I have a terrible habit of not keeping any single sketch for anything. Sort of odd because I kept every scrap of paper I ever sketched on from school... but now that I'm paid to do them, I toss them away. Perhaps I should make an effort as a post-covid resolution?
At least scan them before tossing them so you can contribute them. This will be something that I'm willing to contribute to at some point. It might not be direct client projects work but something I'll look forward to doing and contributing. Not this week at this time but soon. Can they be conceptual sketches or technical drawings (DD/CD level). Maybe a little of both might work especially if one explores ideas. Anyway, thanks Wood Guy for establishing this thread.
Let's start off with roof details. I'm thinking overhangs and parapets, but whatever floats your boat, presented as photos, sketches or construction drawings.
I designed two carriage houses to go with this house, which is being condo-ized. I wish they could keep it as a single family but it's quite large. Fun sidebar: I didn't measure the house, all dimensions were done using SketchUp's photomatch feature. I checked the important dimensions and they were within close tolerances.
You might want to reinforce that soffit upper ledger with thru-bolts to the wall framing. Depending on the brackets alone is an invitation to trouble. Don't ask me how I know.
Miles, good point. The owner is a former carpenter and a friend, so we talked about exactly that detail, and adding hardware to keep the rafter connected to the ledger.
Bench, it is somewhat similar, though King's is Italianate, an earlier Victorian-era style, while this is Second Empire (sometimes called Mansard style), which became popular after Paris was "renovated."
Non, it's been a couple of years since I was up there and I didn't climb the ladder to the tower. It does look like a guardrail but I don't remember seeing a roof hatch.
I'm in Grand Junction, CO. The average snowfall is under 2" so I'm not worried. Spandrel glass was used because the elevated pedestal floor is behind it. The owner wanted the rooftop deck to be open with no glass.
Oh, just to be clear. The sheathing and studs shown in the construction image is only a temporary enclosure while waiting for the curtainwall to arrive. The curtainwall dose continue all around the center volume - it's just in a hard shadow in the progress pic.
I'll post a continuous vertical to horizontal parapet detail we've been working on for a few years. We have several versions of it across many projects with the same client and so far the results have been very positive. Took a lot of coordination with the buildings at first but it works well. Detail drawings are from another location than what is shown on the picture but it's similar enough.
and the dirty details. I kept the text on. We also did many detailed SketchUp models showing membrane laps and trim/flashing connections but I can't find any now. Originally designed and documented in CAD, current version heading to construction later this summer is in Revit. The detail sheets for this is a small project in itself.
and if anyone is curious, the picture above is the finished product and not a bad 3D rendering with all the lights off. Pic was taken in winter hence the gloomy look. I cropped out all the snow.
Thanks WG. we carefully coordinate with the steel fabrication and make sure to dimension the bolt spacing too. I'm currently working on a version that's over 100' long. I have another where the bent-plate C is 2'-6" high.
The underside of the canopy is a single plane through the storefront that becomes the underside of a stair landing in the entry atrium. The new structure utilizes holes in the exterior wall from an old canopy. Threading a needle through existing openings at multiple levels. I learned so much here.
With how tight that roof drain piping goes you might end up having to switch to the side outlet drain type, this keeps coming up in projects I've been working on. Otherwise I like. Looks kinda like my drafting.
we're doing master-spec notation finally, was happy to be the guinea pig for those... Still get a lot of "how did you guys coordinate all those spec sections" type questions though... it's been interesting how adding something simple shines a light on who knows their stuff and who doesn't
Jul 19, 21 8:40 am ·
·
tduds
I have to write (well, "Write", ya know) two specs this week. Small projects, but still...
Good for you guys. Mean While, I got an RFI from the contractor asking to use a different brick tie due to supply issues. And the GC is asking for extra money to cover the cost and blaming it all on Covid. These god damn public bid contractors. New low, man, new low. They even dare to ask. Recently, they also asked for extra cost associated with 10 extra feet of drainage pipe on a $50+M project. The paper work costs more than the pipe.
I'm getting the same nickel & dimes mentality here too. I've got 2 quotes for 2 areas where we needed to extend gypsum board to match a window jamb, or cover a pipe... literally a few inches of material. It's cheaper for the client to just approve it than it is to charge them for my time to review and chase alternative quotes...
Worst part is I know this GC is trying to build up RFI/change order numbers to use as a defense when they are behind schedule. Building ammunitions in case of lawsuits. Their lawyer by trade partner has been quite involved lately. The government client scared of delay and legal entanglement will probably cave and negotiate a pay out. Tax payers money. Games played over and over.
