standard container has a metal data plate on the end that gives the date of manufacture, original owner and other information. From that you might estimate possible use, factoring in load time, transit time, unload time, and lull time before trunaround. You can also check the auction sites where containers are sold, like eBay and the shipping industry specialized sites, where some sellers list manufacturing date and condition in the details of their offerings.
In the Hilo area, you can currently purchase a single use 40' container and have it delivered to your lot for under $5K total. That's less than $16 per sq ft ft for a strong, weatherproof enclosure that only takes a day to site, compared to $50 - 75 per sq ft for materials alone for kit house that will take a month or more to make weathertight. Plain vanilla very basic prefabs run maybe $125 sq ft. It's easy to see why some people are choosing to go the container route on owner-built projects, where they put a couple of containers down, add simple shed roof, and work on upgrades as they go. It's thought there may be as many as 1,000 of these already in use in the Puna and Ka'u districts.
My own biggest interest is in moderate to mid-range contemporary style residences, where the expectations for fit and finish are higher, but where there is a tremendous squeeze right now on the buyers needing housing. As I said earlier in the thread, i don't see this as a panacea for the world's ills, but as one possible approach, that when intelligently used might provide cost savings which could make a difference for a lot of people. The Houston house I mentioned earlier has a basic concept I think is quite scalable, using containers as "side walls" and main supports for the structure, then enclosing the space between, for buildings from 360 sq ft to 3,024 sq ft and up.
Here's a quick update, in case anyone trips across this thread and wonders what conclusions i reached.
1) The single biggest go/no-go factor is transportation. Not just transportation costs, but whether or not you can even get the desired constainer to the site at all. For a specific project that I was considering a multi-container design for, the site proved to be impossible to get 40' containers into due to narrow access roads with sharp corners. For another site a mile away with better access, no problem, and the design is viable there.
2) A single module has challenging dimensions to work with for residential use, but this can be remediated by using 2 or more containers side by side, or augmenting the 8' side to side dimension with additional construction. Spacing two parallel containers a distance from from each other and enclosing the central space is a flexible and inexpensive approach with many possible applications.
3) If you simply treat containers as another material resource, there are valid uses to me made of them. Just don't force the issue if it isn't a good fit. In the project which is moving forward, a 20' container, loaded with building supplies and tools will be shipped to the site, and used to secure them while the main building is constructed. Then it will be incorporated into the final structure to house utilities, laundry, pantry, and storage, and serve as support for a deck extension from the second floor. Although there will be some expense to add siding, it is literally a "bonus" room for the building, better than free, because otherwise it would cost money to haul it away at project completion.
Best of luck,
OpenD
Dec 14, 09 11:14 pm ·
·
Block this user
Are you sure you want to block this user and hide all related comments throughout the site?
Archinect
This is your first comment on Archinect. Your comment will be visible once approved.
Professional Design utilizing ISO Shipping Containers
Dwell Magazine, in the October 2009 issue, features a professionally designed 2 bedroom home in Houston for a professional couple utilizing ISO shipping containers as key structural elements. It was a successful enough approach that two more private residences utilizing shipping containers are now being built nearby.
This year Jure Kotnik published "Container Architecture : This book contains 6441 containers," featuring completed professionally designed projects from around the globe, including a student housing complex in Stockholm using 1026 containers, a cruise line center in Hamburg using 48 containers, a museum in Seoul using 166 containers, and a broad range of private residences using 1 - 12 containers as key elements.
The MOMA "House" show last September featured an ingenious hi-tech portable dwelling in a single container.
The New York Times ran a feature article a few weeks ago on a West Texas getaway constructed from 5 containers by the former art director of Rolling Stone.
Previous discussions on this topic here seem to have been dominated by haters of the concept and nay-sayers, but there are obviously also a number of architects and designers engaging with the possibilities of working with what is currently a very large supply of very strong and relatively inexpensive space enclosures, at a time when the cost of more conventional building materials and techniques have gone sky high.
I'm interested in hearing from anyone who is currently working in this arena, especially for private dwellings.
It is fashion, simple as that. "Cool". I don't think anyone argues with that (it is subjective, of course). Where the problems were was when people were suggesting that it would save a lot of money, which it doesn't (not to my knowledge).
So "cool" being cool, all's good. It'd take a lot more than ideas to convince me and others that this was an economical approach.
I worked on one..
The main problems we ran into were...
Some Cons...
1. Condensation management , i.e. managing water in the wall cavity
2. Conductivity. Romex works but you have to pay special attention to the panelboard and all adjacent wiring. Grounding PV is also an extra layer of concern
3. The floors are sometimes a 3/4" to 1" Pressure treated and creosote treated plywood. Perhaps a lil too toxic for some people.
4. Codes...if you plan it in a major city...you may have an extra bureaucratic layer to deal with. Of course you can use the special section of the IBC
take a look at LOTEK and Wes Jones... they're the kings of the shipping containers...
also, i have a friend that is working on a 20 home subdivision in sarasota, fl that is using shipping containers...
in nz, we've just started using shipping containers to house prisoners.
LOL, now there's a great idea!!
We used them in the design of a project for an office building in Atlanta, Georgia which was never realized. The Atlanta officials were okay with it, and we actually received a permit. The issue was that as soon as pricing came in, there was not enough savings to justify the use. Maybe it was how we used them/cut them up, but we could have done a small "regular" building more inexpensively.
