I am designing my first renovation, for a single-family home, within a setback that requires a 1-hr fire rating at the exterior wall. I have the wall figured out but the floor system is intended to be on piers and I'm trying to find a detail that would work. All of the floor-ceiling assemblies I can find are for ceilings or concrete foundations. Am I stuck doing a concrete foundation or is there a workaround?
Non Sequitur
Oct 15, 24 12:29 pm
Are you sure the floor assemblies need a rating due to the setbacks? If so... that's a new one for me.
Almosthip
Oct 15, 24 12:44 pm
If its a bearing wall and its required to have a rating than the supporting assembly is usually required to be rated too. Happens a lot in wood framed construction
.
OddArchitect
Oct 15, 24 12:46 pm
I think it may be because the building is platformed framed and the ceiling / floor is supporting the second story exterior wall.
Wood Guy
Oct 15, 24 12:49 pm
I really don't know. This has been a challenging project, including multiple major re-designs based on a flaky client, and lots of questions to the permitting office because it's within 2' of the property line which is a new thing for me. It took two weeks to get my last question answered and the builder has paused work, waiting for a permit, so I'm trying to get everything right.
In case it's not clear, the concept is a floor exposed from below, and several feet above grade, so from a practical viewpoint it's similar to a projection. But by the letter of both the IRC and IBC I can't find a place that says it's required.
Non Sequitur
Oct 15, 24 12:58 pm
Platform framing answers my question. Any way to have the required FRR on the exterior of wall passing in front of the floor assemblies? Give it it's own structure and you don't have to worry about the floors.
Wood Guy
Oct 15, 24 1:04 pm
I would extend the exterior wall system (5/8" type X plus 1/2" OSB) down over the floor framing. The interior side of the exterior wall is required to have a rating as well, but a fire would not start within the floor assembly so it seems like that might work.
I added a drawing below.
Or do you mean extend the wall system down to grade? That's possible but causes other problems.
Non Sequitur
Oct 15, 24 1:12 pm
WG, in my area, we're only required to FRR the side exposed to fire when dealing with EBF issues along the property line and or setbacks so we get to choose what is easiest. 2x layer 5/8 on inside is cheaper and easier as long as you detail the jambs. Laying a sub floor of FRR sheathing would likely work for me but it's not something I've done before. I'd just cast it in concrete. That exposed floor is going to be cold without a toasty warm basement underneath.
Wood Guy
Oct 15, 24 1:44 pm
We are 14" from the property line so we need to protect both sides of the wall. The builder is my PGH book co-author and neither of us ever do normal assemblies so thick jambs are no problem, if they were allowed on this wall, but they're not.
We both often do R-40 floors over open air and have had no complaints. Our heating degree days are around 7,000 and the design temp is around 5F; you're likely a little colder there.
Because we're so close to the property line, with a non-friendly neighbor, any excavation is going to cause problems. We were hoping that helical piers would work below grade.
Non Sequitur
Oct 15, 24 10:49 pm
WG, exposed floors need to be R60 min here... so yeah, a bit nipplier up here for sure. (actually, I kick-started my house's furnace this evening).
Wood Guy
Oct 16, 24 10:44 am
Wow, R-60, that's a lot! Even our 2021 energy code, which most people think is too restrictive (I disagree) only requires R-30 in floor, or "whatever fits into the floor joists," which means it could be R-19.
Almosthip
Oct 16, 24 11:22 am
Ive had my furnace on for a month already
OddArchitect
Oct 15, 24 12:47 pm
I may not be understanding this correctly as I'm coming from a commercial background.
Is the ceiling / floor in question supporting the rated exterior wall?
Wood Guy
Oct 15, 24 12:51 pm
Yes, it's the left side of this section-in-progress:
Wood Guy
Oct 15, 24 1:00 pm
The image didn't post. I'll post it as a comment below.
poop876
Oct 15, 24 12:57 pm
What is the type of construction? Or are just just trying to find anything except concrete?
Wood Guy
Oct 15, 24 12:58 pm
SFR. Wood-framed on wood posts on helical metal piles or possibly concrete piers.
poop876
Oct 15, 24 1:19 pm
Why would UL L570 not work?
Wood Guy
Oct 15, 24 1:42 pm
It looks like it would. As I said, this is new stuff for me, and the only resources I've been using are the codes and GA-600, the gypsum association handbook.
OddArchitect
Oct 15, 24 1:45 pm
Try UL Product iQ. You have to create an account however it's free and you can search through assemblies.
GA book is still referencing other tests such as UL, which has a lot more information that GA does not show. Most jurisdictions will not accept GA listing and just the actual tests and it's information. I use GA just to flip through and find something that would work then actually list the test number.
natematt
Oct 15, 24 2:38 pm
L570 might be overcomplicating it. That is pretty common for commercial applications as it's intended to meet both fire AND IIC sound requirements. You should be able to find something simpler than this in the prescriptive fire requirements portion of your local code. Perhaps TABLE 721.1 - 21-1.1?
Wood Guy
Oct 15, 24 3:03 pm
I had looked through those and just did again. They all appear to be intended for roofs/ceilings, not floors over open air. 722.6.1 allows you to add up the components yourself so that's what I'm planning on now, with fingers crossed that the plan reviewer accepts it.
natematt
Oct 15, 24 3:15 pm
.
natematt
Oct 15, 24 3:23 pm
They are for floor and roof systems; this is a floor? Where do conclude it can’t be used for an open air condition? (not sure applying gyp in that space would be a good time though)
Wood Guy
Oct 15, 24 5:06 pm
natematt, they all seem to include ceiling details, and the descriptions are either for the interior side or for a floor over a finished space below. Maybe I could substitute gypsum sheathing for the gypsum wallboard described, but these plan reviewers tend to be very specific.
natematt
Oct 16, 24 12:57 pm
I would argue it is categorically listed as floor and roof not ceiling. The products might generally read as ceilings due to the material indication, but to me that is a pretty soft barrier. You can get “gypsum wall-board” rated soffit boards from many manufacturers that should be uncontroversial. I also think you should be able to just use most exterior sheathing products. The building code has a specific ASTM defining gypsum board in chapter 25, so as long as your product meets those requirements and is type X, I think you are pretty explicitly meeting the code.