Jay - keep in mind that unless the GC can show and documented how the RFI's / Change Orders impacted the schedule then they are out of luck. It still sucks that you're having to deal with this. :(
this is a house that took 4 years from SD to final, a hellish site, bad soils, foundations heave, bad steel contractors, several design changes, family driven interior design....I'm glad it's finished and the owners are happy.
yes, but do they have a climatized custom wine cabinet or a peninsula fireplace with no visible flue? or 15 different types of marble, quartz and granite slabs?
I recently did a project where the majority of the construction was 350/sqft.... it was just unconditioned storage made of single wythe CMU on a concrete slab and a TPO roof......
going rogue, macro for contrast to details. i dig all your jobs btw. obvious pros through and through. even if you hate this, i'm always looking for feedback. it ain't your father's utopia.
Jul 16, 21 3:42 pm ·
·
tduds
My advice is to post articles as articles. I'm not going to read a youtube video.
A "Pretty Good House" addition I designed and am helping build for my mother in law. My father in law built their house in the late 1970s, off-grid for financial reasons--it's1/2 mile to the nearest pole--and had the lumber for an addition cut from their land before he passed away in late 2019.
He was a carpenter (and close friend and mentor to me) and would have built it conventionally, on a foundation, but I'm into low-carbon and high performance so it's on helical piers, with a double-framed envelope for good insulation, air-sealing and vapor control.
I tried to find a local builder but the few who were available were not interested in trying something new, so I'm leading construction activities with the help of local carpenters. As construction has progressed I've changed a few details, including using 2x10s for main rafters and moving the air/vapor control layer from the middle of the wall and roof assemblies to the interior, where it won't work as well but it will save time and money for insulation installation.
I meant to focus on the roof. The gusseted rafter system is a great way to get a decent amount of insulation up there. The original house has no roof overhang so I matched that detail, but had to add soffit vents--sometimes I like to tuck them under the shadow board as I did here.
Careful with the diagonal siding; popular in the 70's but also very much tends to flow rain down the joints into fenestrations like window and door heads and jambs. My Dad's house (he designed) had that and the jamb flashing took as much water as the head due to moisture channeled down the siding joints.
Thanks, but it's the sheathing, not the siding. I'm a huge nerd about control layers so we'll have a well-detailed WRB and a robust rain screen. Good tip though. A couple of years ago I renovated a 1970s passive solar house with diagonal siding directing water directly onto a door I replaced. Earlier this year they tried to blame me for water infiltration. I reminded them how I strongly recommended redoing the siding and adding a roof overhang, and told them that the door would leak in some conditions if they chose to ignore my recommendations.
I was told by a structural engineer that they will only last 20-25 years and that's if they are galvanized. Ungalvanized will only last 15 years. I am assuming this is due to alkaline soil in our area (Colorado).
What has your experience been with the longevity of helical piers in your area?
Jul 20, 21 2:32 pm ·
·
Non Sequitur
WG, it's not everyday that you see a project with better-looking sheathing than most other building's cladding.
Chad, I've only been using them for a few years, and I was nervous the first time--a new house directly on the coast, in 2014. Salt air is notorious for eating steel. (I was an employee and not the decision-maker, though I made sure the client knew my concerns.) We talked with the home office and they were confident that we would get at least 50 years out of them. They're hot-dip galvanized but I believe there was an option to upgrade to stainless steel.
With my focus on climate change, I'm pretty sure that in 50 years we'll have bigger issues to deal with than worrying about whether the piers need to be redone, and using piers may help put that day off by a few seconds...
In my area, I would almost always go with stainless steel if it was my choice and not get some cheap-ass contractor changing what is specified. The reason, if it is exposed to moisture (and there is a LOT of it), I would go with stainless steel. Some other materials, like some alloys, where it will have strength as well as resistance to rust or corrosion, then I would consider them. Galvanized anything (hot-dipped is better than not) or zinc-coated anything is garbage and will not last long without corroding. This comes from experience with fasteners. The material will need to be inherently resistant to rusting and corrosion. Non-structural materials, I may consider aluminum.
Where we are, you are basically going to build houses kind of like you would build ships. (Well.... kind of but the idea inferred is being that boats and ships are exposed to moisture and you want to make sure water doesn't compromise the ship. Same idea.)
SneakyPete, yes, technically all stainless steel will rust over time. The question is, will it rust into rust powder in 15-25 years or will it last 150-250+ years? There are other potential alloys of metals that I may consider but yes, it's "fucking" expensive but it's cheaper than rebuilding your structure every 10 years because it is good for only 15 years, you might as well not design it in the first place let alone build it. Right. When it comes to structure and foundations, that is where the money better be in and not skimped on.
First, I am not interested in designing shit that won't last. Sure, financial considerations would need to be factored in. I didn't say I would necessarily use helical piers. There may be less expensive alternatives that won't compromise my standards where the foundation will last centuries if properly designed. I won't skimp on foundation and structure to build shit that won't last even two decades.