Now I am in Lubbock, Texas and there is a residential/studio/gallery project where they may be used as a storage units within the design. The person I am working with spoke to the city early on, and the officials were open to the idea here as well.
All in all, I would say they have a use, but when you start cutting them up, add in the cost for skinning them to relax heat gain, etc. you can quickly lose any initial savings.
I still find them to be interesting objects which can be used, but I do not find there use in the industry innovative any longer. It also seems that justification for use in some of the projects I have seen is very suspect.
As a means of recycling, building with them may be a good thing, but there could be a better use.
fetish.
I've worked on several container building concept designs and proposals for such, so it was my job to pretend I believed in it and sell it, but I'm not convinced they are a good idea either. They do become more economical past 4 stories, but 4 stories and under they are the same as wood construction or more $$$ (for multi-family construction at least.) If the design is simple enough, you can save a lot of time though. The concept is novel, but limiting because of the 8' widths. I do think there are some legitimate applications, like emergency temporary medic stations in the jungle, which is a job we were going for, but didn't get.
agfa8x, I maybe working on said project.
Shipping containers are bullsh#t.
I do find it interesting that there is now a shipping container advertisement showing at the top of the page.
maybe disturning is a more appropriate word than interesting.
I'm all about the recycling, but theres some pretty basic problems to deal with:
- extremely unsustainable timber use in flooring in standard shipping containers (often virgin rainforest wood, or heavily chemically treated)
- the width of a container makes them difficult to use, so you have to find ways of opening them up, which lessens the advantage of a pre-sealed box.
- all that welding and steelwork isn't easy or cheap.
- have you ever hung out in a shipping container? hot and stuffy.
not that there isn't ways around these, but I don't think shipping container architecture will ever be a huge thing.
Like I said before, the haters and naysayers are plentiful. That's what Dr. Edward de Bono calls "black hat thinking," in which you just criticize what you think is wrong. If that's your bent, save your breath, I've already heard it all in previous discussions here. I'm hoping, instead, to find a few people here who are interested in having a "white hat" discussion about what is right with the concept. And maybe some creative discussions about the best ways to take advantage of the resource.
So I'll kick things off by mentioning several key points:
1. ISO Shipping containers are inherently very strong. They are designed to be lifted, fully loaded (58,000 pounds net load, plus the 8,000 pound weight of the container for a 40' unit), by sling points, and can be stacked 8 high on the deck of ship. And they're weatherproof. Anchored to concrete groundpads, a stock unit can easily withstand a storm that would demolish a mobile home or severely damage a frame construction building.
2. In some locations they have piled up in huge quantities, because of trade imbalances. In these places merely disposing of the excess has become an environmental issue.
3. In the "Reduce - Reuse -Recycle" paradigm of current environmental thinking, Reuse is superior to Recycle, because Reuse does not waste the original fabrication "costs," and does not incur additional costs to reclaim the material and refabricate a new product. So finding valid second uses for shipping containers is an environmentally sound practice.
4. Because of their transportability and inherent modularity, they can be quickly deployed for "immediate need" shelter, and structures can be incrementally expanded as required.
5. Because of the large surplus of containers, the cost of enclosing space with a permanent structure is very low compared to onsite construction of any modality. A 40' unit (320 sq ft) in most of the U.S, currently runs $8 - 16 sq ft total, sited, depending on location.
So that's a start. Given those parameters, what are valid uses of the resource?
Usually, I do criticize what I think is wrong. But I call it "no hat thinking" aka simple logic.
But to your question: all the reasons you listed above are potential benefits for, as you say, immediate need shelter. But in your earlier post you asked about private residential projects. This is a pretty wide spectrum, and at the private residential end of it, shipping containers will always be, for all the reasons others have noted, a fetish/funky alternative building type. The economics just rarely make sense.
One question I have is: is there still a shipping container manufacturing industry? Because clearly we have enough.
OpenD, you are about 15 years too late.
There are huge problems with shipping containers. to refer to LB, a new 40ft hi-cube shipping container [yes, still being built] costs approx $USD100,000 to build - in my metric thats 28.5m2 or $3500/m2.
Any model using shipping containers has to rely on old shipping containers which come from a variety of sources in a variety of states as agfa8x mentions above. Some containers have to be of a certain class to transport goods. So there maybe a heap of spare containers out there but they are effectively useless for their original purpose.
Some fall off the back of ships, and are picked up and sold to numerous factories in China and Vietnam for reuse. Most have toxic timbers for floors that needs complete and controlled removal
Structurally, they can be rigid, but once you start playing around with the frame or the walls, this vanishes. There is little or no IP involved. A monkey with a blowtorch can modify a container.
The dimensions are difficult to make work. There are alot of issues with insulation and ventilation.
My question is this, and its simple: why get involved with a business model where your methodology cannot be protected? Even the big shipping container modifiers like Verbus Systems have very limited patents that only apply to logistics rather than construction detailing.
your first post is indicative of a flawed premise; just because Dwell and other publications or institutions feature these containers hardly makes it new or newsworthy. typically media or institutions are lagging indicators of what's "in." certainly a case point; the first time i can recall shipping container[s] being used by architects, was at least 7 or 8 years ago[?] - Pugh & Scarpa and then Michael Rotondi, Jennifer Segal, and i'm sure more examples exist...
again shipping containers and modular design have become so fetishized that local architects think that PODS containers can be utilized for homeless housing. can you believe that? essentially upgraded cardboard boxes used to house homeless?