The beauty of the code prescriptive approach over actual ULs, is that most of the ULs have specific manufacturer products, so it becomes harder to use an exterior appropriate material.
Can you actually install gyp appropriately in that space is another question…
Wood Guy
Oct 15, 24 1:01 pm
Here's a section-in-progress. Wood framed (2x8 studs to meet the energy code). The floor framing is to be on piers because it's nearly impossible to get a concrete foundation placed in this location. And we're trying to save carbon emissions where we can.
Non Sequitur
Oct 15, 24 1:07 pm
Pier is concrete or wood? If concrete, I don't see a problem.
Wood Guy
Oct 15, 24 1:21 pm
My plan was wood posts on concrete footings, but I could do concrete piers up to the floor system.
OddArchitect
Oct 15, 24 1:25 pm
In my opinion, the pier and floor would need to be rated as it's supporting the wall.
poop876
Oct 15, 24 1:27 pm
Yes, I don't see how you can omit rating the pier, floor itself as that is also in the setback, then the wall and overhangs as well. If the floor is not required to be rated, then I would rate the pier, introduce a beam (rate it) then the wall that is being supported by the beam.
OddArchitect
Oct 15, 24 1:29 pm
I don't think it's about the floor being in the setback. In the IBC any construction supporting a rated wall or floor must be rated. The pier and floor appear to be supporting the wall.
I'm not sure if this is different in the IRC.
poop876
Oct 15, 24 1:34 pm
I understand that, but why is the wall rated? As he mentioned above it is because of some setback issue. If the rating is supposed to protect from one side or the other, I don't see how an exposed floor as proposed would not be treated the same way as a wall.
To add, you can design this so the wall is not supported by the floor itself, but by a beam that is rated. Does that mean we don't have to rate the floor as it's not supporting secondary rated members? If the floor is supporting the rated wall it needs to be rated as you said, but if it wasn't supporting the wall I think it needs to be rated as well, just like the wall.
OddArchitect
Oct 15, 24 1:43 pm
I would agree that even if the floor wasn't supporting the wall it should still be rated.
I don't know if in the IRC this would be required. I do think in the IBC it would be. At the very least I think my AHJ would want some type if non-combustible sheathing on the underside of the floor.
JLC-1
Oct 15, 24 2:26 pm
heavy timber is rated 1 hr. 6x6 posts would comply.
Wood Guy
Oct 15, 24 3:07 pm
OA, as far as I can tell, for components that support a floor that is required to be rated, the IRC requires that support to be rated, but it doesn't say anything about what supports walls.
Wood Guy
Oct 15, 24 3:09 pm
Poop, that's a great idea--run a rated beam under the wall and hang the floor joists from that. Not ideal from a thermal point of view but I might find a solution for that.
Wood Guy
Oct 15, 24 3:10 pm
I can't find anywhere in the IRC or IBC where this situation is specifically addressed.
OddArchitect
Oct 15, 24 3:10 pm
That's interesting WG.
Richard Balkins
Oct 15, 24 10:38 pm
There are options as to what you do. I know some buildings, here in Astoria, Oregon are on piers locally. Ideally, you would have the exterior perimeter be made of say, stone. On the exterior wall side, this may be accomplished by some kind of layer of gypsum board or something. One way would be to use masonry attached to the wall and be the exterior finish. This being non-combustible would meet 1 hour rating quick with gypsum wallboard on the interior.
I'd recommend a solid wall... even a stone foundation. Where I am, due to seismic D2 zone, that may be difficult to do a solid stone masonry wall that way but where you are, I don't think you have that seismic zone issue but it could be a way to use something natural and just cut and shaped. You can inset a framing on the inside of that or whatever, if you need to. You can potentially have openings that are perpendicular to the property line which would be treated similarly if an adjacent building was within a fire-separation distance line.
I've seen buildings where they used stone foundation wall on two or three side and such and then part of it being stud framing or post/beam with stud framing and the interior basement level being post/beam (piers) foundation. So, it is conceivable that you could do something similar. Where I am, we'd be hesitant to use pier foundation on new homes unless I have a grade beam (sometimes also serving as a continuous pile cap for perimeter piles) which then may have such walls. Along a property line, we'd probably use a concrete wall system that serves part of the perimeter foundation. Here, that may conveniently also serve as a sort of "retaining wall" system due to our hillside nature. The thing in seismic zone D (D1/D2) is the dislike of isolated footings along building perimeter and along shear wall lines.
I know you would want to avoid concrete as much as possible Wood Guy so there if you are in a low seismic zone area, you may be able to use natural stone. Extract and cut to size is less environmental impact as say the concrete process. You may need concrete at the footing level but use of stone masonry on top of that as a possible option. There may be some other options of non-combustible material or such. It's just throwing thoughts out there but you can check if they suit your project needs and other criteria.
Richard Balkins
Oct 15, 24 10:50 pm
Another old school trick is, if it is possible, acquire a strip of land from the neighboring property... sometimes it might just be 5-ft or something, and merge that piece to the existing lot which then changes the equation of where the property line is. However, I am not clear how close other properties are and if that makes a difference because then you have the other building still within a fire separation distance. In some cases, if the neighboring property's building area (with setback) would cause that building to be more than the fire separation distance requirements under code for 1-hour rated requirements, you might possibly argue if that could be waived in the light of that scenario. I don't know what the neighboring property development and the location of neighboring buildings are to your project site.