Clients can be bitching moaning and groaning asshats whining about how much it costs because if they only see themselves living there for 5-10 years. If that is how long they only plan to live at a place, they don't belong being property owners in the first place. They should be renters, in that case.
Having a custom home built is a once-in-a-lifetime opportunity for most people who will ever is able to get the financial resources to build one at all. Most people will never be able to afford to have a custom home designed for them.... ever.
It's unrealistic in the United States where only 10% of the population may ever be able to have the money for a custom home designed & built for them. The rest of them are renters and buyers of used homes (like used cars.... homes that had prior owners). Got it.
If a house is going to be built, it needs to last centuries (although some components like roofing, sheathing, etc. might need to be periodically replaced over the life cycle of the structural system and foundation because when the structural or foundation fails, it is the end of life of that building (in other words, its demolished if it can't be properly repaired). Sure, at that point, either a new home or building is built or reconstruction of what was once there, now demolished,... would be built.
Jul 20, 21 11:19 pm ·
·
rcz1001
Sorry Wood Guy, I didn't mean this to be some dick fight. You have an interesting design and I am not inherently against helical piers. The conditions of the ground geology matter and whether the soil is going to corrode the helical piers/piles too quickly or not is something to consider. I'm looking at the design of structures where the foundation system is perhaps the most important part of a structure that needs to be done right but it's all part of the holistic process of the designing of the structure. The primary structural system is crucial but as with anything carrying load. If it is not done right or if it fails because it has such a short life cycle that is unrealistic for a structure that is intended to have some permanence then yes, it's absolutely important that they last a respectable duration.
Jul 20, 21 11:26 pm ·
·
rcz1001
SneakyPete, if a prospective client wants garbage buildings that will collapse in 15-25 years then I'll send them your way.
Jul 20, 21 11:28 pm ·
·
Wood Guy
The brand I use is Techno Metal Post, and another brand available locally is Goliath. Neither offers stainless steel as a stock option but the TMP rep said they sometimes have them made. A google search shows that they are available elsewhere.
Of course different grades of stainless steel are good for different things. All will eventually corrode but at slower rates than plain steel. With any type of steel in the ground, you can set up an anode array--sacrificial posts--around the piece you want to protect.
While I would like for my buildings to last hundreds of years, I would also like for our planet to be habitable that long, and part of that means thinking critically about the materials we use. I have done a lot of renovations and have rarely seen a concrete pier that was not broken and deteriorating. TMP offers a 25-year warranty and Goliath offers a 30-year warranty.
Assuming moderately corrosive soil and a slightly low pH of 6.0, which is roughly what we have where I am, and using 3mm steel for the posts, this study shows that the piers should last around 100 years: https://helicalpileworld.com/Dealing_with_Corrosion_-_Kevin_Davies.pdf. (P. 17 of the PDF.)
If you don't want to use them, don't use them, IDGAF. I like them and will continue to use them whenever they are a good solution. Just this morning a contractor building a $180k screened porch addition asked if he could switch my concrete piers to TMPs, and a few days ago a structural engineer for another addition asked if she could do the same.
We used diagonal board sheathing for a few reasons: it's what my FIL had planned to do, and did on his garage I designed and helped him build 25+ years ago. The material was cut on site, which you can't say for any sheet goods. Solid wood holds up much better than OSB or plywood to repeated wetting, which happens to every house in a cold climate that doesn't have a thick layer of exterior insulation. You can burn the offcuts as kindling, an important consideration in an off-grid house heated entirely with wood (and sun).
I assumed that in your area the helical piers lasted longer than here. I also assumed that they are a completely suitable for you project types.
I've had about a dozen structural engineers out of Denver inform me that they wouldn't use helical / spiral piers / piles for our soil due to the short lifespan. Keep in mind we're doing a lot of public projects were the building will have a lifecycle of 50-100 years.
Chad, according to the table I shared, they should last much longer in alkaline soils than in the acidic soils they have here. But I know that engineers tend to be conservative, and I have worked with some who won't use helical piers because they can't see the soil they are going into.
Jul 21, 21 3:16 pm ·
·
rcz1001
Thanks for the info, Wood Guy. Where I am, things are actually quite wet (other than the unusually warm summer we have been having this year) and the idea is to determine if the product will be suitable for long-term use at the project location. One thing you can do is employ redundancy in the foundation so if some fail, it isn't a complete and sudden catastrophic failure but it's not clear if that would be viable in your particular project. I do agree with you about wanting the planet to be habitable for hundreds of years. Part of the solution is building buildings to last longer not like the trend we have been doing in more recent years because new construction contributes more to carbon footprint than work on existing buildings. Every time you have to demolish and rebuild is a big impact. So if I can design a building that lasts 5 times longer than it may be lasting with how some of the construction these days are.... it would save in carbon emissions over the same period of time. There is a lot to consider and nothing I said above is meant at all as criticism of you.