Agreed, reference Jones Partners High Sierra Cabin series from 1995.
For a slightly tongue-in-cheek take on homeless housing, has anyone recently looked at Jones Partners 'Housing for the Homeless' from 1985. The cash for clunkers program could have helped to implement this proposal.
Pugh+Scarpa's shipping container conference room is still my favorite.
Pure fetish, pure object, but very, very cool. See it in person if you can (just off the promenade in SM).
Pretty sure it is at least 10 years old.
I had a Wes Jones studio with this stuff and it was well over 10 years, so I'd guess at least 15 years ago he was pushing it, maybe more.
So again, nothing wrong with a fetishized object, but the rhetoric surrounding them has been proven ineffective.
trace, absolutely, that is my favorite. i think when it becomes the "cure all" for human needs, as a fetish object it becomes, well, shit.
it's pretty cool that the havaianas flip-flop store in brazil using a shipping container to feature their "international" collection.
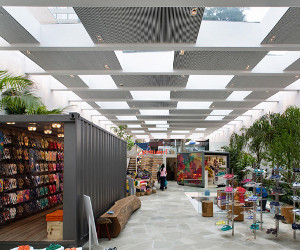
why can't more architecture be cool like that?
For those interested in digging into this a little bit, the criticisms so far mostly miss the point. I'm not saying the use of shipping containers as an architectural element is the solution to all the world's ills or even makes sense in every case. But what I am interested in exploring with others is those situations where it could make sense.
Take Hawai'i, for instance, where almost everything, building materials included, arrives in containers. And far more comes in than goes out. So there is a permanent surplus, which translates into a permanent disposal problem as well as a permanent possible resource. And in that same area, cost of living is high, cost of construction is sky high, while average income is low, and that translates into a permanent shortage of affordable, low cost housing. Conventional home ownership is simply out of reach for a very large percentage of the population.
Used good condition 20' standard containers can be purchased today in Hilo or Honolulu for under $3K, while new ones sell for about $5K. Single use (one trip only) 40' High-cubes (9'6" tall, 8' 11" inside) are about $8K, while good condition used are under $5K. At least one entrepreneur is building and selling a fully permittable 320 sq ft basic living unit on Oahu out of these 40' single use containers with bathroom and efficiency kitchen, wiring and lighting, door and three windows, drywall, insulation, and shed roof for about $25K, or $17K without drywall and roof. For some people that can make private home ownership affordable, even if it is minimalistic. And there is always the possibility of incrementally adding to the size of the home in the future.
But people's thinking about adding to a basic shelter single unit naturally gravitates toward placing a second one next to the first and attaching them. And many designs to date have followed that logic, stacking multiple containers side by side or on top of each other like Legos. What I really like about Christopher Robertson's Houston design is that he took the concept to another level by placing two 40' containers about 20' apart, bridging the space between them with a floor and roof, and enclosing the open ends. The containers serve as "really wide walls" as he puts it, with a large great room surrounded by bedrooms, bath, etc. in the "wall space." It's a very flexible concept. And it even holds the possibility of being built incrementally, with a basic "starter" unit eventually morphing over the years into a full sized family dwelling.
To me that is an idea worth exploring.
knock yourself out.
yup, go for it if you want, but make sure you look up all the precedents we all mentioned. Jones and others were using modules, stacking, putting walls between, etc., 15+ years ago (and look how far they got!).
Just like prefab, there are great applications, but for general cost savings they don't cut it.
ff33º, comments duly noted, with my questions:
1. Condensation management , i.e. managing water in the wall cavity - OpenD: what do you think of the possibility of using foam-in-place insulation between the corrugated steel wall and drywall? Polyurethane foam is non-absorbant, non-flammable, an excellent insulator, and essentially non-degradable except by UV exposure.
2. Conductivity. Romex works but you have to pay special attention to the panelboard and all adjacent wiring. Grounding PV is also an extra layer of concern - OpenD: check
3. The floors are sometimes a 3/4" to 1" Pressure treated and creosote treated plywood. Perhaps a lil too toxic for some people. - Open D: on the wet side of the Big Island of Hawai'i (Hilo side) this might be an advantage, due to the high incidence of termite infestation. Wood used within 12" of the ground is required to be pressure treated anyway. One approach I've seen used is to lay up a ceramic tile floor over the ply. Seems to be an effective barrier against toxic fumes in the living space. Comments? Ideas?
4. Codes...if you plan it in a major city...you may have an extra bureaucratic layer to deal with. Of course you can use the special section of the IBC - OpenD: most of the land on the Big island falls under county regulation, not city. Building codes are fairly standard to US norms, but the Building Department is chronically understaffed and enforcement is, shall we say, lax. Matter of fact there are currently an estimated 1,000 non-permit homes in the Puna region alone. The county has begun to come to terms with the idea that working with unconventional construction to insure safety and health concerns are addressed, and to get these buildings on the tax roles, is a worthwhile effort. A couple of weeks ago county commissioners unanimously approved the use in Puna Dsistrict of temporary shelters like tents to be lived in for up to 2 years, off the grid, while construction covered by a permit is being undertaken. And the precedent is already established, with a number of container structures already built and occupied under approved permits.