Wood Guy
Oct 16, 24 11:07 am
Thanks Rick. The wall is 14" from the property line and the neighbor's narrow driveway, and my client isn't on good terms with them, so we have to be very careful about any excavation and can't use their driveway for any equipment. They certainly wouldn't sell a strip; I asked about that early on.
I do prefer to limit carbon emissions but my rule is to first focus on occupant health and safety, then building durability, and then choose "green" materials when possible. In other words, I would have no problem using concrete here if that were a reasonable option, but it's not.
It's also nearly impossible to get a concrete contractor to show up for a small job here, so this would likely have to be self-performed by the GC, and they don't have much experience with concrete. They would do ICFs if necessary but the short version is we need to limit excavation as much as possible. I have a new solution, locating the piers outside the fire zone and cantilevering beams to support the exterior wall.
Richard Balkins
Oct 16, 24 4:23 pm
I agree. The concern about excavation makes sense given frost depth levels in maine (likely deeper than coastal Oregon) and the correlation with that concern relating to the neighbor and that situation. You will probably need a series of beams running transverse with the joists. I'm assuming you are using i-joists that are equivalent roughly to 2x8 to 2x12 in depth and spaced @ 16" o.c.. The beams should probably be at least 6x12. Maybe 8x12 beams at a spacing of about 8-ft. to 12-ft. o.c.. The supporting post being say, 4-ft. or abouts from the outside face of the wall line. Which should align about where the I-joist #4 from left to right is going down. This would be a long cantilever span. You may need a non-combustible brace beam connecting from bottom of that 6x12 or 8x12 beam or whatever (likely under I-joist #2, from left to right) and that it would be supported by post(s) under i-joist #4 from left to right. The brace beam would connect to the post(s) under I-joist #4 (from left to right) at a point near grade... maybe 3"-6" above grade). Kind of an engineering trick based on those craftsman brackets but of larger scale and actual structural purpose (as sometimes those on craftsman bungalows were really of decorative purpose than actual structural purpose but we would be dealing with actual structural purpose. This is an idea that you may need to consult an engineer on. Just an idea.
Richard Balkins
Oct 16, 24 4:31 pm
You may need another set of posts under the 6x12 or 8x 12 beam(s) vertically aligned to i-joist #8 (from left to right). I just wouldn't typically cantilever structural wood beams or a standard I-beam or H-beam (steel) more than ~2x the depth of the beam from top to bottom. 4x or more is considerable cantilevering distances.
Wood Guy
Oct 15, 24 5:09 pm
My current thinking is that what I want to do is not allowed; the IRC forbids having penetrations or openings in a wall this close to the property line, and this could be conceived of as a large wall with a large opening. I have put the question to my client and the builder, whether they want me to submit what we'd like to do and hope for the best, or change gears and use a full wall, which would likely have to be a framed wall sitting on piers at grade. Thanks everyone for your help and I'll keep you updated.
We're less than 2' from the property line, and the building will be sprinklered.
gwharton
Oct 15, 24 6:29 pm
I think you've got that right: the jurisdiction is treating that space as a wall opening. I've seen similar requirements on multifamily projects with balconies extending close to setbacks. You might be able to get around it by making everything within 5 feet of the property line non-combustible, but I suspect that's not a viable answer for what you're trying to do. Taking the wall all the way down to dirt is probably the only reasonable answer.
Non Sequitur
Oct 15, 24 6:43 pm
This type of restriction starts at 2’? We have similar rules but it’s 1.2m or less (4 freedom ferries).
OddArchitect
Oct 15, 24 6:49 pm
Um, actually that's 3'-11 7/8" in freedom units. ;)
GH, this was supposed to be a mostly-interior renovation to a kitchen wing off the main house. The contractor decided to fully gut the interior and expose the crawl space framing, and said it's all junk and needs to come down, and our client agreed. Because it's non-conforming regarding setbacks, I have to stay within the original exterior dimensions, with thicker walls and ceiling eating into the space, and we have to meet current energy codes which are the 2021 IECC. And none of this was in the budget so I'm doing my best to keep it as affordable as I can. Stupid old houses...
gwharton
Oct 16, 24 12:23 pm
Does a 2x6 wall with blown-in insulation not meet the required U value on performance based design? I find that surprising. What climate zone is this?
OddArchitect
Oct 16, 24 1:05 pm
If you use the total building performance method with COMcheck or REScheck it should work up to climate zone 6. I think WG said the walls are 2 x 8 though.
gwharton
Oct 16, 24 1:14 pm
Right. I saw his complaint about the thickness of the walls, hence my question about going to 2x6. 2x8 wall framing is also significantly more expensive than 2x6. Another option might be to do a 2x8 plate with staggered 2x4 studs. That would be even better thermal performance if the structural engineer is okay with it.
Wood Guy
Oct 16, 24 4:59 pm
I did my own calcs, including the framing, and found that I had to use 2x8s to meet our 2021 EICC requirements of U≤0.045. (climate zone 6.) I have not used REScheck to try to get away with less. Both the builder and I primarily do high-performance projects, and that's one of the main reasons our client hired us.
My comment above was not complaining about the thickness, but responding to what I thought non-combustible meant, which apparently is both truly non-combustible or combustible materials covered with something non-combustible. That doesn't match what the IRC says, which I'm very familiar with, and no matter how hard I try I don't seem to understand the IBC rules.
rightangledevelopers
Oct 16, 24 5:05 am
To create a 1-hour fire-rated floor on piers, it's crucial to use materials and construction methods that meet fire resistance standards. Utilizing fire-resistant materials such as gypsum boards or intumescent coatings can be beneficial. It's important to ensure proper insulation and fire-stopping techniques are used to preserve the structural integrity of the floor system
poop876
Oct 16, 24 7:54 am
No shit!
Wood Guy
Oct 16, 24 10:27 am
I smell A.I....