Wood Guy - I don't know what to tell you. The engineers we know that have studied this basically told us that the tables from the manufacturer were bunk. They could be wrong but we trust them and it doesn't make sense to doubt them.
I know someone who almost dies sniffing white out in 7th grade. He survived only to be arrested a few years later for accidentally starting a fire with a bag of flaming dog shit.
Jul 20, 21 8:32 pm ·
·
atelier nobody
Many, many years ago, we were trying to mount some renderings to foam core with spray adhesive, but the nozzle was clogged.
In the process of trying to unclog the sprayer, I managed to give myself a good blast right in the face, to which I laughingly responded, "Well, this reminds me of middle school."
My coworkers both gave me this strange look - they honestly didn't know what I was talking about. Sigh, kids these days... (For the record, I did not actually sniff glue in middle school, but I knew folks who did.)
It's been a week so let's try a new topic: concrete. What's an interesting detail you're working on that includes concrete, or what's your favorite detail from the past?
I have no interesting recent concrete detailing to show for myself, but I do have a concrete detailing story.
Very early in my career, I worked on a Fire Department training facility. Part of the facility was a building designed to approximate a 2-storey SFR, but constructed entirely of CIP concrete so it could be repeatedly torched and the firefighters could practice running into the burning house to save the baby. The interesting detailing part was that there were gas lines and jets cast into the concrete, so we had to dimensionally locate both the gas lines and every piece of reinforcing or embedment, so they'd all fit. I wish I still had a copy of those drawings.
Now they use prefab 'training buildings' made out steel. Still use gas to provide the flames and smoke. Fire chief described it to me once as a little two story house filled with mini flamethrowers.
@ Beta - do you want to start this week's "Post your work" thread and theme with this project? I kinda liked the idea of doing a new thematic thread every week. Having it all come to this single thread means i almost missed this awesome project!
That's a very attractive quarry tile, congrats. What manufacturer are they?
I believe porcelain is generally stronger than quarry, and easier/cheaper to install based on the thicknesses. A lot of authorities require quarry in different areas of food service projects, but from what I gather it's sort of an outdated thing.
@nate - these are Argelith Tiles, fully vitrified industrial. The tile is 3/4" thick. The existing kitchen has that horrible red quarry tile. Typically when I do commercial kitchens, the two things that don't work for me, or my clients, are tile floors, and pebble finish FRP. I avoid both. This floor tile however, has me rethinking that.
Post Your Work
Inspired by archanonymous, each week we'll pick a new theme. Share what you're working on now (or recently) that fits the theme.
What is first topic?
Some ideas: stairs, concrete, flashing, roof, floors, millwork, windows, structure, lighting, color, daylight, pattern, texture, landscape, views, ???
What are we to post?
Finished projects?
Work in progress?
Conceptual Images?
Construction Details?
Specific assemblies (like what archanyonymous is suggesting)?
I think we should keep it to details or sketches and finished/ WIP images.
I have a terrible habit of not keeping any single sketch for anything. Sort of odd because I kept every scrap of paper I ever sketched on from school... but now that I'm paid to do them, I toss them away. Perhaps I should make an effort as a post-covid resolution?
At least scan them before tossing them so you can contribute them. This will be something that I'm willing to contribute to at some point. It might not be direct client projects work but something I'll look forward to doing and contributing. Not this week at this time but soon. Can they be conceptual sketches or technical drawings (DD/CD level). Maybe a little of both might work especially if one explores ideas. Anyway, thanks Wood Guy for establishing this thread.
Let's start off with roof details. I'm thinking overhangs and parapets, but whatever floats your boat, presented as photos, sketches or construction drawings.
Dumpster enclosures?
I designed two carriage houses to go with this house, which is being condo-ized. I wish they could keep it as a single family but it's quite large. Fun sidebar: I didn't measure the house, all dimensions were done using SketchUp's photomatch feature. I checked the important dimensions and they were within close tolerances.
Nice!
You might want to reinforce that soffit upper ledger with thru-bolts to the wall framing. Depending on the brackets alone is an invitation to trouble. Don't ask me how I know.
WG - this photo looks really similar to Steven King's house? Is this a common typology up your way?
is the top of that tower-thing accessible? I see a fancy guardrail.
Miles, good point. The owner is a former carpenter and a friend, so we talked about exactly that detail, and adding hardware to keep the rafter connected to the ledger.
Bench, it is somewhat similar, though King's is Italianate, an earlier Victorian-era style, while this is Second Empire (sometimes called Mansard style), which became popular after Paris was "renovated."
Non, it's been a couple of years since I was up there and I didn't climb the ladder to the tower. It does look like a guardrail but I don't remember seeing a roof hatch.
