"And one last picture. It's a nice 3D job that we've milled. A plano-concave hacked gadgets logo thingy. It is drawn in 3D in ProEngineer Wildfire 3 and the CAM (computer aided manufactoring) job has been made in ProE as well. It's not much bigger than a matchbox, so the quality of the parts we can produce on the mill is very good!"
The thing with this paralell port device are, that it is easy to write a post processor ,that mill down a 3D drawing into G Codes.
------ But some time in the 90' I borrowed a small 3 axis from Roland ,for one of my first projects ; that also was driven by paralell port and as the drivers and software was not to borrow ,I had to write a small application that "looked" at a 3D drawing and calculated a reasonable set of data to feed the 3 axis routing . Now just one small problem that had to be solved, was that you can't just route the cutter with no thought about how the raw block is , you can't just "force" the router bit strait into the block with no thought about how much material that mean removing.
Being an xyz router the solution became to let the router in a number of steps , route the intire object nomatter if there was material to route all places. by doing it from the maximum z and down to the minimum z in a number of steps ,it was possible to let the router only route a layer of 3 mm. at each time ---- would you think that to be a problem ,well it showed to be but solved easy as described. still first time it worked ,the router in a strait vector ,returned thru the block from end point to start point, destroying the intire routed piece, try and error.
"i want to get a mill soon..... i was looking at a small shop bot type..... whats your smallest bit that you were using?
b"
These things work as any routing, there are an ideal feed speed that is calculated from the cutting piece diameter and from what the feed rate for the particular material ------ you will find that some have this build into the software and some has not ,but you soon wear out a bit if the motopn are to slow and the spindle to fast --- that's the same in woods or metal working and there are easy tables for that, to set the feed speed for a particular spindle speed and tool diameter.
I think 3 mm. is about the smallest you would use any smaller would ask very high speed motor and the heat from the cutting is easier let away the bigger the bit.
Jul 18, 07 10:38 am ·
·
Block this user
Are you sure you want to block this user and hide all related comments throughout the site?
Archinect
This is your first comment on Archinect. Your comment will be visible once approved.
volunteerlabrat.com
The Video will take some time to load -- I suggest you turn speakers on to enjoy the nice music.
http://www.volunteerlabrat.com/images/cnc-timelapse.mov
It's a 3 axis router project ,
http://www.volunteerlabrat.com/default.html?goto=cnc.html
About the crew , look close at "about us".
http://www.ackw.dk/
is that you with the mohawk mullet vindpust?
well, that explains a lot...
I particular like this text:
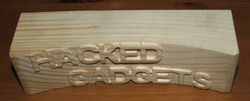
"And one last picture. It's a nice 3D job that we've milled. A plano-concave hacked gadgets logo thingy. It is drawn in 3D in ProEngineer Wildfire 3 and the CAM (computer aided manufactoring) job has been made in ProE as well. It's not much bigger than a matchbox, so the quality of the parts we can produce on the mill is very good!"
The thing with this paralell port device are, that it is easy to write a post processor ,that mill down a 3D drawing into G Codes.
http://www.volunteerlabrat.com/images/cnc_innovus_final.mov
i want to get a mill soon..... i was looking at a small shop bot type..... whats your smallest bit that you were using?
b
did you invent the cnc mill?
As you recall my name is not "CNC".
------ But some time in the 90' I borrowed a small 3 axis from Roland ,for one of my first projects ; that also was driven by paralell port and as the drivers and software was not to borrow ,I had to write a small application that "looked" at a 3D drawing and calculated a reasonable set of data to feed the 3 axis routing . Now just one small problem that had to be solved, was that you can't just route the cutter with no thought about how the raw block is , you can't just "force" the router bit strait into the block with no thought about how much material that mean removing.
Being an xyz router the solution became to let the router in a number of steps , route the intire object nomatter if there was material to route all places. by doing it from the maximum z and down to the minimum z in a number of steps ,it was possible to let the router only route a layer of 3 mm. at each time ---- would you think that to be a problem ,well it showed to be but solved easy as described. still first time it worked ,the router in a strait vector ,returned thru the block from end point to start point, destroying the intire routed piece, try and error.
"i want to get a mill soon..... i was looking at a small shop bot type..... whats your smallest bit that you were using?
b"
These things work as any routing, there are an ideal feed speed that is calculated from the cutting piece diameter and from what the feed rate for the particular material ------ you will find that some have this build into the software and some has not ,but you soon wear out a bit if the motopn are to slow and the spindle to fast --- that's the same in woods or metal working and there are easy tables for that, to set the feed speed for a particular spindle speed and tool diameter.
I think 3 mm. is about the smallest you would use any smaller would ask very high speed motor and the heat from the cutting is easier let away the bigger the bit.
Block this user
Are you sure you want to block this user and hide all related comments throughout the site?
Archinect
This is your first comment on Archinect. Your comment will be visible once approved.