OddArchitect
Oct 16, 24 10:30 am
A foolish and uninformed AI . . .
joseffischer
Oct 16, 24 9:26 am
Perhaps I'm the lone person of a slightly different opinion. I can only say what I've experienced in Georgia when doing housing and coming across this issue. We do a lot of brick/block piers and crawlspace with brick veneer and/or siding. We've dealt with being too close to the property line often. We have a nice fire-rated sheathing system that handles the wall assembly with ULs for the assembly we use.
For the floors we do NOT rate them. we build the rim joists fat and fully bearing on the piers below and tie the joists with hangers as typ treating it like the beam/ledger it is. The AHJs consider the walls bearing on the beams and which are bearing on the piers, so all that has to be rated, but the floors don't have to be.
This makes sense to me from the intent as well. In a fire even if the floors burn out/thru and the entire house goes up, the walls remain in place on the piers and the fires get put out, leaving a shell and containing the fire from jumping across the property line.
Wood Guy
Oct 16, 24 10:34 am
Interesting perspective! For energy and condensation reasons (practically, not code-related) I need insulation between the beams and the interior floor but I have 8" walls to meet our energy code so something like a 4x12 beam would work, if wrapped in gyp-board.
OddArchitect
Oct 16, 24 10:43 am
That's what we've done as well joseffischer.
Wood Guy
Oct 16, 24 11:11 am
In a comment above, JLC noted that 6x6s are rated for 1-hr. I have scoured the IBC and have read and reread the section on heavy timber but I can't find where that is stated explicitly. Any help?
I'm sorry that I'm dumb about this stuff. Once we get through this, I won't be!
OddArchitect
Oct 16, 24 11:20 am
Check section 722 Calculated Fire Resistance. Some things may be in table 721.1. Don't ask me why table 721.1 is in section 722.
Wood Guy
Oct 16, 24 11:41 am
haha, they appear to have fixed that in the 2021 code. And thank you.
betonbrut
Oct 16, 24 11:44 am
The tested theory is that mass timber will slowly and predictably burn. I think it is generally 1" per hour. So you are upsizing the wood members by 1" per hour of rating needed.
Wood Guy
Oct 16, 24 11:54 am
BB, I've heard that in various places, but I can't find a code reference. I just looked through the tables that OA mentioned for the umpteenth time and I don't see it mentioned there. IBC table 2304.11 shows the required minimum size of heavy timbers but it doesn't mention the fire rating. Maybe it's supposed to be implied?
OddArchitect
Oct 16, 24 12:04 pm
I looked an couldn't find it either WG. Could it be in the new mass timber section (IBC 2021?)
joseffischer
Oct 16, 24 12:09 pm
commercially, when working on old-school HT buildings, our structural engineer handled actual sizing to confirm safety even "after-burn". My understanding is that the calcs/tests are covered under ASTM E119, or Canadian ULC S101... but I actually don't know how that works. On my most recent project 3 years ago as example, we replaced a bunch of doweled HT decking with 3 1/2" boards and covered the top with 3/4" hardwood over sound board. 3 1/2" is the minimum required and spanned 10' max. I didn't think to ask what that meant in the midst of a fire event after 60 minutes for the occupants.
We were replacing because of a fire event uncovered/unforeseen that had burned the bottom of the existing floor to approx 2-2 1/2". All of that had been covered up with suspended ceiling decades earlier and occupied for the length of time. It was both a structural and aesthetic concern for the project since we were putting things back to expose the timber.
joseffischer
Oct 16, 24 12:11 pm
If anyone has more direct info about the testing for confirmation, I'd love to know as well.
joseffischer
Oct 16, 24 12:13 pm
sorry for the 3-post... check the National Design Specification for wood construction referenced in the IBC, chapter 16, for burn rate characteristics and loading under burnt conditions.
from NDS ch 16 - calc based on shape in red, final size based on added thickness from table 6
joseffischer
Oct 16, 24 12:24 pm
so a 10x10 post would be 9.25"-3.6" for effective loading of 5.65" of support post burn.
OddArchitect
Oct 16, 24 12:48 pm
Has that been recognized by the IBC?
betonbrut
Oct 16, 24 1:08 pm
Yes, in the 2021 code they have changed type IV construction to IV-a and IV-b.
In IV-b, you have to oversize the mass timber elements to achieve the rating. in IV-a, you have to conceal the mass timber with something non-combustible.
Wood Guy
Oct 16, 24 1:17 pm
I guess that's a key question, and probably a dumb one. In the IRC, "non-combustible" basically means masonry. A fire-resistant covering over wood framing is not "non-combustible."
In the IBC, does "non-combustible" include a fire-resistant covering over wood framing--i.e., is typical SFR wood-based platform framing considered type IV construction?
OddArchitect
Oct 16, 24 1:26 pm
In the IBC non-combustible means it cannot burn. However, you can have a rated assembly using materials that are both non-combustible and combustible. IE gwb over wood.
smaarch
Oct 16, 24 6:23 pm
I've read thru some but not all the comments- your section was the most helpful. Generally the code attitude is that perpendicular surfaces to the fire line need to be rated. To my mind this presents a few problems for you.
1. The lower and upper terminations of the wall
2. The piers need to be rated
3. The floor does not need to be rated but it would be a good idea and maybe save some laborious effort on wall floor connection
4. The area above the wall top plate also needs to be rated - that's a potentially difficult detail
I'm assuming you are aware of the USG Handbook and the UL Directory?
OddArchitect
Oct 17, 24 11:12 am
I think the floor needs to be rated if it's supporting the rated wall.
Wood Guy
Oct 17, 24 1:26 pm
Thank you, yes I have the USG handbook as well as the GA-600 book, and others here have let me know about the UL directory.