A roof shade on a past project. Some details, work in progress, and finished images. Last two images are out of order. Flame away.
Any concerns about ice/snow build up on a brise-soleil that far up? Also... why no vision glass at that corner?
I'm in Grand Junction, CO. The average snowfall is under 2" so I'm not worried. Spandrel glass was used because the elevated pedestal floor is behind it. The owner wanted the rooftop deck to be open with no glass.
Oh, just to be clear. The sheathing and studs shown in the construction image is only a temporary enclosure while waiting for the curtainwall to arrive. The curtainwall dose continue all around the center volume - it's just in a hard shadow in the progress pic.
My first Church Project, completed in 2010. This is a page from my portfolio for my RAIC application.
finish picture
I'll post a continuous vertical to horizontal parapet detail we've been working on for a few years. We have several versions of it across many projects with the same client and so far the results have been very positive. Took a lot of coordination with the buildings at first but it works well. Detail drawings are from another location than what is shown on the picture but it's similar enough.
and the dirty details. I kept the text on. We also did many detailed SketchUp models showing membrane laps and trim/flashing connections but I can't find any now. Originally designed and documented in CAD, current version heading to construction later this summer is in Revit. The detail sheets for this is a small project in itself.
Typ parapet section:
Plan detail:
and if anyone is curious, the picture above is the finished product and not a bad 3D rendering with all the lights off. Pic was taken in winter hence the gloomy look. I cropped out all the snow.
Cool detail. I know detailing parapets can get tricky but I like your C-channel detail.
Thanks WG. we carefully coordinate with the steel fabrication and make sure to dimension the bolt spacing too. I'm currently working on a version that's over 100' long. I have another where the bent-plate C is 2'-6" high.
Still in school, one of the school's projects, no technicality experience.
Balcony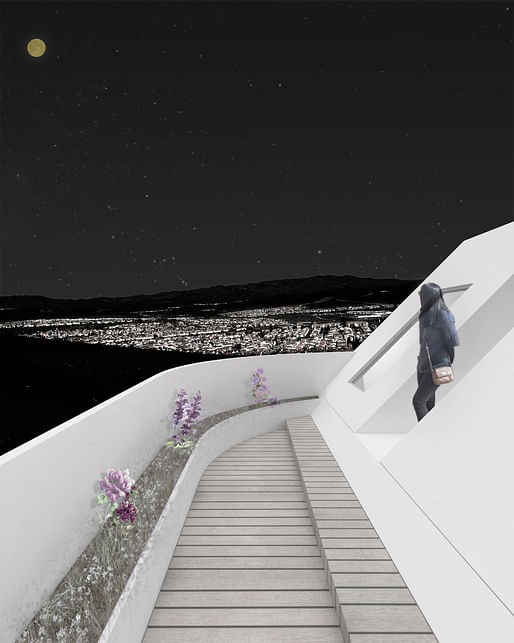
Interior Through window
This is from a few years back. A canopy I did for a very fun reuse project. That counts as a roof, right?
And the detail I'm pretty proud of:
The underside of the canopy is a single plane through the storefront that becomes the underside of a stair landing in the entry atrium. The new structure utilizes holes in the exterior wall from an old canopy. Threading a needle through existing openings at multiple levels. I learned so much here.
If it rains, every canopy is a roof. I see you also struggle with getting camera housings in black.
More like I struggle with getting design-build subs to ask me what color I'd prefer.
With how tight that roof drain piping goes you might end up having to switch to the side outlet drain type, this keeps coming up in projects I've been working on. Otherwise I like. Looks kinda like my drafting.
Very clean detail. I love soffits that continue the ceiling plane, but in cold climates getting a thermal break can be challenging.
Luckily getting warmer every day. ;)
I like the use of master-spec notation.
we're doing master-spec notation finally, was happy to be the guinea pig for those... Still get a lot of "how did you guys coordinate all those spec sections" type questions though... it's been interesting how adding something simple shines a light on who knows their stuff and who doesn't
I have to write (well, "Write", ya know) two specs this week. Small projects, but still...
Good for you guys. Mean While, I got an RFI from the contractor asking to use a different brick tie due to supply issues. And the GC is asking for extra money to cover the cost and blaming it all on Covid. These god damn public bid contractors. New low, man, new low. They even dare to ask. Recently, they also asked for extra cost associated with 10 extra feet of drainage pipe on a $50+M project. The paper work costs more than the pipe.
I'm getting the same nickel & dimes mentality here too. I've got 2 quotes for 2 areas where we needed to extend gypsum board to match a window jamb, or cover a pipe... literally a few inches of material. It's cheaper for the client to just approve it than it is to charge them for my time to review and chase alternative quotes...
Jay - I get stuff like that on a lot of projects. Including the one I posted images of. It happens.