So while the approach may be discouraged in other areas, where it is permitted, why not make use of it if the requirements are a fit? The main barrier left today is the need for for professionally drawn plans stamped by state licensed architect and engineer, but the widespread use of package home kits and package plans in the area indicates to me that the cost to an individual owner with limited resources could be made attainable with well designed, attractive standard plans.
As a side note, I find it interesting that the bulk of the alternative, environmentally sensitive design today is happening at the two extremes of the economic scale... with wealthy owners who can easily afford the high costs of cutting edge LED lighting, solar and wind power, separate greywater reclamation and blackwater systems, etc.... and with low income owner/builders who are working with salvaged materials, homemade solar water heating, rammed earth and hay bale construction and the like, simply because it's what is within their reach. Interesting.
architphil: "take a look at LOTEK and Wes Jones"
I am familiar with LOT EK, which has gotten media attention for their popular Puma City store concepts in NYC and Boston. And about 2 weeks ago they were awarded the contract to do the big Pier 57 complex in NYC. http://www.inhabitat.com/2009/08/07/lot-ek-proposes-pier-made-of-shipping-containers/
Their detached residence concepts are interesting, if limited, but their attention seems to be on larger complexes. I haven't seen their small structure concepts evolving beyond the original "swiss army knife" unfolding container, and overhanging stacked blocks approach that have been pictured on their site for quite a while.
Wes Jones? Not familiar. Any references you can point me to?
"i have a friend that is working on a 20 home subdivision in sarasota, fl that is using shipping containers..."
Interesting? Any online references you can point me to? I'm particulary interested in gathering more information on actual experience vs concepts.
architphil: I'm familiar with Jones Partners: Architecture's work, yes, just drew a momentary blank at his name.
Thanks
Okay, I'll bite...
There are several reasons as to why shipping containers are not an exceptionally great idea. Notice that I said "exceptionally great" and not just bad.
Shipping containers are considerably pricey-- when you compare them to the at-cost price of manufactured homes and trailers:
* A FEMA trailer-- sans overhead costs-- runs between 13,500 and 15,500 dollars.
* A single-wide mobile home at-cost runs about 8,000 to 15,000 dollars.
* A "manufactured home" is ball park 12,000 to 21,000 dollars.
Remember, these are at-cost prices out-the-factor-door. If you add research and development along with delivery, it adds some expense onto the cost.
If you were to build houses at a similar size minus the costs of architectural services, permitting, land et cetera... you could build more-than-affordable "real" houses for $50 a square foot with a high level of finish. Obviously this would require government intervention but if the goal is providing shelter... private business has no business in this discussion. Get the government to subsidize concrete and that figure plummets even further.
Now to the weight part, a "dry weight" shipping container weighs about the same as a finished mobile home at a similar size. I think a 70' single wide weighs about 26,000 lbs-- 370 pounds be linear foot or 25 lbs per square foot. So a 40-foot single wide would weigh about 14,800 pounds.
Hawaii's roads are not as weight-rated as roads on the mainland. Any planner would scorn a project for just this reason... with similar weights, they will both equally damage a road. However... with shipping containers, you'll not only have the weight of the container but the weight of the concrete, finishing materials and so on. So, there is a hidden cost here. If moving them completely finished as units, one must factor in whether the roads are rated to handle that enormous weight.
Essentially weight will be a limiting factor. Standard construction can usually mitigate this with smaller and more divided loads.
I have no particular issues with conductivity. The only issue I might possible bring up is radio interference. Since the entire structure is made of ferous metals, I'd be mildly worried that the close contact of electrical wiring and steel would produce radio noise and possible interactions with cellular, wifi and tv signals. I don't see this as problematic but there's a possibility of feedback interference (hissing and whining) that might be amplified by operating plasma tvs or devices that emit microwave radiation.
I did a quick search but found little-to-nothing saying one way or another since there's very little precendent of people living in solid steel structures.
The pressure treated lumber is dead on. If I a remember correctly, most food in hawaii is shipped by plane. So I'm not entirely what the availablity of finding foodsafe (which would automatically inhabitable) shipping containers. The other problem with shipping containers is the paint. Most industrial and high-performance paints are incredibly toxic from the paint itself to the pigments in the paint-- technically, most pigments are not chemically inert either.
So, to prevent your property being deemed condemned or brownfielded... all containers would have to be completely stripped and repainted. You'll have to pay quite a hefty amount to have the paint chips and dust removed and disposed of by full plasma valorization-- i.e., super expensive.
On to the moisture, I do not currently know enough on this subject. However, weatherproof containers are air tight which presents a different health problem and a structural problem especially in dealing with a "reactive" material like the metal used in shipping containers. The metal in shipping containers is not purposely designed for high amounts of chemical exposure-- i.e., why they are often "single-use."
While a common concern of indoor air pollution, the use of many different types of household chemicals release caustic gases (chlorides [chlorine gas and choloroform], ammonia, dioxins, various oxides et cetera) that may over time severly damage an all steel nearly airtight enclosure.