Wood Guy
Oct 17, 24 1:30 pm
Thank you everyone. To keep things relatively simple, I'm going to do a skirting on the side in question that is fire-rated. There are reasons I was resisting that approach but it's going to be far easier than the other systems. I'm not sure what the city will say about the roof directly over the wall but I think I'll submit what I would normally do and we can adjust it if they say we have to. The nearest house is 14' feet away and the fire station is around the corner so I'm not super concerned about the actual risk of fire, but I do want to protect my liability to a reasonable degree.
gwharton
Oct 17, 24 1:35 pm
Thanks for the update. I look forward to hearing how that turns out. Another possibility, if you reach a roadblock with the city, is to approach the neighbor about buying a no-build easement adjacent to this structure to make the effective property line setback 5 feet from a building code standpoint. I've had to do this a couple of times in the past where all other options failed.
Wood Guy
Oct 17, 24 2:20 pm
Thanks GH. I think I mentioned somewhere above that my client isn't on very good terms with the neighbor. I had initially suggested buying a strip of land or an easement to make this and other things easier, but they said it's not an option.
If I were my client, I would tear the house down and move it away from the property line; they have a double lot and plenty of space to do so. They didn't want to spend the money, but with the many change orders for additional work they have incurred, they will have spent almost as money to get a much worse house. What can you do...
I am designing my first renovation, for a single-family home, within a setback that requires a 1-hr fire rating at the exterior wall. I have the wall figured out but the floor system is intended to be on piers and I'm trying to find a detail that would work. All of the floor-ceiling assemblies I can find are for ceilings or concrete foundations. Am I stuck doing a concrete foundation or is there a workaround?
Are you sure the floor assemblies need a rating due to the setbacks? If so... that's a new one for me.
If its a bearing wall and its required to have a rating than the supporting assembly is usually required to be rated too. Happens a lot in wood framed construction .
I think it may be because the building is platformed framed and the ceiling / floor is supporting the second story exterior wall.
I really don't know. This has been a challenging project, including multiple major re-designs based on a flaky client, and lots of questions to the permitting office because it's within 2' of the property line which is a new thing for me. It took two weeks to get my last question answered and the builder has paused work, waiting for a permit, so I'm trying to get everything right.
In case it's not clear, the concept is a floor exposed from below, and several feet above grade, so from a practical viewpoint it's similar to a projection. But by the letter of both the IRC and IBC I can't find a place that says it's required.
Platform framing answers my question. Any way to have the required FRR on the exterior of wall passing in front of the floor assemblies? Give it it's own structure and you don't have to worry about the floors.
I would extend the exterior wall system (5/8" type X plus 1/2" OSB) down over the floor framing. The interior side of the exterior wall is required to have a rating as well, but a fire would not start within the floor assembly so it seems like that might work.
I added a drawing below.
Or do you mean extend the wall system down to grade? That's possible but causes other problems.
WG, in my area, we're only required to FRR the side exposed to fire when dealing with EBF issues along the property line and or setbacks so we get to choose what is easiest. 2x layer 5/8 on inside is cheaper and easier as long as you detail the jambs. Laying a sub floor of FRR sheathing would likely work for me but it's not something I've done before. I'd just cast it in concrete. That exposed floor is going to be cold without a toasty warm basement underneath.
We are 14" from the property line so we need to protect both sides of the wall. The builder is my PGH book co-author and neither of us ever do normal assemblies so thick jambs are no problem, if they were allowed on this wall, but they're not.
We both often do R-40 floors over open air and have had no complaints. Our heating degree days are around 7,000 and the design temp is around 5F; you're likely a little colder there.
Because we're so close to the property line, with a non-friendly neighbor, any excavation is going to cause problems. We were hoping that helical piers would work below grade.
WG, exposed floors need to be R60 min here... so yeah, a bit nipplier up here for sure. (actually, I kick-started my house's furnace this evening).
Wow, R-60, that's a lot! Even our 2021 energy code, which most people think is too restrictive (I disagree) only requires R-30 in floor, or "whatever fits into the floor joists," which means it could be R-19.
Ive had my furnace on for a month already
I may not be understanding this correctly as I'm coming from a commercial background.
Is the ceiling / floor in question supporting the rated exterior wall?
Yes, it's the left side of this section-in-progress:
The image didn't post. I'll post it as a comment below.
What is the type of construction? Or are just just trying to find anything except concrete?
SFR. Wood-framed on wood posts on helical metal piles or possibly concrete piers.
Why would UL L570 not work?
It looks like it would. As I said, this is new stuff for me, and the only resources I've been using are the codes and GA-600, the gypsum association handbook.
Try UL Product iQ. You have to create an account however it's free and you can search through assemblies.
https://iq2.ulprospector.com/s...
GA book is still referencing other tests such as UL, which has a lot more information that GA does not show. Most jurisdictions will not accept GA listing and just the actual tests and it's information. I use GA just to flip through and find something that would work then actually list the test number.
L570 might be overcomplicating it. That is pretty common for commercial applications as it's intended to meet both fire AND IIC sound requirements. You should be able to find something simpler than this in the prescriptive fire requirements portion of your local code. Perhaps TABLE 721.1 - 21-1.1?
I had looked through those and just did again. They all appear to be intended for roofs/ceilings, not floors over open air. 722.6.1 allows you to add up the components yourself so that's what I'm planning on now, with fingers crossed that the plan reviewer accepts it.
.
They are for floor and roof systems; this is a floor? Where do conclude it can’t be used for an open air condition? (not sure applying gyp in that space would be a good time though)
natematt, they all seem to include ceiling details, and the descriptions are either for the interior side or for a floor over a finished space below. Maybe I could substitute gypsum sheathing for the gypsum wallboard described, but these plan reviewers tend to be very specific.