Worst part is I know this GC is trying to build up RFI/change order numbers to use as a defense when they are behind schedule. Building ammunitions in case of lawsuits. Their lawyer by trade partner has been quite involved lately. The government client scared of delay and legal entanglement will probably cave and negotiate a pay out. Tax payers money. Games played over and over.
thank god I'm not the only one not posting pictures and instead dealing with these... thought I was alone for a second
Jay - keep in mind that unless the GC can show and documented how the RFI's / Change Orders impacted the schedule then they are out of luck. It still sucks that you're having to deal with this. :(
this is a house that took 4 years from SD to final, a hellish site, bad soils, foundations heave, bad steel contractors, several design changes, family driven interior design....I'm glad it's finished and the owners are happy.
What is the cost per sf? What is the total?
and this is going right now
jay, about 1400 a foot, total 5.5M.
Great gowd JLC! The last school I did in back in 2019 was $380 a sf. The current fire station I'm working on is $780 sf.
yes, but do they have a climatized custom wine cabinet or a peninsula fireplace with no visible flue? or 15 different types of marble, quartz and granite slabs?
look at this puppy I just found
I recently did a project where the majority of the construction was 350/sqft.... it was just unconditioned storage made of single wythe CMU on a concrete slab and a TPO roof......
JCL - I think a wine cabinet would be overkill in a public school The fireplace, marble, and quartz is just fine!
not even in the teacher's lounge?
Wine cabinets are for private schools only.
The fireplace is in the teachers lounge. It's strictly BYOB though in public schools.
going rogue, macro for contrast to details. i dig all your jobs btw. obvious pros through and through. even if you hate this, i'm always looking for feedback. it ain't your father's utopia.
My advice is to post articles as articles. I'm not going to read a youtube video.
We should definitely invade Canada now. That water is going to be very valuable soon.
Do not forget the Maple Syrup ... and Gun Control ... and nicer people. Oh wait, lets just move there!
Hey there! Sorry.
It’s too cold up
A "Pretty Good House" addition I designed and am helping build for my mother in law. My father in law built their house in the late 1970s, off-grid for financial reasons--it's1/2 mile to the nearest pole--and had the lumber for an addition cut from their land before he passed away in late 2019.
He was a carpenter (and close friend and mentor to me) and would have built it conventionally, on a foundation, but I'm into low-carbon and high performance so it's on helical piers, with a double-framed envelope for good insulation, air-sealing and vapor control.
I tried to find a local builder but the few who were available were not interested in trying something new, so I'm leading construction activities with the help of local carpenters. As construction has progressed I've changed a few details, including using 2x10s for main rafters and moving the air/vapor control layer from the middle of the wall and roof assemblies to the interior, where it won't work as well but it will save time and money for insulation installation.
The project is the lead image for this story: https://www.greenbuildingadvis....
I meant to focus on the roof. The gusseted rafter system is a great way to get a decent amount of insulation up there. The original house has no roof overhang so I matched that detail, but had to add soffit vents--sometimes I like to tuck them under the shadow board as I did here.
Love the red line in the set
Careful with the diagonal siding; popular in the 70's but also very much tends to flow rain down the joints into fenestrations like window and door heads and jambs. My Dad's house (he designed) had that and the jamb flashing took as much water as the head due to moisture channeled down the siding joints.
Thanks, but it's the sheathing, not the siding. I'm a huge nerd about control layers so we'll have a well-detailed WRB and a robust rain screen. Good tip though. A couple of years ago I renovated a 1970s passive solar house with diagonal siding directing water directly onto a door I replaced. Earlier this year they tried to blame me for water infiltration. I reminded them how I strongly recommended redoing the siding and adding a roof overhang, and told them that the door would leak in some conditions if they chose to ignore my recommendations.
Wood Guy - Question about the helical piers.
I was told by a structural engineer that they will only last 20-25 years and that's if they are galvanized. Ungalvanized will only last 15 years. I am assuming this is due to alkaline soil in our area (Colorado).
What has your experience been with the longevity of helical piers in your area?
WG, it's not everyday that you see a project with better-looking sheathing than most other building's cladding.
Chad, I've only been using them for a few years, and I was nervous the first time--a new house directly on the coast, in 2014. Salt air is notorious for eating steel. (I was an employee and not the decision-maker, though I made sure the client knew my concerns.) We talked with the home office and they were confident that we would get at least 50 years out of them. They're hot-dip galvanized but I believe there was an option to upgrade to stainless steel.
With my focus on climate change, I'm pretty sure that in 50 years we'll have bigger issues to deal with than worrying about whether the piers need to be redone, and using piers may help put that day off by a few seconds...