In addition to that, this presents unique fire hazards as well which may not be fully understood. That brings me to your other point, untreated polyurethane foam is highly flammable once it begins to burn. On top of that, burning polyurethane foam releases hydrogen cyanide. I'm not sure about you but I'd rather not be inside of a steel box filling up with cyanide gas.
---
Lastly, like any major tourist destination, the housing price scheme of Hawaii is really messed up... almost bordering on locational discrimination.
The tourism industry relies on armies of low-wage workers but no one on vacation really wants to see that reality. Businesses will often force a "suburbanization" of these workers to places where incidental contact is more than likely not possible. The tricky part with Hawaii that makes it particular is the limited amount of land. Almost all land in Hawaii is valuable and the working poor can't compete with the monied higher-paid individuals who want the "authentic" Hawaiian experience or the vast amounts of rental vacation homes.
So, where do you put the poor when everyone wants to be everywhere? The problem with a place like Hawaii (and it is really no different than Florida or Jamaica or any other place) is that people need to face the reality that poverty is an inherent part of their business plan and need to be inclusive instead of exclusive.
These are all things that would concern me as a planner versus traditional construction or traditional modular homes.
Very interesting points, Orochi, especially the bit about locating the poor people away from where the rich people want to vacation.
I'm still feeling like the bigger question isn't "What should we do with all these containers?" but rather "Why do we have so many of these containers?" If they can't be reused after one use then that's a completely unsustainable industry, right? It's taking a disposable attitude towards an enormous use of material.
It seems both Orochi and I are proposing that vis a vis wage discrepancies and surplus materials people are coming up with a plausible solution, but it's only because they are asking the wrong questions.
Granted, alternative projects (like Project Pink, or the Manhattan Airport proposal) are very often a great way to start a discussion of a real problem.
Orochi, thanks for playing. You haven't quite got the hang of "white hat" thinking, but I appreciate the input.
"White hat" thinking, to take another stab at explaining it, is where you set negative criticism aside and consider only the positive aspects of something. It's not the only way one should look at something, but as a phase in planning, it is a way to get beyond our cultural bias in the Western World for black hat "whats wrong with it" thinking to dominate all else. One of the factors that is credited for the phenomenal industrial growth of post-war Japan is that they have a very different cultural bias. It's considered rude to attack another's ideas.
I've simplified the case, but in short, Japanese designers and engineers come at the design process very differently than Westerners. They tend to elevate ideas as long as they have support, whereas in the west we are more prone to shooting down ideas until only one is left standing. I find the first approach more conducive to creativity. When I hold "think tank" meetings I ban the word "no," and make it safe for anyone to propose anything, free of criticism. It seems to work well to spark "outside the box" thinking, which can lead to real breakthoughs.
Orochi, now I'll slip on my own black hat for a bit to consider your objections...
First, you're comparing apples to pineapples. Costs of construction are much higher in Hawai'i, so $50 sq ft is not a realistic comparison figure. And those FEMA trailers, which would blow away in a wind that wouldn't faze an ISO container, same deal. Either you'd have to ship the materials in and assemble them locally, or build them elsewhere and ship the finished units in, either of which is costly.
A big plus for reusing containers is that they are already there, in large numbers. Asking why they are there is not really germane to the question of what to do with what is already there. And they're not "single use" because they can't be used again for shipping, they're single use (when they are) because the economics of shipping empty containers back where they came from doesn't support it. Same reason you don't send a can back to Campbells for a refill after you've eaten the beans. These are just bigger cans. And my question is, what are possible valid uses for these big cans, since they can be purchased intact for salvage value prices?
Besides the old bent up rusty containers y'all seem to be thinking of, there are also virtually new unpainted containers, some made of corten steel, some of aluminum. And 20' containers can be trucked in to most places where larger ones won't go.
On the foam-in-place rigid ployurethane foam insulation question, I slipped a cog when I called it nonflammable, but neither is it highly combustible. Even without added fire retardant, it is what used to be called "self-extinguishing," and it takes sustained very high temperature to set afire. I've seen photos of a dome home in California that had an exterior of polyurethane foam with a vinyl skin, which was the only structure in its area to survive a huge wildfire. The only damage was a small area where the foam melted away under the sustained blowtorch of 100+ mph winds and 40 foot flames. It is considered safe for insulation in many uses when covered with plaster or stucco, or for crack and crevice sealing, like around pipes and vents or windows and doors. Still, toxic outgasssing under the high temperatures of a sustained fire in an enclosed space is a valid issue. Where i had originally envisioned it being of possible use is on the exterior, sandwiched between the metal corrugations and an exterior skin to provide weather insulation, where that wouldn't be a concern. .
As to the poverty issue and how it affects the housing picture in desireable vacation destinations, I couldn't agree more. But while we're waiting for the big picture to be improved in some way, on the micro level there are still real people in need of real housing today. Container based housing may not be THE solution, but it's possible it could be A solution for some. And that's a question I'm interested in wrestling with.
OK, black hat off, white hat ON.
For anyone interested in learning more about ployurethane foam insulation, there's a useful book by David B South called "Urethane Foam: Magic Material - and the Best Kept insulation Secret!" It's been out of print for a while, so he put it online as a free download at htttp://www.monolithic.com/stories/foam-chapter-00 Now the book is back in print, but the free content is still online at the moment.