I would argue it is categorically listed as floor and roof not ceiling. The products might generally read as ceilings due to the material indication, but to me that is a pretty soft barrier. You can get “gypsum wall-board” rated soffit boards from many manufacturers that should be uncontroversial. I also think you should be able to just use most exterior sheathing products. The building code has a specific ASTM defining gypsum board in chapter 25, so as long as your product meets those requirements and is type X, I think you are pretty explicitly meeting the code. The beauty of the code prescriptive approach over actual ULs, is that most of the ULs have specific manufacturer products, so it becomes harder to use an exterior appropriate material. Can you actually install gyp appropriately in that space is another question…
Here's a section-in-progress. Wood framed (2x8 studs to meet the energy code). The floor framing is to be on piers because it's nearly impossible to get a concrete foundation placed in this location. And we're trying to save carbon emissions where we can.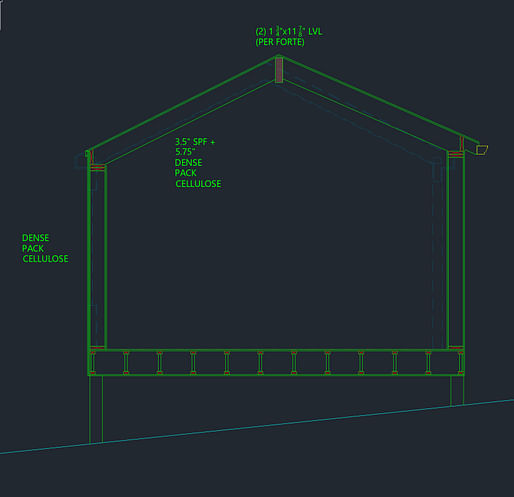
Pier is concrete or wood? If concrete, I don't see a problem.
My plan was wood posts on concrete footings, but I could do concrete piers up to the floor system.
In my opinion, the pier and floor would need to be rated as it's supporting the wall.
Yes, I don't see how you can omit rating the pier, floor itself as that is also in the setback, then the wall and overhangs as well. If the floor is not required to be rated, then I would rate the pier, introduce a beam (rate it) then the wall that is being supported by the beam.
I don't think it's about the floor being in the setback. In the IBC any construction supporting a rated wall or floor must be rated. The pier and floor appear to be supporting the wall.
I'm not sure if this is different in the IRC.
I understand that, but why is the wall rated? As he mentioned above it is because of some setback issue. If the rating is supposed to protect from one side or the other, I don't see how an exposed floor as proposed would not be treated the same way as a wall.
To add, you can design this so the wall is not supported by the floor itself, but by a beam that is rated. Does that mean we don't have to rate the floor as it's not supporting secondary rated members? If the floor is supporting the rated wall it needs to be rated as you said, but if it wasn't supporting the wall I think it needs to be rated as well, just like the wall.
I would agree that even if the floor wasn't supporting the wall it should still be rated.
I don't know if in the IRC this would be required. I do think in the IBC it would be. At the very least I think my AHJ would want some type if non-combustible sheathing on the underside of the floor.
heavy timber is rated 1 hr. 6x6 posts would comply.
OA, as far as I can tell, for components that support a floor that is required to be rated, the IRC requires that support to be rated, but it doesn't say anything about what supports walls.
Poop, that's a great idea--run a rated beam under the wall and hang the floor joists from that. Not ideal from a thermal point of view but I might find a solution for that.
I can't find anywhere in the IRC or IBC where this situation is specifically addressed.
That's interesting WG.
There are options as to what you do. I know some buildings, here in Astoria, Oregon are on piers locally. Ideally, you would have the exterior perimeter be made of say, stone. On the exterior wall side, this may be accomplished by some kind of layer of gypsum board or something. One way would be to use masonry attached to the wall and be the exterior finish. This being non-combustible would meet 1 hour rating quick with gypsum wallboard on the interior.
I'd recommend a solid wall... even a stone foundation. Where I am, due to seismic D2 zone, that may be difficult to do a solid stone masonry wall that way but where you are, I don't think you have that seismic zone issue but it could be a way to use something natural and just cut and shaped. You can inset a framing on the inside of that or whatever, if you need to. You can potentially have openings that are perpendicular to the property line which would be treated similarly if an adjacent building was within a fire-separation distance line.
I've seen buildings where they used stone foundation wall on two or three side and such and then part of it being stud framing or post/beam with stud framing and the interior basement level being post/beam (piers) foundation. So, it is conceivable that you could do something similar. Where I am, we'd be hesitant to use pier foundation on new homes unless I have a grade beam (sometimes also serving as a continuous pile cap for perimeter piles) which then may have such walls. Along a property line, we'd probably use a concrete wall system that serves part of the perimeter foundation. Here, that may conveniently also serve as a sort of "retaining wall" system due to our hillside nature. The thing in seismic zone D (D1/D2) is the dislike of isolated footings along building perimeter and along shear wall lines.
I know you would want to avoid concrete as much as possible Wood Guy so there if you are in a low seismic zone area, you may be able to use natural stone. Extract and cut to size is less environmental impact as say the concrete process. You may need concrete at the footing level but use of stone masonry on top of that as a possible option. There may be some other options of non-combustible material or such. It's just throwing thoughts out there but you can check if they suit your project needs and other criteria.
Another old school trick is, if it is possible, acquire a strip of land from the neighboring property... sometimes it might just be 5-ft or something, and merge that piece to the existing lot which then changes the equation of where the property line is. However, I am not clear how close other properties are and if that makes a difference because then you have the other building still within a fire separation distance. In some cases, if the neighboring property's building area (with setback) would cause that building to be more than the fire separation distance requirements under code for 1-hour rated requirements, you might possibly argue if that could be waived in the light of that scenario. I don't know what the neighboring property development and the location of neighboring buildings are to your project site.