In my area, I would almost always go with stainless steel if it was my choice and not get some cheap-ass contractor changing what is specified. The reason, if it is exposed to moisture (and there is a LOT of it), I would go with stainless steel. Some other materials, like some alloys, where it will have strength as well as resistance to rust or corrosion, then I would consider them. Galvanized anything (hot-dipped is better than not) or zinc-coated anything is garbage and will not last long without corroding. This comes from experience with fasteners. The material will need to be inherently resistant to rusting and corrosion. Non-structural materials, I may consider aluminum.
Where we are, you are basically going to build houses kind of like you would build ships. (Well.... kind of but the idea inferred is being that boats and ships are exposed to moisture and you want to make sure water doesn't compromise the ship. Same idea.)
Ricky - they aren't available in stainless steel.
Are you sure? Maybe not local to where you are. Maybe do a little google search and you might be surprised.
I worked at a firm that used a 316 Stainless structural column. They're fucking expensive. They rust.
Why diagonal sheathing? Structural reasons? Never seen it before.
Diagonal for shear is an old school technique.
SneakyPete, yes, technically all stainless steel will rust over time. The question is, will it rust into rust powder in 15-25 years or will it last 150-250+ years? There are other potential alloys of metals that I may consider but yes, it's "fucking" expensive but it's cheaper than rebuilding your structure every 10 years because it is good for only 15 years, you might as well not design it in the first place let alone build it. Right. When it comes to structure and foundations, that is where the money better be in and not skimped on.
Spoken like someone who's never had a client.
First, I am not interested in designing shit that won't last. Sure, financial considerations would need to be factored in. I didn't say I would necessarily use helical piers. There may be less expensive alternatives that won't compromise my standards where the foundation will last centuries if properly designed. I won't skimp on foundation and structure to build shit that won't last even two decades.
Clients can be bitching moaning and groaning asshats whining about how much it costs because if they only see themselves living there for 5-10 years. If that is how long they only plan to live at a place, they don't belong being property owners in the first place. They should be renters, in that case.
Having a custom home built is a once-in-a-lifetime opportunity for most people who will ever is able to get the financial resources to build one at all. Most people will never be able to afford to have a custom home designed for them.... ever.
It's unrealistic in the United States where only 10% of the population may ever be able to have the money for a custom home designed & built for them. The rest of them are renters and buyers of used homes (like used cars.... homes that had prior owners). Got it.
If a house is going to be built, it needs to last centuries (although some components like roofing, sheathing, etc. might need to be periodically replaced over the life cycle of the structural system and foundation because when the structural or foundation fails, it is the end of life of that building (in other words, its demolished if it can't be properly repaired). Sure, at that point, either a new home or building is built or reconstruction of what was once there, now demolished,... would be built.
Sorry Wood Guy, I didn't mean this to be some dick fight. You have an interesting design and I am not inherently against helical piers. The conditions of the ground geology matter and whether the soil is going to corrode the helical piers/piles too quickly or not is something to consider. I'm looking at the design of structures where the foundation system is perhaps the most important part of a structure that needs to be done right but it's all part of the holistic process of the designing of the structure. The primary structural system is crucial but as with anything carrying load. If it is not done right or if it fails because it has such a short life cycle that is unrealistic for a structure that is intended to have some permanence then yes, it's absolutely important that they last a respectable duration.
SneakyPete, if a prospective client wants garbage buildings that will collapse in 15-25 years then I'll send them your way.
The brand I use is Techno Metal Post, and another brand available locally is Goliath. Neither offers stainless steel as a stock option but the TMP rep said they sometimes have them made. A google search shows that they are available elsewhere.
Of course different grades of stainless steel are good for different things. All will eventually corrode but at slower rates than plain steel. With any type of steel in the ground, you can set up an anode array--sacrificial posts--around the piece you want to protect.
While I would like for my buildings to last hundreds of years, I would also like for our planet to be habitable that long, and part of that means thinking critically about the materials we use. I have done a lot of renovations and have rarely seen a concrete pier that was not broken and deteriorating. TMP offers a 25-year warranty and Goliath offers a 30-year warranty.
Assuming moderately corrosive soil and a slightly low pH of 6.0, which is roughly what we have where I am, and using 3mm steel for the posts, this study shows that the piers should last around 100 years: https://helicalpileworld.com/Dealing_with_Corrosion_-_Kevin_Davies.pdf. (P. 17 of the PDF.)
If you don't want to use them, don't use them, IDGAF. I like them and will continue to use them whenever they are a good solution. Just this morning a contractor building a $180k screened porch addition asked if he could switch my concrete piers to TMPs, and a few days ago a structural engineer for another addition asked if she could do the same.
We used diagonal board sheathing for a few reasons: it's what my FIL had planned to do, and did on his garage I designed and helped him build 25+ years ago. The material was cut on site, which you can't say for any sheet goods. Solid wood holds up much better than OSB or plywood to repeated wetting, which happens to every house in a cold climate that doesn't have a thick layer of exterior insulation. You can burn the offcuts as kindling, an important consideration in an off-grid house heated entirely with wood (and sun).