Despite the hokey title, it's actually a practical reference. Drawing on a long career in the polyurethane foam business (at the peak his foam company was applying over a million pounds of foam insulation per year) and his later work with thin-shell ferrocement domes, which use polyurethane foam both as a mold form for sprayed concrete and as an exterior insulation material, he tells it like it is, and like it isn't.
In Chapter 5, on Foam and Fire, he strongly cautions against using unprotected polyurethane foam as interior insulation, but follows with:
Urethane foam is an excellent fire barrier when used on the exterior of a building. There are numerous examples of urethane foam roofs saving a building from fire. Burning brands * and debris can lay on a urethane roof for a considerable time before burning through. The urethane insulated roof will simply char. If there is no external heat source, the fire will go out. It requires a lot of heat to keep urethane foam burning. Where heat can radiate into the atmosphere, urethane makes a superior fire barrier.
We have a gentleman in Fort Worth working to develop shipping containers as transitional housing for our homeless population. He has received a fair amount of media attention and has been battling it out with city council for over a year.
I have met with him several times now and we are pushing to engage the design community, lead by our local Architecture for Humanity chapter, in the design process of future units.
He currently has a one-unit residence constructed on an industrial site, the final hurdle being the acquisition of city land. According to him, he purchases the 8' x 48' units out of Houston for around $2700 and can finish them out at a per unit cost of between $12-15K. As I understand it, the key cost component is the final leg of transportation; that is, getting the unit off the train and onto your site.
I believe this low-end, residential application to be the only economically viable architectural solution to the growing surplus of container units.
http://aplacetosleep.org/index.html
http://www.aplacetosleep.org/slideshow2/index.htm
ryanj, thanks for the information.
One of the interesting things about his approach is that for what I call Tier 1 housing (the homeless), he has the wisdom to redefine "home" as "a safe place to sleep," and to address that need directly.
It's hard for a lot of people who do have homes to get past the fact that Tier 1 housing doesn't satisfy THEIR OWN needs, but it's a worthwhile improvement nevertheless for those who have been sleeping in cardboard boxes, or under tarps or bridges. And I think it is a key distinction to make in trying to find solutions to the homeless issue. As Abraham Maslow pointed out in his "Hierarchy of Needs," until the most basic needs for food, water, and a safe place to sleep are met, higher needs are not motivators.
"I believe this low-end, residential application to be the only economically viable architectural solution to the growing surplus of container units."
I see the man in Ft. Worth is already planning to use containers in his approach to "Tier 2" housing as well, as a step up from Tier 1 into fully equipped small low end dwellings. This will be more difficult to achieve, but again, I think it is a worthwhile ambition, and one containers could play a part in.
Agreed. Given the Tier 1 approach, a redefinition of "value claims" is key to public appeal (and political appeasement). Maslow's hierarchy of needs is an interesting interjection, however I believe a multi-leveled approach is necessary in light of the negatively-skewed perception of shipping containers as dwelling units. In other words, one must appeal to not only physical needs, but also factors which influence the interdependency of physiological and emotional needs as well.
I believe these "value claims" must supercede any performance or aesthetic claims from an architectural perspective. At Tier 1, housing is not just a tectonic artifact for dwelling, but a symbol of dignity and stability, than architectural "honesty" and "transparency" et. al. can come. Having a place to sleep possesses an inherent dignity. This seems to be the central claim to his effort.
Interesting comments...it makes me think of Kahn's anecdote about the brick..."what does a shipping container want to be?"
Black hat off, Red hat on.
Another potential point of contention with shipping containers and their use of housing is the sacrere of our [Western] own culture.
What kind of society do we live in where consumerism runs so rampant that we are now resorting to the idea of living within the boxes of the products that we use to decorate our houses?
Something is amiss here-- especially the idea of housing our discarded population in the boxes that house boxes. That notion lacks any sort of sanctity we have in our own belief of universal human rights. It sends the message to the people we are trying to help that we are trying to put our human "trash" into the "trash" that more or less is a major factor in them becoming human "trash" in the first place.
Is this really where our society should go? Should we all resort to living in the boxes of boxes? Should we treat everything as disposable and recyclable?
I do not necessarily feel that there is any dignity in this marginalization of marginals.
Red hat off, Blue hat on.
Detachment from the subject and the object is necessary. The judgment and idea most of us are making is that home is box with four sides, one door and two windows that sits on a piece of land.
Home has many meanings. A home is not just a house. When planners, researchers and architects approach subjects like this, they often always apply what their life from their point of view is.
Home ownership and its benefits are often a fantasy of the middle class. They believe strongly in the idea that ownership infers some sort of glorious benefit whether it be personal freedom, personal expression or monetary gain.
However, this persuasion is often of ethos or pathos. It rarely is rooted in logos. Ownership is not for everyone nor are the benefits as spectacular as one would like to think. Renting may not necessarily be the better thing either.
The point is most homeless people and people in deep poverty often end up there for many reasons. Paranoia, disability and disenfranchisement are some of the bigger reasons. While disability requires it own special approach, the other two are blockades to projects such as this.
Essentially, many "easy routes to homeownership" projects, affordable housing projects and other schemes seem to apply the preference of the helping crowd to the needing crowd. The process is essentially is making someone else walk in your shoes without walking in their shoes first.