Thanks Rick. The wall is 14" from the property line and the neighbor's narrow driveway, and my client isn't on good terms with them, so we have to be very careful about any excavation and can't use their driveway for any equipment. They certainly wouldn't sell a strip; I asked about that early on.
I do prefer to limit carbon emissions but my rule is to first focus on occupant health and safety, then building durability, and then choose "green" materials when possible. In other words, I would have no problem using concrete here if that were a reasonable option, but it's not.
It's also nearly impossible to get a concrete contractor to show up for a small job here, so this would likely have to be self-performed by the GC, and they don't have much experience with concrete. They would do ICFs if necessary but the short version is we need to limit excavation as much as possible. I have a new solution, locating the piers outside the fire zone and cantilevering beams to support the exterior wall.
I agree. The concern about excavation makes sense given frost depth levels in maine (likely deeper than coastal Oregon) and the correlation with that concern relating to the neighbor and that situation. You will probably need a series of beams running transverse with the joists. I'm assuming you are using i-joists that are equivalent roughly to 2x8 to 2x12 in depth and spaced @ 16" o.c.. The beams should probably be at least 6x12. Maybe 8x12 beams at a spacing of about 8-ft. to 12-ft. o.c.. The supporting post being say, 4-ft. or abouts from the outside face of the wall line. Which should align about where the I-joist #4 from left to right is going down. This would be a long cantilever span. You may need a non-combustible brace beam connecting from bottom of that 6x12 or 8x12 beam or whatever (likely under I-joist #2, from left to right) and that it would be supported by post(s) under i-joist #4 from left to right. The brace beam would connect to the post(s) under I-joist #4 (from left to right) at a point near grade... maybe 3"-6" above grade). Kind of an engineering trick based on those craftsman brackets but of larger scale and actual structural purpose (as sometimes those on craftsman bungalows were really of decorative purpose than actual structural purpose but we would be dealing with actual structural purpose. This is an idea that you may need to consult an engineer on. Just an idea.
You may need another set of posts under the 6x12 or 8x 12 beam(s) vertically aligned to i-joist #8 (from left to right). I just wouldn't typically cantilever structural wood beams or a standard I-beam or H-beam (steel) more than ~2x the depth of the beam from top to bottom. 4x or more is considerable cantilevering distances.
My current thinking is that what I want to do is not allowed; the IRC forbids having penetrations or openings in a wall this close to the property line, and this could be conceived of as a large wall with a large opening. I have put the question to my client and the builder, whether they want me to submit what we'd like to do and hope for the best, or change gears and use a full wall, which would likely have to be a framed wall sitting on piers at grade. Thanks everyone for your help and I'll keep you updated.
We're less than 2' from the property line, and the building will be sprinklered.
I think you've got that right: the jurisdiction is treating that space as a wall opening. I've seen similar requirements on multifamily projects with balconies extending close to setbacks. You might be able to get around it by making everything within 5 feet of the property line non-combustible, but I suspect that's not a viable answer for what you're trying to do. Taking the wall all the way down to dirt is probably the only reasonable answer.
This type of restriction starts at 2’? We have similar rules but it’s 1.2m or less (4 freedom ferries).
Um, actually that's 3'-11 7/8" in freedom units. ;)
Non, that's for sprinklered 1-and 2-family homes. Non-sprinklered homes have slightly more restrictive rules--table R302.1(1): https://codes.iccsafe.org/content/IRC2021P1/chapter-3-building-planning#IRC2021P1_Pt03_Ch03_SecR302
GH, this was supposed to be a mostly-interior renovation to a kitchen wing off the main house. The contractor decided to fully gut the interior and expose the crawl space framing, and said it's all junk and needs to come down, and our client agreed. Because it's non-conforming regarding setbacks, I have to stay within the original exterior dimensions, with thicker walls and ceiling eating into the space, and we have to meet current energy codes which are the 2021 IECC. And none of this was in the budget so I'm doing my best to keep it as affordable as I can. Stupid old houses...
Does a 2x6 wall with blown-in insulation not meet the required U value on performance based design? I find that surprising. What climate zone is this?
If you use the total building performance method with COMcheck or REScheck it should work up to climate zone 6. I think WG said the walls are 2 x 8 though.
Right. I saw his complaint about the thickness of the walls, hence my question about going to 2x6. 2x8 wall framing is also significantly more expensive than 2x6. Another option might be to do a 2x8 plate with staggered 2x4 studs. That would be even better thermal performance if the structural engineer is okay with it.
I did my own calcs, including the framing, and found that I had to use 2x8s to meet our 2021 EICC requirements of U≤0.045. (climate zone 6.) I have not used REScheck to try to get away with less. Both the builder and I primarily do high-performance projects, and that's one of the main reasons our client hired us.
My comment above was not complaining about the thickness, but responding to what I thought non-combustible meant, which apparently is both truly non-combustible or combustible materials covered with something non-combustible. That doesn't match what the IRC says, which I'm very familiar with, and no matter how hard I try I don't seem to understand the IBC rules.
To create a 1-hour fire-rated floor on piers, it's crucial to use materials and construction methods that meet fire resistance standards. Utilizing fire-resistant materials such as gypsum boards or intumescent coatings can be beneficial. It's important to ensure proper insulation and fire-stopping techniques are used to preserve the structural integrity of the floor system
No shit!
I smell A.I....
A foolish and uninformed AI . . .
Perhaps I'm the lone person of a slightly different opinion. I can only say what I've experienced in Georgia when doing housing and coming across this issue. We do a lot of brick/block piers and crawlspace with brick veneer and/or siding. We've dealt with being too close to the property line often. We have a nice fire-rated sheathing system that handles the wall assembly with ULs for the assembly we use.
For the floors we do NOT rate them. we build the rim joists fat and fully bearing on the piers below and tie the joists with hangers as typ treating it like the beam/ledger it is. The AHJs consider the walls bearing on the beams and which are bearing on the piers, so all that has to be rated, but the floors don't have to be.