Wood Guy - Thanks for the info!
I assumed that in your area the helical piers lasted longer than here. I also assumed that they are a completely suitable for you project types.
I've had about a dozen structural engineers out of Denver inform me that they wouldn't use helical / spiral piers / piles for our soil due to the short lifespan. Keep in mind we're doing a lot of public projects were the building will have a lifecycle of 50-100 years.
Chad, according to the table I shared, they should last much longer in alkaline soils than in the acidic soils they have here. But I know that engineers tend to be conservative, and I have worked with some who won't use helical piers because they can't see the soil they are going into.
Thanks for the info, Wood Guy. Where I am, things are actually quite wet (other than the unusually warm summer we have been having this year) and the idea is to determine if the product will be suitable for long-term use at the project location. One thing you can do is employ redundancy in the foundation so if some fail, it isn't a complete and sudden catastrophic failure but it's not clear if that would be viable in your particular project. I do agree with you about wanting the planet to be habitable for hundreds of years. Part of the solution is building buildings to last longer not like the trend we have been doing in more recent years because new construction contributes more to carbon footprint than work on existing buildings. Every time you have to demolish and rebuild is a big impact. So if I can design a building that lasts 5 times longer than it may be lasting with how some of the construction these days are.... it would save in carbon emissions over the same period of time. There is a lot to consider and nothing I said above is meant at all as criticism of you.
Wood Guy - I don't know what to tell you. The engineers we know that have studied this basically told us that the tables from the manufacturer were bunk. They could be wrong but we trust them and it doesn't make sense to doubt them.
A project I worked on at Brooklyn Basin , Oakland, Ca. - Should be complete this fall 2021
Fun fact, it's named Brooklyn after the ship full of Mormons that landed there.
Nothing too groundbreaking here.
I'm surprised to see white-out.... and now that I see it, I can really smell that drawing.
I know someone who almost dies sniffing white out in 7th grade. He survived only to be arrested a few years later for accidentally starting a fire with a bag of flaming dog shit.
Many, many years ago, we were trying to mount some renderings to foam core with spray adhesive, but the nozzle was clogged.
In the process of trying to unclog the sprayer, I managed to give myself a good blast right in the face, to which I laughingly responded, "Well, this reminds me of middle school."
My coworkers both gave me this strange look - they honestly didn't know what I was talking about. Sigh, kids these days... (For the record, I did not actually sniff glue in middle school, but I knew folks who did.)
I didnt think you were referring to glue while talking about middle school :)
It's been a week so let's try a new topic: concrete. What's an interesting detail you're working on that includes concrete, or what's your favorite detail from the past?
I have no interesting recent concrete detailing to show for myself, but I do have a concrete detailing story.
Very early in my career, I worked on a Fire Department training facility. Part of the facility was a building designed to approximate a 2-storey SFR, but constructed entirely of CIP concrete so it could be repeatedly torched and the firefighters could practice running into the burning house to save the baby. The interesting detailing part was that there were gas lines and jets cast into the concrete, so we had to dimensionally locate both the gas lines and every piece of reinforcing or embedment, so they'd all fit. I wish I still had a copy of those drawings.
Now they use prefab 'training buildings' made out steel. Still use gas to provide the flames and smoke. Fire chief described it to me once as a little two story house filled with mini flamethrowers.
You haven't asked for interiors, but I'll add these.
Cute graphics of the stuff that ends up on the plates.
Except that it's all vegan food.
I’m digging those floor tiles.
Here's what I love about these tiles, they're quarry tile, thicker than the normal crap, rugged, and stylish.
@ Beta - do you want to start this week's "Post your work" thread and theme with this project? I kinda liked the idea of doing a new thematic thread every week. Having it all come to this single thread means i almost missed this awesome project!
@b3tadine
That's a very attractive quarry tile, congrats. What manufacturer are they?
I believe porcelain is generally stronger than quarry, and easier/cheaper to install based on the thicknesses. A lot of authorities require quarry in different areas of food service projects, but from what I gather it's sort of an outdated thing.
@arch - I'll do that.
@nate - these are Argelith Tiles, fully vitrified industrial. The tile is 3/4" thick. The existing kitchen has that horrible red quarry tile. Typically when I do commercial kitchens, the two things that don't work for me, or my clients, are tile floors, and pebble finish FRP. I avoid both. This floor tile however, has me rethinking that.
Thats a beautiful interior, b3ta...
Thanks doc! I'll post more tonight, with some more detail...and some lessons learned.
Block this user
Are you sure you want to block this user and hide all related comments throughout the site?
Archinect
This is your first comment on Archinect. Your comment will be visible once approved.