I think for these things to be acceptable and not doomed to failure, we have to detach ourselves from the projects. Just because someone is homeless doesn't always mean they need or want a house or shelter. And their idea of a house or a shelter is probably much different from what we percieve to be a house or a shelter.
Blue hat off, yellow hat on.
A recent study points to the fact that there is enough self storage facilities in the United States to fit everyone in the country inside of them.
Instead of repurposing shipping containers, why don't we just out law new construction of new self storage facilties unless they are made out of shipping containers? It only seems natural that a container made for storing cargo would be better suited to storage cargo.
I think it probably might be even easier to rehab self-storage facilities into apartments than it would be to rehab shipping containers into homes.
Yellow hat off, black hat on.
Most of the studies regarding the flammability of polyurethane foam have been done by the Polyurethane Foam Association.
Anyone arguing the fact that polyurethane foam isn't as flammable as advertised should really consider that a majority [or maybe large portion] of structural fires that result in death are caused by dropping cigarettes on polyurethane foam.
Flexible polyurethane foam is suppose to be less flammable than rigid foam. It is even suppose to be flame proof against smoldering fire hazards. So, explain to me why a product that is suppose to not burn has killed soo many people and destroyed soo many buildings?
I checked the research and most of the research regarding PF involves treated or self-extinguishing foam and a bulk of this research was conducted in the 1970s and the 1980s. So, my hypothesis is that the slim availability of third-party facts about the the flammability of polyurethane foam is that no one has ever extensively studied it because it was a known fact that the stuff is flammable.
Furthermore, the PFA states on their website "Flexible polyurethane foam (FPF) is an organic material and, like all organic materials, is flammable." And to add insult to injury, "High risk occupancies should consider having fire detection, fire alarm and fire suppression systems."
Why would an association that says their product is not that dangerous recommend having fire suppression systems if you use their product?
HMM.
Black hat off, white hat on.
Maslow's heirarchy of needs is an important topic. However, the most effective form of housing the homeless and poor is known as the "housing first" approach.
The approach utilizes existing housing stock and assigns individuals to a collection of properties across the given area. Unlike homeless shelter approaches and other "camp like structure," housing first is showing to have a much higher success rate and a lower total cost.
What the aim is too fully integrate these people into society, away from other homeless people and to give them responsibility. It works better because this option really assigns no identity or cultural construct to them outside of being "regular people." The only thing that is different about them is the regularly scheduled visits from social workers making sure the person is complying with the program details.
It is more expensive upfront but over the course of a year is somewhere between a 1/4th and an 1/8th of the cost of keeping these people in shetlers, jail or "communities."
White hat off, green hat on
Considering the "hierachy of energy consumption," perfectly good steel would be a waste to turn into housing. If we were to talk about this from an ecological point of view, the biggest consumers of electricity are-- from least to greatest-- concrete, glass, chlorine, rubber/tar, iron and finally steel.
So, essentially, why should recyclable steel be used when energy and emissions are right now such huge issues?
If anything, a state like Hawaii should open a steel recycling facility that operates as a non-profit to reduce costs. It could then trade containers of shredded steel casings for concrete and then use that concrete to build real, affordable, centralized and urban-ish housing for its poor and homeless population. You know, considering concrete would be a more appropriate material in a place like typhoons, high amounts of rain and a landscape that oozes sulfur from every pore.
Interested hat off, yawn hat on
Good stuff Orochi. Hats off to you.
Along with redefining what a home is, we might also redefine what ownership is. Ironically Hawai'ian native culture did not have the concept of ownership Westerners later imposed on them. All the land was seen as being for the common good, and tribal allocations were made based on need, and re-evaluated as conditions changed. The requirement for good stewardship of the resources available was a given.
In regard to the Ft. Worth Tier 1 project, ownership might be defined something like "it's yours to use as long as you want it and need it, so long as you take care of it and don't break the rules." That would not work for everyone, and some wouldn't even be interested, as you said, but for some it would be a step up that could make a huge difference. And for Tier 2 projects I can see a co-housing approach being a possibility, on publically owned land, with individual units having basic facilities plus access to shared facilities.
"Housing first" is a great approach if you have existing surplus housing stock to work with. But in some places, as diverse as Hilo and NYC, you just don't have that resource.
Recycling the steel from the containers in situ has possibilities, but if it were that simple i think it would already be done, which it largely isn't. For Hawai'i I think the the key obstacles to overcome would be the lack of required infrastructure and very high energy costs. Ironically the use of steel frames in mid range house construction there is trending up, despite rising material costs, as stick-built wood construction costs climb out of sight. Steel has proven to be a very good material to work with in the area, especially given the seismic activity and hurricane risk, not to mention widespread termite problems, so long as you take easy and appropriate steps to remediate the environmental factors you mentioned like rain and volcanic sulfur in the air, where it occurs.
Regarding rigid polyurethane foam, it's not the same stuff as soft polyurethane pillows and upholstery, so you really can't compare them in any meaningful way. I've experimented with one of David South's key assertions myself, holding a well cured chunk of rigid polyurethane insulating foam in one hand, while applying a blowtorch flame to it with the other. As long as you hold the torch flame steady on the foam it will oblate, and as long as there is no wind you can eventually work up a little lick of flame. But take the torch away and the flame dies immediately. Meanwhile the back of the foam stays cool. It is this extremely low thermal transfer that makes it, in South's words, a better fire barrier than concrete.