This makes sense to me from the intent as well. In a fire even if the floors burn out/thru and the entire house goes up, the walls remain in place on the piers and the fires get put out, leaving a shell and containing the fire from jumping across the property line.
Interesting perspective! For energy and condensation reasons (practically, not code-related) I need insulation between the beams and the interior floor but I have 8" walls to meet our energy code so something like a 4x12 beam would work, if wrapped in gyp-board.
That's what we've done as well joseffischer.
In a comment above, JLC noted that 6x6s are rated for 1-hr. I have scoured the IBC and have read and reread the section on heavy timber but I can't find where that is stated explicitly. Any help?
I'm sorry that I'm dumb about this stuff. Once we get through this, I won't be!
Check section 722 Calculated Fire Resistance. Some things may be in table 721.1. Don't ask me why table 721.1 is in section 722.
haha, they appear to have fixed that in the 2021 code. And thank you.
The tested theory is that mass timber will slowly and predictably burn. I think it is generally 1" per hour. So you are upsizing the wood members by 1" per hour of rating needed.
BB, I've heard that in various places, but I can't find a code reference. I just looked through the tables that OA mentioned for the umpteenth time and I don't see it mentioned there. IBC table 2304.11 shows the required minimum size of heavy timbers but it doesn't mention the fire rating. Maybe it's supposed to be implied?
I looked an couldn't find it either WG. Could it be in the new mass timber section (IBC 2021?)
commercially, when working on old-school HT buildings, our structural engineer handled actual sizing to confirm safety even "after-burn". My understanding is that the calcs/tests are covered under ASTM E119, or Canadian ULC S101... but I actually don't know how that works. On my most recent project 3 years ago as example, we replaced a bunch of doweled HT decking with 3 1/2" boards and covered the top with 3/4" hardwood over sound board. 3 1/2" is the minimum required and spanned 10' max. I didn't think to ask what that meant in the midst of a fire event after 60 minutes for the occupants.
We were replacing because of a fire event uncovered/unforeseen that had burned the bottom of the existing floor to approx 2-2 1/2". All of that had been covered up with suspended ceiling decades earlier and occupied for the length of time. It was both a structural and aesthetic concern for the project since we were putting things back to expose the timber.
If anyone has more direct info about the testing for confirmation, I'd love to know as well.
sorry for the 3-post... check the National Design Specification for wood construction referenced in the IBC, chapter 16, for burn rate characteristics and loading under burnt conditions.
That's what I've been looking at. Not that I can find. https://codes.iccsafe.org/content/IBC2021P2/chapter-23-wood#IBC2021P2_Ch23_Sec2304.11
That's IBC, not NDS, NDS has the actual calcs that I assume the struct eng must use
here's a long paper from the wood products council https://www.woodworks.org/wp-content/uploads/Wood_Solution_Paper-Fire-Design-of-Mass-Timber-Members-WoodWorks-Apr-2019.pdf
and the referenced ibc section https://codes.iccsafe.org/cont...
look at table 601
Specifically, keynote c.
A nominal 6x6 wood pier / column wouldn't get a 1 hour rating though. It's not meeting the min size requirements for combined floor and roof loads.
Sorry Jose, I was responding to OA above and hadn't seen your comments yet.
so a 10x10 post would be 9.25"-3.6" for effective loading of 5.65" of support post burn.
Has that been recognized by the IBC?
Yes, in the 2021 code they have changed type IV construction to IV-a and IV-b. In IV-b, you have to oversize the mass timber elements to achieve the rating. in IV-a, you have to conceal the mass timber with something non-combustible.
I guess that's a key question, and probably a dumb one. In the IRC, "non-combustible" basically means masonry. A fire-resistant covering over wood framing is not "non-combustible."
In the IBC, does "non-combustible" include a fire-resistant covering over wood framing--i.e., is typical SFR wood-based platform framing considered type IV construction?
In the IBC non-combustible means it cannot burn. However, you can have a rated assembly using materials that are both non-combustible and combustible. IE gwb over wood.
I've read thru some but not all the comments- your section was the most helpful. Generally the code attitude is that perpendicular surfaces to the fire line need to be rated.
To my mind this presents a few problems for you.
1. The lower and upper terminations of the wall
2. The piers need to be rated
3. The floor does not need to be rated but it would be a good idea and maybe save some laborious effort on wall floor connection
4. The area above the wall top plate also needs to be rated - that's a potentially difficult detail
I'm assuming you are aware of the USG Handbook and the UL Directory?
I think the floor needs to be rated if it's supporting the rated wall.
Thank you, yes I have the USG handbook as well as the GA-600 book, and others here have let me know about the UL directory.
Thank you everyone. To keep things relatively simple, I'm going to do a skirting on the side in question that is fire-rated. There are reasons I was resisting that approach but it's going to be far easier than the other systems. I'm not sure what the city will say about the roof directly over the wall but I think I'll submit what I would normally do and we can adjust it if they say we have to. The nearest house is 14' feet away and the fire station is around the corner so I'm not super concerned about the actual risk of fire, but I do want to protect my liability to a reasonable degree.
Thanks for the update. I look forward to hearing how that turns out. Another possibility, if you reach a roadblock with the city, is to approach the neighbor about buying a no-build easement adjacent to this structure to make the effective property line setback 5 feet from a building code standpoint. I've had to do this a couple of times in the past where all other options failed.
Thanks GH. I think I mentioned somewhere above that my client isn't on very good terms with the neighbor. I had initially suggested buying a strip of land or an easement to make this and other things easier, but they said it's not an option.
If I were my client, I would tear the house down and move it away from the property line; they have a double lot and plenty of space to do so. They didn't want to spend the money, but with the many change orders for additional work they have incurred, they will have spent almost as money to get a much worse house. What can you do...