I love your idea about mandating the use of containers for self-storage facilities. The big name facilities I've seen are typically built very much like a complex of shipping containers, but of much flimsier material. You really have to wonder why. And the reuse of containers for larger structures like apartment complexes and hotels and offices is already happening at a rate you can't ignore... almost everywhere except the US. You really have to look to other countries for the best examples of what is possible when considering "what does a shipping container want to be?"
We met with the owner last night and are moving forward with a collaborative design work session with architecture for humanity, client, city officials, financiers and a possible jury. Will keep you posted!
it's like stepping into a set...


lot/ek's organizations of the containers tend to be more compelling since they take advantage of creating spaces between the containers...
Good luck with it ryanj
You might also take at look at what this guy in Oahu is doing. He's got an approach to a portable single container, 320 sq ft studio with a bathroom and kitchenette that meets legal standards for the area, has made it through the building permit process and has been sited.
On another page he's got a 4 container 1420 sq ft house that he says the State officials love, and are in discussion about building a couple for their use.
What he needs, obviously, is a good architect to take these to the next level of design, but his basic concepts are also obviously workable, because he's gotten 5 structures built already.
http://www.affordableportablehousing.com/
I have some questions if anyone can help.I am working on my thesis which is about these shipping containers being used for homes, etc.
When are shipping containers no longer useful in the shipping industry? Is it at this point they are useful for the building industry?
most shipping containers - or at least a large portion - are only used once. this is because of trade imbalances. most countries are either goods importers or exporters. not many import and export equally. large consumers like the usa consequently have a lot of surplus containers.
Hi Michellem
It very much depends on the market. In the Hawai'i case I'm looking into, many containers are surplus after a single trip because of the large imbalance between what is shipped in, versus what is shipped out. Surprisingly, you can even buy new locally made containers in Hawai'i, as you can elsewhere in the United States, because some shippers insist on using only pristine new containers. A few homebuilders wanting the best quality, even at higher cost, have been known to buy new ones for that reason.
More typically, in most American port cities, like Houston, there are a wide range available for purchase, from scrap metal grade to like new, with many having had enough use to require small repairs before reuse for shipping, like patching the floor or welding a hinge. The more use they've had the more beat up they are, and the lower the price. The cheaper ones are popular for use as small steel buildings for storage, workshops, hunting cabins and the like. The better, newer ones are in some demand now for architectural use.
If you want to research the lifecycle on containers before they are resold, each ISO standard container has a metal data plate on the end that gives the date of manufacture, original owner and other information. From that you might estimate possible use, factoring in load time, transit time, unload time, and lull time before trunaround. You can also check the auction sites where containers are sold, like eBay and the shipping industry specialized sites, where some sellers list manufacturing date and condition in the details of their offerings.
In the Hilo area, you can currently purchase a single use 40' container and have it delivered to your lot for under $5K total. That's less than $16 per sq ft ft for a strong, weatherproof enclosure that only takes a day to site, compared to $50 - 75 per sq ft for materials alone for kit house that will take a month or more to make weathertight. Plain vanilla very basic prefabs run maybe $125 sq ft. It's easy to see why some people are choosing to go the container route on owner-built projects, where they put a couple of containers down, add simple shed roof, and work on upgrades as they go. It's thought there may be as many as 1,000 of these already in use in the Puna and Ka'u districts.
My own biggest interest is in moderate to mid-range contemporary style residences, where the expectations for fit and finish are higher, but where there is a tremendous squeeze right now on the buyers needing housing. As I said earlier in the thread, i don't see this as a panacea for the world's ills, but as one possible approach, that when intelligently used might provide cost savings which could make a difference for a lot of people. The Houston house I mentioned earlier has a basic concept I think is quite scalable, using containers as "side walls" and main supports for the structure, then enclosing the space between, for buildings from 360 sq ft to 3,024 sq ft and up.
Good luck with your reasearch.
Here's a quick update, in case anyone trips across this thread and wonders what conclusions i reached.
1) The single biggest go/no-go factor is transportation. Not just transportation costs, but whether or not you can even get the desired constainer to the site at all. For a specific project that I was considering a multi-container design for, the site proved to be impossible to get 40' containers into due to narrow access roads with sharp corners. For another site a mile away with better access, no problem, and the design is viable there.
2) A single module has challenging dimensions to work with for residential use, but this can be remediated by using 2 or more containers side by side, or augmenting the 8' side to side dimension with additional construction. Spacing two parallel containers a distance from from each other and enclosing the central space is a flexible and inexpensive approach with many possible applications.
3) If you simply treat containers as another material resource, there are valid uses to me made of them. Just don't force the issue if it isn't a good fit. In the project which is moving forward, a 20' container, loaded with building supplies and tools will be shipped to the site, and used to secure them while the main building is constructed. Then it will be incorporated into the final structure to house utilities, laundry, pantry, and storage, and serve as support for a deck extension from the second floor. Although there will be some expense to add siding, it is literally a "bonus" room for the building, better than free, because otherwise it would cost money to haul it away at project completion.
Best of luck,
OpenD
Block this user
Are you sure you want to block this user and hide all related comments throughout the site?
Archinect
This is your first comment on Archinect. Your comment will be visible once approved.